Flexible Solutions for High-Mix, Low-Volume Manufacturing Assembly
Henry Ford famously said, "Any customer can have a car painted any color that he wants so long as it is black." Ford's remark underscored his belief that mass production and fast assembly were necessary to build affordable, dependable cars "for the great multitude." His vision of a simple, scalable platform product with minimal variations allowed him to produce 15 million Model Ts over its 19 model years, which revolutionized the automobile industry.
While Ford's strategy of high-volume, low-mix production has long been the desired model in most types of assembly operations, its opposite – high-mix, low-volume assembly – has increased significantly in the last couple of decades.
Why? Today's consumers want a variety of products and features tailored to their specific needs and preferences: high-mix, low-volume. In high-mix, low-volume manufacturing, production volume decreases inversely and accordingly to meet the demand for higher production variety.
Learn lean manufacturing storage principles. Download the Lean Manufacturing Storage Guidebook!
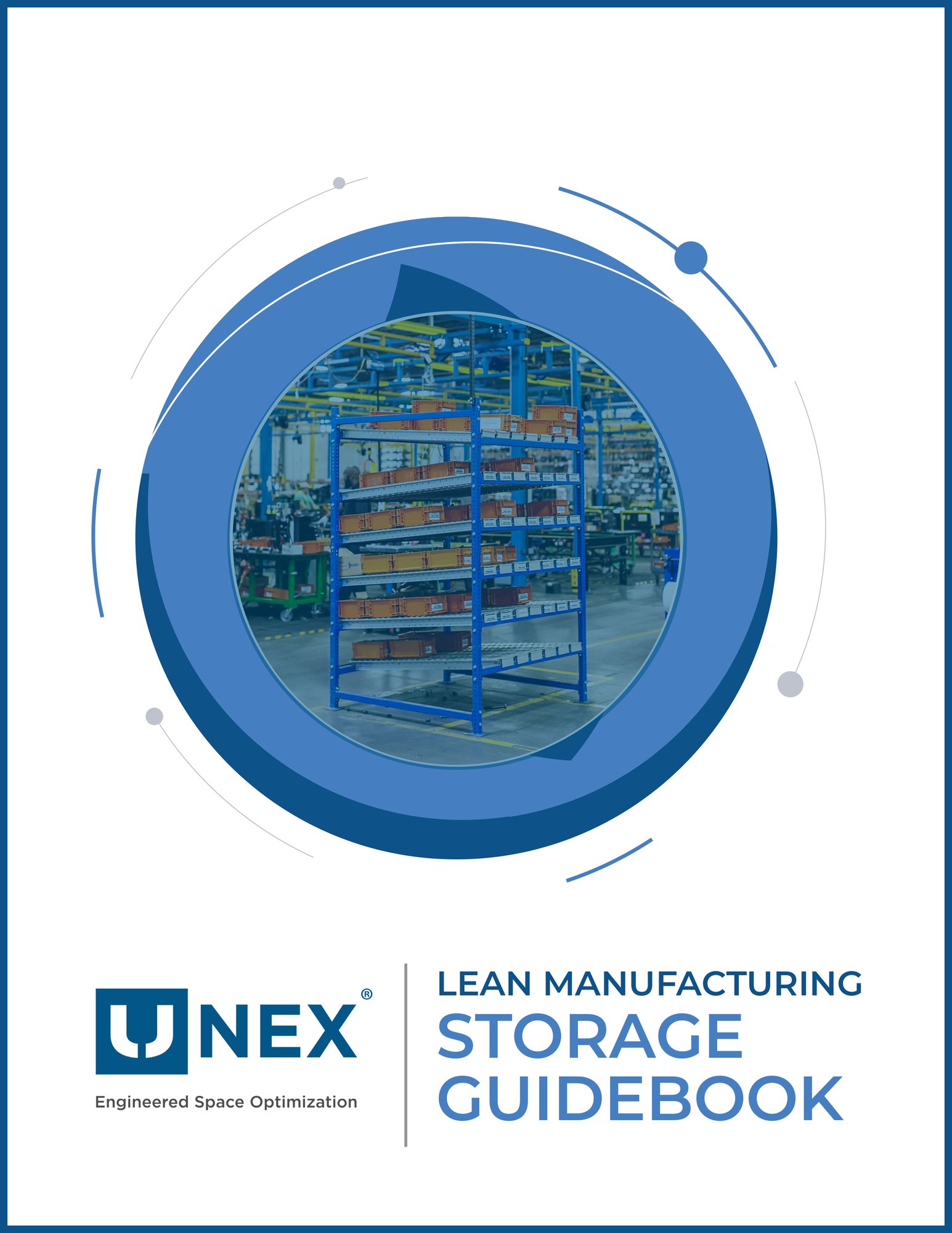
Benefits of High-Mix, Low-Volume Assembly
There's no reason that flipping the assembly model should turn production costs and speeds topsy-turvy. While the specifics of sourcing, setup, testing, production, packaging, and shipping may need to be adjusted, moving to high-mix, low-volume assembly can offer many advantages, including:
- Faster reaction times to fluctuations in component costs and availability
- Reduced inventory requirements
- Improved responsiveness to consumer trends and market demands
- Better customer service and satisfaction
- Greater flexibility in the use of working capital
To improve operations in high-mix, low-volume organizations apply Lean principles and practices to assembly operations, dynamic environments call for progressive solutions. Implementing the Lean methodology will minimize waste and optimize material, people, and process flow, which are vital to achieving output quality and operational efficiency.
Flexible Solutions for High-Mix, Low-Volume Environments
High-mix, low-volume assemblies require flexible, innovative racks, shelving systems, workstations, and other organizational solutions. These solutions improve space utilization, eliminate clutter, reduce travel and search time, protect worker safety, improve ergonomics, and speed picking, rotation, and replenishment. That's the only way to balance greater product variety with smaller production volume – and still turn a profit.
Introducing FlowCell by UNEX
UNEX FlowCell organizes Lean assembly environments. Our workstations neatly store tools and parts in the appropriate order to eliminate wasted time looking for parts or locating tools. UNEX FlowCell Lean workstations integrate industry-leading carton flow solutions with galvanized steel workbenches and overhead toolbars to hold all of the equipment needed for tasks – keeping parts and products easily within reach without stretching, bending, or other risky body movements.
Benefits of FlowCell:
- Maximized Space Utilization: FlowCell increases space utilization by up to 50% by keeping inventory organized and properly stored. This boosts production efficiency by up to 30% by angling parts toward the worker, creating an efficient and accessible pick point.
- Improved Ergonomics: FlowCell minimizes reaching and improves ergonomics, reducing worker injury and fatigue.
- Enhanced FIFO Inventory Rotation: FlowCell replenishes from the back so it doesn’t interfere with the picking process in the front, ensuring a smooth flow of materials.
Applications of FlowCell in High-Mix, Low-Volume Assembly
FlowCell's modular design makes it ideal for various applications in high-mix, low-volume environments:
- Lineside Storage: Keep essential parts and tools within arm's reach of assembly workers, improving efficiency and reducing downtime.
- Sub-Assembly Stations: Streamline sub-assembly processes with well-organized workstations that adapt to changing production needs.
- Supermarket Storage Areas: Efficiently store and retrieve components in high-density configurations to support Lean manufacturing principles.
Optimize Your Assembly Operations with UNEX
UNEX specializes in engineered space-saving solutions for lean manufacturing environments. We serve several industries, including distribution, logistics, retail, and manufacturing. Learn more about how UNEX can help minimize waste, improve ergonomics, and optimize storage space within your operation by contacting us today!