How U-Shaped Assembly Cells Can Improve Efficiency
Henry Ford revolutionized manufacturing with his invention of the assembly line. Before 1913, Ford and virtually every other automaker assembled whole cars at a station with a team of workers working together to complete a single example, usually from start to finish.
Ford had been trying to increase his factories’ productivity for making the Model T to meet his ideal of building his “motor car for the great multitude.” The first Model T cost $850, which is $21,000 in today’s dollars. But, he felt this wasn’t cheap enough for the masses and looked for ways to decrease the cost while pumping up production rates.
Ford broke the Model T assembly into 84 discrete steps and trained workers to do just one of the steps. He also built machines that would stamp out automobile parts automatically, and much quicker than humans could. For his assembly line, Ford installed moving lines to handle various parts. In December 1913, he unveiled the moving chassis assembly line. Several months later, a mechanized belt that traveled at six feet per minute was added, allowing Ford to produce more and more cars, much faster. The assembly line cut the amount of time it took to assemble a Model T from 12.5 hours to just 93 minutes.
Not only did Ford realize a 90 percent productivity gain with his assembly line implementation, but he also saved a considerable amount of money on operating costs. Ford doubled wages to $5/hour and cut working hours from ten to eight hours a day. By drastically reducing the cost of production with standardized parts and more efficient assembly, Ford was able to bring the cost of the automobile low enough for everyone to purchase at $260.
Today’s automotive manufacturing lines have changed significantly with the addition of robots, interchangeable parts, and hydraulic lifts. The Ford assembly plant that assembled the first Model T in Michigan went from 100 cars per day in 1913 to 1000 vehicles per day a year later. Today the same assembly plant builds over 600 Ford Focus and C-Max sedans in each of two 10-hour shifts using just 500 people. The current line’s flexibility allows for building five different models with a range of colors and features. One hundred and twelve years after Ford’s first moving assembly line launched, the company now makes 16 Ford vehicles every minute.
The Assembly Line of Today – U-Shaped Assembly Cells
Automobiles are no longer made from start to finish in the same place. Parts are created all around the world and then assembled in multiple facilities until the final car is pieced together at still another location.
Take, for example, the Adient LLC’s facility in Georgia, which assembles seats, door panels, and other interior parts for several automobiles. The high-volume facility completes 55 jobs an hour so that every minute counts in the assembly, and every inch of workspace is essential.
Automotive assembly plants have found that U-shaped cells work best in the plants for saving space and because there are so many intricate subassembly processes included in the assembly of a vehicle. For example, putting together an engine block or dashboard in one of these cells allows a highly specified process to take place that doesn’t crowd and eat up space on the main assembly line.
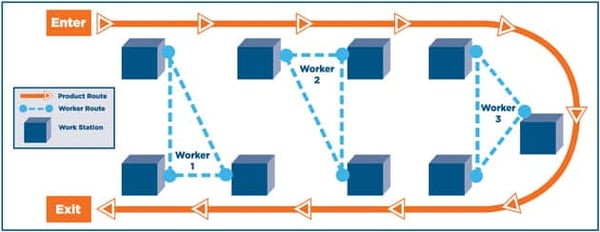
Implementing one-piece flow with U-shaped assembly cells is a great way to save space in most manufacturing environments with moderate amounts of variability in production size and product mix. One-piece flow will have a tremendous impact on manufacturing lead times, production delays, inventory levels, and warehousing space requirements.
Some of the key concepts to understand when transitioning to a manufacturing cell are:
- One-piece flow,
- Line balancing,
- Right-sizing,
- Ergonomics, and
- Quality control.
One-piece flow, the opposite of batch processing, is the movement of a single product through the manufacturing process. One-piece flow redirects the workforce away from non-value added activities, such as having to search for parts and focuses on the manufacturing process. With batch processing, large amounts of wastes exist in waiting, transporting, and storage of inventory. Workers maximize their output at the expense of downstream processes and increased work in process.
Work in progress (WIP) drastically reduces in one-piece flow, which minimizes exposure to defects in the manufacturing process and allows for quicker reaction to fluctuating customer demands. One-piece flow creates a smoother production process, with steady workloads and shorter lead times. The units of work performed in each position must have equivalent cycle times to keep the process seamless. This technique is called “Line Balancing.”
Right-sizing machinery to meet customer demand, instead of minimizing part cost, is essential to the success of cellular manufacturing. Placing smaller and slower equipment in close proximity to other equipment and processes helps eliminate wasted space, walking, inventory build-up while lowering initial cost. Cellular manufacturing is a system to transfer products between stations (i.e. U, J, or L shaped assembly cells), a method to feed parts into the stations (flow racks, bins, or carts), and a means by which to flow finished goods and packaging out of the system.
Learn how UNEX flow racks allowed Adient to adapt quickly to production changes. Download the Case Study.

Setting Up Your U-Shaped Assembly Cells
- Always flow product in the same direction, counterclockwise.
- Cross-train employees to be able to perform all or most functions within the cell to increase responsibility, quality, and traceability.
- Use U-shaped assembly cells when possible to minimize the distance between the beginning and the end of the process.
- Use First In First Out (FIFO) to shorten lead times, reduce errors, and improve order accuracy.
- Workstations should be positioned as close together as possible to eliminate wasted space, but not so close as to hinder maintenance or create discomfort for employees.
- Create a system for flowing sub-parts into the system in an optimal manner, considering ergonomic principles.
- Keep the path of flow within the cell clear and unhindered.
The benefits of implementing cellular manufacturing in the appropriate environments can have a positive impact on a business. Reconfiguring machinery into assembly cells reduces material handling and warehouse footprint. When properly executed, a company will simultaneously shorten their lead times and dramatically reduce work in process inventory. Having a cross-trained workforce gives a factory increased flexibility to meet variations in demand and a better understanding of a quality product.
Lineside Storage and FIFO
Manufacturing has come a very long way since Henry Ford’s Model T came in black, black or black. Today, there are dozens of different options for nearly every product imaginable, which is outstanding for consumers but can provide logistical challenges in assembly. Because there are so many different options, stock rotation is paramount in most operations in the automotive assembly plant. FIFO is a natural fit for assembly processes that require natural stock rotation because it is backloaded, and there is a logical order. The first product loaded is also the first product picked. If you’ve analyzed your throughput, stocking with FIFO becomes a smooth and hassle-free storage method.
Lineside storage is something that has been complicated by the deluge of choices that consumers have today. During the early Ford years, it was easy to keep pallets of black door panels along the line, because there was no variety. However, when there are 40 different colors available (do you want your door black, midnight, or gunmetal black?), storage becomes much more difficult. To keep palletized storage within reach, the assembly line must be extended to accommodate this additional space. Additional physical space to extend the line means more equipment and more pickers. Replacing those pallets with a lineside flow rack system is much more efficient. Flow racks, like FlowCell, are used for just-in-time storage where assemblers are each picking items for assembly.
At Adient LLC's plant, lineside assembly racks are used to hold parts such as door handles, airbags, and brackets/buttons. As a just-in-time operation, the plant needs to keep things moving without interruption. Lineside FlowCells can easily be configured to handle a variety of parts, keeping productivity high. These racks have greatly improved the efficiency of the assembly process.
Final Words
Maintaining a consistent flow of materials lineside requires a balance of the right parts placed at the right locations so they can easily and quickly be picked and placed within the assembly cells. Combining flow and assembly cell techniques is becoming quite a popular approach in automotive manufacturing, providing great flexibility, and fostering a reduction in time and workspace requirements. What would Henry Ford say now if he saw a modern assembly plant with employees working on bits and pieces instead of the entire automobile? He’d probably like it.
UNEX specializes in engineered smart space-saving solutions for Assembly Operations, serving several industries, including distribution, logistics, retail, and manufacturing. Learn more about how UNEX can help keep productivity high, improve ergonomics, and maximize storage space within your operation, click here to contact us.