How to Design a Carton Flow System Based on Storage Requirements
No one knows your warehouse operation better than you. If you've identified a need for carton flow in your order picking process, you may want to take control of designing and implementing it yourself. A well-planned carton flow system can streamline picking, optimize space utilization, and reduce labor inefficiencies, but achieving these benefits requires a clear understanding of your inventory and operational needs.
Before selecting a racking system, you must analyze key inventory characteristics, including SKU dimensions, quantity, and throughput velocity. Knowing how products move through your facility will help you determine the right number of pick facings, the most efficient rack configuration, and the best storage medium to maximize productivity.
Design a Carton Flow System Tailored to Your Warehouse Needs
In order to create a highly effective carton flow system, you need to understand the big picture that is your inventory. Your SKUs’ physical dimensions and throughput play a major role in building a solution that keeps your inventory optimized. Here are four steps you can take to create an efficient carton flow system based on your storage requirements.
1. Understand your inventory characteristics.
To design the best carton flow solution for you, you need a complete understanding of how many pick locations (or facings) your inventory requires. Your storage needs for each of your SKUs can be entirely different - you may carry 100 of Product A and 1,000 of Product B - and the number of pick locations needed to efficiently store and pick a SKU can vary widely.
Conducting a profiling of your inventory, or a slotting analysis, is one of the most effective ways to determine how many storage locations you require. There are three main characteristics you’ll need to identify to design an appropriate carton flow solution:
- Picking methods: First, you want to identify the types of picks you need to accommodate in your carton flow system. While your primary focus will be on split case, otherwise known as each picking, and/or full case picks, analyzing your full and partial pallet picks will help you determine if you need to integrate pallet picks above or below your carton flow system. Picking methods can affect how many facings you need as well.
- Quantity: Your most popular products will demand more space in a carton flow system and more pick facings to store the quantity needed. If your storage needs change with the seasons, identify your needed quantities at both the highs and lows of their demand. Combining this information with your box dimensions will help determine storage medium and storage medium dimensions.
- Physical dimensions: The length, width, height, and weight of your SKUs will play a major role in determining the depth of the carton flow system and the elevations needed to store your product. Be sure to document these details for every SKU.
Once you have a clear picture of the characteristics of your inventory and how orders will be picked, you’ll need to determine the throughput of your SKUs.
2. Understand your inventory's throughput.
Now that you have your quantity, dimensions, and picking methods plotted out, your next step is to understand the velocity of products moving through your facility. At a high level, you need to identify slow, medium, and fast-moving products, and whether or not your SKU velocities change seasonally.
Throughput is the rate at which SKUs are processed through a facility. You may calculate these numbers by the hour, shift, day, or whatever best fits your particular business. To calculate your throughput for a SKU, multiply the volume of the product (length x width x depth) by the number of times it is picked in a given time interval. Throughput can also vary greatly by product and by season - for example, cases of string lights may fly off the shelves during the fall and winter and dwindle in spring and summer. Failing to account for the seasonality of your inventory can result in designing an ineffective carton flow system.
Effectively analyzing your throughput data in this step and combining it with the physical attributes of your inventory you identified in step 1 gives you the information you need to determine the total facings you need for each SKU. This will also inform the dimensions of the rack required to efficiently store your inventory.
3. Identify your racking needs.
With the throughput and dimensional data you’ve collected, you can now determine what type of racking will best meet your needs. Other factors, like existing equipment and picking methods, will also play a part in this step.
To avoid excessive replenishment, which slows down your operation and can increase pick times, you need to ensure that the depth and width of the rack can accommodate enough SKUs so that each pick facing remains stocked throughout a shift (or your preferred measure of time). The data you collected in the previous steps is invaluable here - it will help you determine how many SKUs you can store at a given depth, if you can stack SKUs in a pick location, and where in the rack the SKU should be placed to provide for the most effective pick. This will inform the style and size of rack you need.
However, factors outside this exercise may also play a part in selecting the best rack for your operation. If you have existing pallet racking in your facility, you may want to use it in your carton flow system to stay consistent across your operation and to reuse beams and uprights you already have. SpanTrack Lane and SpanTrack Wheel Bed carton flow tracks easily drop into existing pallet rack so you can utilize the racking you already have in your facility. If you don’t need to store pallets above your picking locations or are constrained vertically in your facility, you may opt for a standalone carton flow rack solution like Roller Rack instead of pallet rack. Additionally, if you intend to use forklifts or order pickers in your picking process, you’ll need to choose a racking system that best compliments your equipment.
With these three pieces of information, you are ready to design your own carton flow system.
Learn how to Design Your Own Carton Flow Solution! Download our step-by-step guide to designing carton flow systems.
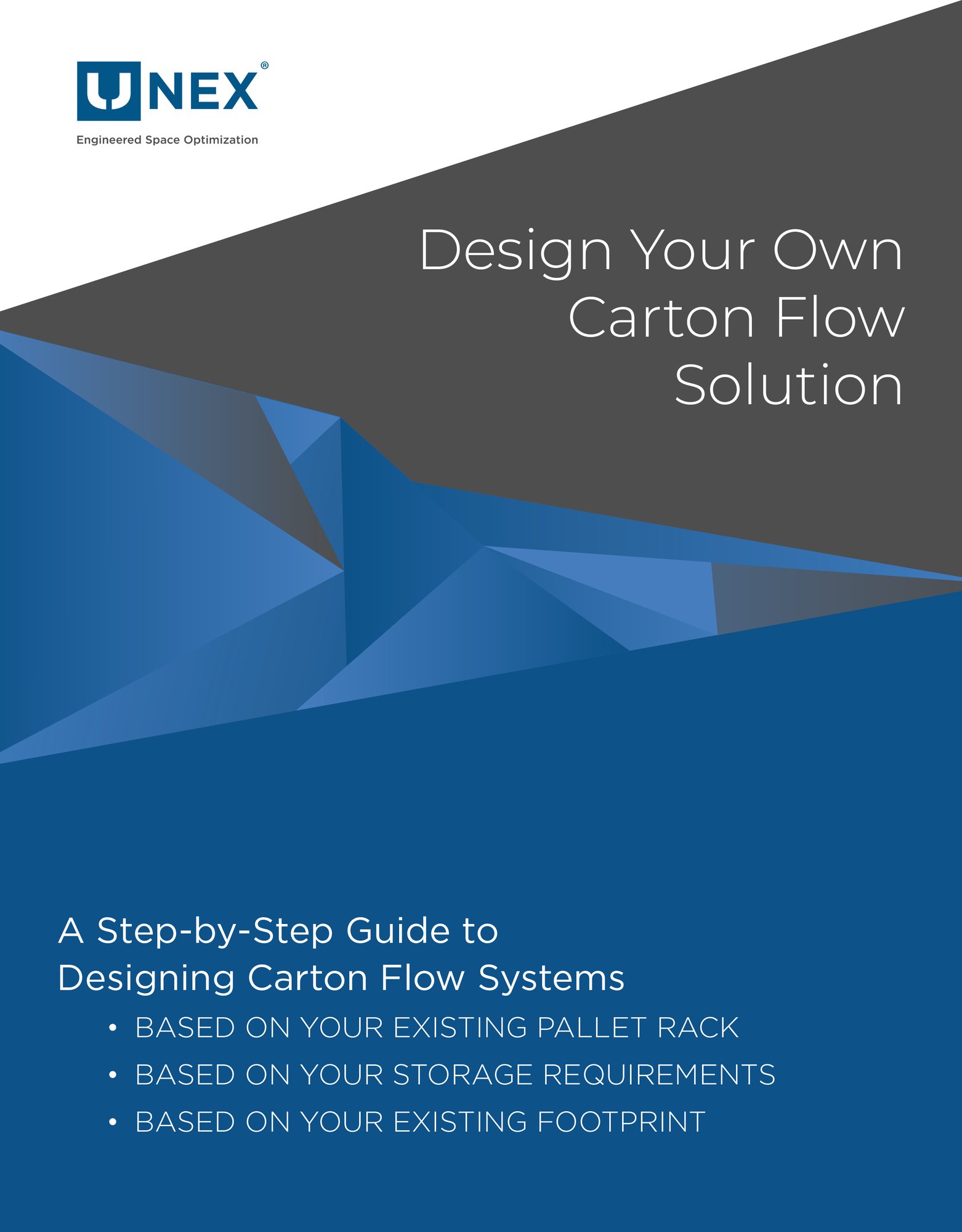
4. Engineer your rack and tracks.
Now it’s time to design - using your product dimensions, volumetric throughput, and rack requirements, you can configure your order picking operation to meet your specific needs.
Whether you identified a need for pallet racking or flow racks, UNEX has developed free and easy-to-use tools to design your solution yourself. To design a carton flow system for your existing pallet rack, using our SpanTrack configurator will help you plot out the amount of carton flow lanes or beds you need, the weight capacities you need at each facing, the heights of each level of storage, and the style of track best suited for your picking methods for each bay of carton flow.
If your inventory is much better suited for a rack + track solution, our Roller Rack flow rack builder will help you quickly and easily input your required dimensions and levels, pick methods, and track styles to create a solution that meets your needs. These carton flow rack systems can also be customized to meet your required weight capacities and can be used as standalone or connected bays to provide the necessary amount of pick facings per SKU.
DIY Carton Flow Checklist
- Document the characteristics of your inventory, including:
- Picking methods required for each SKU.
- Quantity of each SKU.
- Length, width, height, and weight of each SKU.
- Calculate the throughput of each SKU over a designated time interval.
- Use your dimensions and throughput data to identify the type of rack needed and the rack dimensions required to house your inventory.
- Include any existing constraints, like types of equipment being used or types of storage rack being used in other parts of your facility.
- Design carton flow lanes or beds to fit within your selected rack type, or design a rack and track combination.
Choosing the Right SpanTrack Solution for Your Carton Flow System
Once you’ve assessed your inventory characteristics and throughput needs, selecting the right carton flow solution is essential to optimizing your warehouse efficiency. SpanTrack Lane and SpanTrack Wheel Bed are two engineered-to-order solutions designed to seamlessly integrate into existing pallet rack systems, providing superior product flow, accessibility, and storage density.
SpanTrack Lane
SpanTrack Lane is a full-width roller carton flow track, offering continuous contact with stored cartons to ensure smooth movement and prevent hang-ups. This solution is ideal for consistent, high-volume picking environments, where keeping SKUs secure, stable, and within easy reach is critical.
Key Features of SpanTrack Lane:
- Full-width rollers provide complete product support, preventing cartons from getting stuck or misaligned.
- Built for durability, handling heavy and high-volume inventory with ease.
- Drop-in design for quick installation, making it easy to retrofit into existing pallet racks.
- Improves first-in, first-out (FIFO) inventory rotation, reducing product obsolescence and mis-picks.
SpanTrack Wheel Bed
SpanTrack Wheel Bed offers maximum flexibility, allowing left-to-right slotting adjustments to accommodate varying carton sizes. Unlike full-width rollers, wheel beds provide greater adaptability, making them a perfect choice for warehouses with a wide range of SKUs and shifting product dimensions.
Key Features of SpanTrack Wheel Bed:
- Independent wheel tracks enable dynamic slotting, allowing for SKU reconfiguration on demand.
- Optimized for mixed SKU storage, perfect for facilities with frequent product turnover or seasonal inventory shifts.
- Hex hub wheel design ensures smooth carton movement, reducing labor strain and increasing pick speed.
- Modular drop-in installation means quick integration into existing rack structures without the need for extensive modifications.
Maximize Efficiency with the Right Carton Flow Solution
By choosing SpanTrack Lane or SpanTrack Wheel Bed, warehouses can maximize storage space, improve order fulfillment speed, and create a more ergonomic picking environment. Designing a carton flow system based on your storage needs will ensure your facility is not overwhelmed by inefficiently stored products and SKUs are always available at the point of pick.
If you need help navigating your DIY carton flow project, the UNEX team is available to help you understand your inventory data and make informed decisions that result in a highly optimized carton flow system. Contact us and we will guide you through the process.