Cutting Travel Time in Warehouses: How UNEX Solutions Boost Efficiency
Statistics show order pickers spend about 60 percent of their time walking product or moving product around. As picking operations are very labor intensive, anything you can do to speed the process will help lower the cost of fulfilling orders. However, in the omnichannel world, customers place more orders with fewer items, which can lead to a picking nightmare, especially if you strive to reduce labor costs.
As demand for faster fulfillment and higher order accuracy continues to grow, warehouses face increasing pressure to do more with limited space and labor resources. Inefficient picking processes not only slow down operations but also drive up costs, increase worker fatigue, and create bottlenecks that impact overall productivity. To remain competitive, businesses must find smarter ways to store, pick, and move products efficiently—without adding unnecessary steps or strain to their workforce.
The Impact of an Unorganized Warehouse
In large distribution centers, pickers often walk 8 to 15 miles per day, increasing fatigue and slowing productivity. Hard concrete floors and frequent bending and reaching add strain to joints and muscles, making it essential to streamline workflows and reduce unnecessary movement.
Long walking distances take a toll on workers, leading to slower pick rates, increased exhaustion, and higher risk of errors. Over time, this physical strain contributes to worker burnout, absenteeism, and even injuries, which further disrupt warehouse efficiency. Poorly organized storage layouts force pickers to constantly bend, stretch, and lift, adding to physical fatigue and making every order more labor-intensive than necessary.
Additionally, inefficient warehouse layouts create bottlenecks and congestion, slowing down operations even further. When high-velocity items are stored too far from picking stations, workers spend more time navigating the warehouse instead of fulfilling orders. These inefficiencies drive up labor costs, decrease order accuracy, and reduce overall throughput, making it harder for businesses to keep up with demand.
Practices that Reduce Travel Time
Managers look at how to optimize the way that products are stored as a way to reduce travel times and stress on employees. Travel time can be reduced by reducing the time to search to locate items. Creating a slotting system that makes products easy to locate should always be the first step in solving the issue of travel time. Knowing where a product is located and storing SKUs with similar throughput velocities near each other ensures that order pickers spend more time picking and less time traveling to the next pick.
Another method to reduce travel time we've discussed here often is consolidating storage space. Maximizing the storage density of products allows managers to reduce the footprint of their storage systems. This means less walking for order pickers as they pick and prepare orders for packaging.
Ultimately, all this great travel time reduction is pointless if these order pickers need to physically carry completed orders to packing stations to prepare for shipment. A combination of powered and gravity conveyor can solve this problem. Using a conveyor to move picked products out of pick zones or modules eliminates the need for the picker to walk that order to a packing station.
Learn to optimize warehouse space for increased speed and accuracy. Download the Guide to Understanding Throughput for Fulfillment!
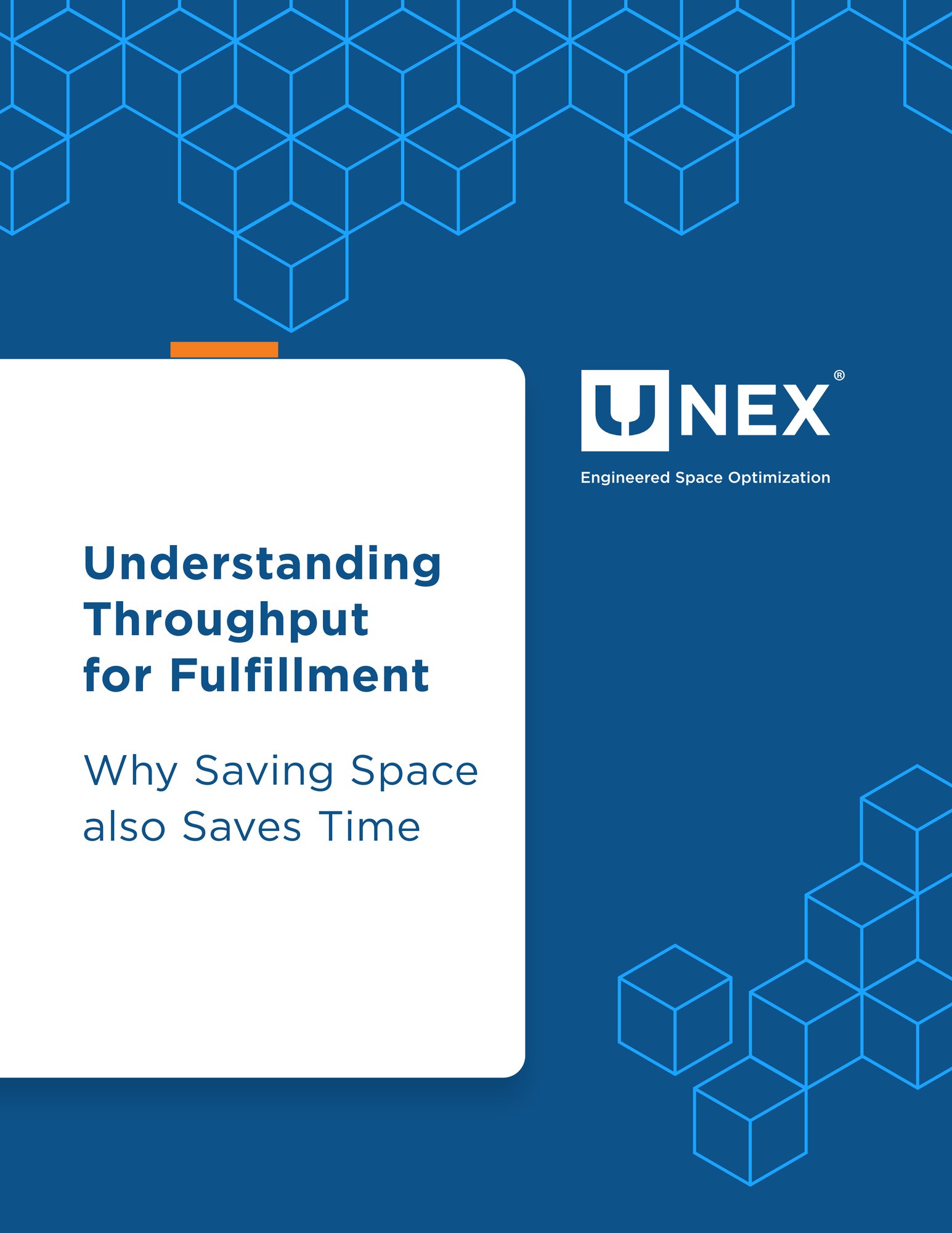
UNEX Solutions to Optimize Picking Efficiency
Reducing travel time and minimizing physical strain on workers requires intelligent storage and material handling solutions. UNEX solutions are designed to maximize warehouse efficiency by strategically organizing SKUs. Grouping similar throughput items together ensures pickers spend more time fulfilling orders and less time traveling.
UNEX offers a suite of high-density, space-saving products designed to streamline order fulfillment, optimize SKU accessibility, and reduce unnecessary movement throughout the warehouse.
SpanTrack Carton Flow
By integrating full-width roller lanes or wheel beds, SpanTrack creates a FIFO (First-In, First-Out) storage system that ensures products are always within reach. This eliminates time wasted searching for inventory and reduces picker travel distances by keeping high-velocity SKUs front and center.
SpeedCell High-Density Storage
SpeedCell condenses 200 feet of shelving into just 40 feet, dramatically reducing the footprint of picking operations. This high-density storage solution allows workers to retrieve products quickly without excessive walking, bending, or stretching.
Gravity Conveyors in Packing Stations
Travel time reduction is meaningless if workers still have to manually transport completed orders to packing stations. By implementing gravity conveyors, picked products can flow seamlessly from pick zones to packing areas, eliminating unnecessary walking and keeping pickers focused on order fulfillment.
Boost Your Warehouse Efficiency with UNEX
By implementing UNEX solutions, warehouses can significantly cut travel time, reduce labor costs, and improve worker ergonomics. If your picking process is slowing you down, UNEX can help you build a faster, more efficient operation.
Contact UNEX today to discuss your warehousing needs and discover the best solutions to optimize your space and streamline your order fulfillment process.