A Look at Ergonomics in the Distribution Center
Think for a moment about your personal definition of productivity. Words like “effectiveness” and “output” and “production” likely come to mind.
But what we often forget in material handling is that productivity doesn’t have to mean harder work. In fact, in manufacturing operations and distribution facilities, higher productivity often means less demanding physical work, employee touches, and interactions between product and personnel.
What do we mean by this?
The answer lies in ergonomics, the science of designing the job to fit the worker instead of physically forcing the worker’s body to fit the job. According to the Occupational Health & Safety Administration, ergonomics helps lessen muscle fatigue, increases productivity, and reduces the number and severity of work-related musculoskeletal disorders (MSDs).
Let’s take a look at the relationship between ergonomics and productivity in the distribution center:
Decreased Risk of Injury
In the distribution center, workplace injuries aren’t just detrimental to employee health and safety; they can also have a significant impact on productivity. With workers sidelined and unable to work, companies face serious productivity losses – not to mention costly worker compensation insurance premiums.
In addition to serious injuries such as falls, slips, and trips, warehouse workers run the risk of developing MSDs, including muscle strains, lower back injuries, carpal tunnel syndrome, tendinitis, and more. U.S. Bureau of Labor Statistics data, in fact, shows MSDs are twice as common in the warehousing and distribution sector as they are in other private-sector industries.
Enter workplace ergonomics. Ergonomics is not a feel-good factor, but instead the linchpin in designing work processes and workplaces. Ergonomics not only contributes to the well-being and relief of the staff but also brings measurable and distinct advances in productivity.
Here are a handful of actionable tips for distribution centers to drive productivity gains with ergonomics:
- Review worker tasks for risk factors (awkward/static postures, repetitive/quick motions, excessive force, compression or contact stress, etc.).
- Control risk factors with ergonomic solutions (adjustable height workstations, anti-fatigue mats, lifts or hoists to reduce awkward positions, etc.).
- Understand how to make the workplace work ergonomically (issues frequently encountered include work surfaces that are the wrong size or at the wrong height, uncomfortable chairs, shelves and bins that are too high or out of reach, and awkward hand tools).
- Continually monitor workflow and make ergonomic improvements as necessary.
Reduced Travel Time
Aside from making ergonomic adjustments to workstations while workers are standing in place, it’s also critical to factor in how much a worker needs to move around the warehouse in order to perform industrial tasks.
Let’s take order picking, for example. In a distribution or warehousing operation, the most common working concept is “person-to-goods” order picking, which means that order pickers move to storage locations, often pushing or pulling carts and reading orders off paper. These pickers spend significant amounts of time (up to 60%) walking between storage, so reducing that time-spend is an excellent idea.
Automated solutions (automated storage and retrieval, robotic picking systems, etc.) and manual systems (carton and gravity flow systems, pallet flow systems, etc.) can help to make accuracy and productivity improvements in these cases.
But a good ergonomics program will also help facilities design workstations so that everything is within reach of the operator (to the extent possible). Oftentimes, ergonomic solutions are the result of implementing the automated or manual systems listed above. Carton and gravity flow systems, for instance, install easily into existing pallet racks, helping to create ergonomic workstations ideal for picking, assembly, or lineside storage.
Improved Space Utilization
Ergonomics may not have been a prime plant design consideration in the past, but today’s consumer-driven marketplace demands that distribution facilities operate as efficiently and productively as possible.
Proper space utilization is of particular importance during the holiday season, the busiest time of year for retailers. As stated in a previous UNEX blog post, “distribution operations must be in high-performance mode and ready to handle peak volumes.”
By understanding the way that shelves and space are being utilized, UNEX notes, facilities can determine how best to maximize warehouse efficiency: “The placement of shelves and containers, along with the traffic patterns and total design of the building, ultimately affects the ability for [facilities] to utilize any space available.”
Beyond product storage, an in-depth look at space utilization can also help warehouses design the workstation most efficiently for workers. The idea is to minimize reach, reduce twisting, and avoid long periods of standing in one position so that workers won’t need to take steps to reach product or materials.
Learn how to save space in your facility. Download The Guide To Optimizing Warehouse Space Utilization!
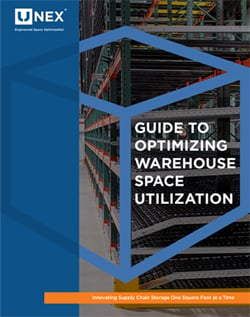
UNEX Solutions to Enhance Ergonomics and Productivity in Distribution Centers
In material handling and distribution, improving productivity doesn’t have to mean pushing workers to work harder. Instead, focusing on ergonomics—designing tasks and workstations to fit the worker—can enhance productivity while reducing physical strain and injury risk. UNEX offers a range of solutions that address key ergonomic challenges in distribution centers, helping to decrease injury risks, reduce travel time, and optimize space utilization.
SpanTrack Lane
Implementing SpanTrack carton flow systems helps reduce the need for workers to reach, bend, or lift in awkward ways, as products flow directly to the pick face. The ergonomic design of SpanTrack places items within easy reach, promoting safer picking practices and reducing the risk of back injuries, strains, and other MSDs.
SpanTrack Lane has full-width roller lanes that provide smooth SKU flow, which reduces picker fatigue and repetitive stress. By keeping products accessible and ensuring efficient flow, SpanTrack minimizes the need for excessive movement and awkward postures, helping to create safer work environments while boosting productivity.
SpeedCell
Reducing the amount of time workers spend walking between storage locations is critical for increasing productivity. SpeedCell, a high-density dynamic storage solution, compresses up to 200 feet of shelving into just 40 feet of organized space, significantly cutting down travel time. By increasing pick facings and storing more SKUs in a compact footprint, SpeedCell keeps products closer to pickers, minimizing walking distance and enhancing picking efficiency.
This solution not only improves throughput but also reduces the physical toll on workers, allowing them to access products more quickly without the need for extensive walking or bending.
Pick Shelves
To further enhance ergonomic design in workstations, pick shelves offer an adjustable and angled shelving system that keeps SKUs within easy reach. These shelves are ideal for piece-picking operations where workers need to retrieve items frequently. By angling the shelves, pick shelves reduce the need for bending or stretching, allowing workers to maintain neutral postures and reducing fatigue over long shifts.
Tilted pick shelves can be customized to meet the specific needs of your operation, ensuring that products are always accessible and within the ergonomic "safe zone" for employees. This increases not only productivity but also employee satisfaction by making tasks physically easier.
Pallet Track
Pallet Track is another ergonomic solution that reduces the need for double handling of high-throughput SKUs. It allows workers to pick directly from pallets, eliminating the need to move heavy items multiple times. Pallet Track also promotes First In, First Out (FIFO) stock rotation, ensuring that the most accessible items are always ready to be picked. By keeping frequently ordered products within easy reach, Pallet Track reduces unnecessary strain and supports a more efficient, ergonomic picking process.
Maximize Warehouse Productivity by Prioritizing Ergonomics
In the distribution center, ergonomics isn’t just a good idea for worker health and longevity: It’s also critical to driving productivity in the warehouse. As noted above, a good ergonomics program can decrease the risk of injury, reduce travel time for workers, and optimize space – driving significant improvements to the bottom line and a more efficient operation overall.
How does your company view the relationship between ergonomics & productivity? For expert assistance in implementing ergonomic solutions and boosting efficiency, contact UNEX today. Our team can provide tailored strategies to enhance your warehouse operations.