How to Manage Excess Inventory in Your Warehouse
Fluctuating consumer demand and unpredictable market conditions have created major inventory management challenges for many retailers and warehouses. Many businesses, eager to avoid supply shortages, overstocked their warehouses, only to find that consumer spending had shifted, leaving them with excess inventory and limited storage space.
Without the right inventory management and space optimization strategies, businesses risk higher storage costs, slower fulfillment times, and reduced operational efficiency.
Cost Savings Hiding in Plain Sight
Excess inventory in your warehouse is a very expensive problem. According to a Modern Retail article from June 2022, due to its excess inventory, Target’s operating income dropped 43% year-over-year in the first quarter of 2022. Target also slashed its expectations for operating margin rate from 5.3% to about 2%. Facing a similar excess inventory issue, Walmart’s operating income decreased by $1.6 billion in the first quarter of 2022.
In response to their overflowing warehouses, Target and other retailers were offering heavy discounts to offload inventory. In the tight spot they're in, this makes sense. But it’s also just a short-term solution to the new, unpredictable world we’re living in. The long-term solution is a holistic rethink of the way retailers and other fulfillment operations utilize their warehouse space. Because an overflowing warehouse isn't always as simple as having too much “stuff.”
The problem of too much stuff is created, or at the very least compounded, by suboptimal warehouse space utilization. Fortunately, optimizing your warehouse space isn’t just a band-aid. And with a trained eye, the signs that suboptimal space utilization is affecting your operation are easy to spot.
Finding Space in Your Warehouse
In warehouses that are not fully optimized or experiencing storage challenges, you only need to look up to find lots of unused vertical space. Our research shows that reclaiming overhead space alone allows you to recover up to 85% of unused space.
You can also find unused space hiding in plain sight with a close look at your warehouse’s storage racks. For instance, if a rack is slotted to hold 4x4 boxes but its largest containers are only 3x3, this is a poor use of space. As small as this example may sound, fixing that type of discrepancy can make a dramatic difference in space efficiency.
Less easy to spot, but equally damaging are:
- Lack of, or ineffective policies governing SKU storage, which leads to inefficient storage.
- Haphazard pick and pack processes that decrease throughput.
- Inflexible storage solutions that can’t adjust to increasing SKU variety or changing SKU velocity.
- Lack of balance between reducing pick time and increasing storage density.
Finding and fixing these issues alleviates the multi-faceted challenges presented by inventory overflow because they enable you to store more in your existing space, increase throughput, and adjust storage as your needs change.
Learn how to save space in your facility. Download The Guide To Optimizing Warehouse Space Utilization!
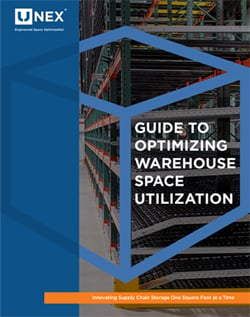
4 Things You Can Do Right Now to Maximize Warehouse Space Efficiency
Warehouse space is a valuable resource, and inefficiencies in storage can lead to higher costs, slower fulfillment, and wasted space. Whether you're dealing with inventory overflow, poor slotting, or rigid storage systems, optimizing your available space is key to improving productivity and throughput.
By making small but strategic adjustments warehouses can increase efficiency without expanding their footprint. Here are four actionable steps you can take right now to make the most of your warehouse space.
1. Reclaim vertical space
In some warehouses, narrowly spaced, high storage racks paired with vertical picking machines can help maximize space utilization (and pick efficiency). In other warehouses, unused vertical space can be found by adjusting beam levels on your racks and/or rearranging SKUs by height. The point is, vertical space is often hiding in plain sight, just waiting for you to reclaim it.
2. Follow putaway rules
Strict enforcement of putaway rules maximizes picking productivity and improves throughput by ensuring SKUs make it to the ideal storage location. Your warehouse management system should direct putaway rules; if it doesn’t, create or adopt a system that does. And make sure those rules are followed.
3. Adopt re-configurable storage
A big part of the problem with excess inventory is that retailers have too much of one thing and not enough of another. A more flexible, configurable warehouse storage system creates a margin for these kinds of SKU snafus. So consider implementing systems like universal carton flow beds that allow for flexible reslotting. This way, when demand changes, you can remain agile and adjust your SKU slotting accordingly.
4. Choose storage mediums based on SKU velocity
The faster a SKU moves in and out of your warehouse the better. There are certain storage mediums that are suited for slow, medium, and fast-moving SKUs. Determining which storage mediums you require for your unique product mix ensures slow-moving SKUs aren’t taking up the easily accessible space that should be reserved for fast-moving SKUs. It also ensures fast-moving SKUs aren’t packed too densely to be picked efficiently.
UNEX Solutions that Can Help Combat Inventory Woes
There’s no one-size-fits-all recipe you can follow to reclaim unused space in your warehouse. But, as you may have gathered, there are universal principles. And in the face of unpredictability, it’s these principles—balancing SKU speed and accessibility, proper slotting, choosing configurable solutions, etc.—that will see you through.
Of course, it doesn’t hurt to have a few tools of the space utilization trade in your belt. Carton flow beds and reconfigurable flow racks, for example, are two space-saving storage solutions you may consider to stay flexible as inventory levels change.
SpanTrack Wheel Bed
Flexible carton flow beds that drop into existing structures to create flow rack systems for full and split case picking operations. This solution helps you adopt configurable storage because it can be added to any new or existing pallet and filled with products of various sizes and weights. SpanTrack Wheel Bed allows you to flood entire levels of pallet rack with carton flow storage, giving you maximum flexibility left-to-right for reslotting.
FlowCell Modular Flow Racks
Storage units and workstations that can be configured to your facility’s unique operation. FlowCell is very versatile in that it can be easily reconfigured as your needs change. Utilize FlowCell for extra SKU storage at the ends of aisles, or in areas of your facility where overhead clearance is an issue. When your needs change, you can reconfigure FlowCell to work in many other areas of your facility like staging, packing, shipping, and more.
Maximize Warehouse Storage and Efficiency with UNEX
No matter your inventory woes, UNEX offers a full range of engineered-to-order solutions that help optimize workflows and maximize storage for a variety of businesses. If you have questions or want to learn more about increasing storage capacity and efficiency in your warehouse, contact us today.