Implementing FIFO for Lineside Storage
Since Henry Ford’s Model T came in black, black, or black, manufacturing has come a long way. Today, there are dozens of options for nearly every product imaginable, which is outstanding for consumers but can provide logistical challenges in assembly. Because there are so many different options, stock rotation is paramount in most operations. FIFO is a natural fit for assembly processes requiring natural stock rotation because it is back-loaded and has a natural order. The first product loaded is also the first product picked. If you’ve analyzed your throughput, stocking with FIFO becomes an easy and hassle-free storage method.
Lineside storage has been complicated by the deluge of choices that consumers have today. During the Ford years, keeping pallets of black door panels along the line was easy. There was no variety. However, storage becomes much more difficult when there are 40 different colors available (do you want your door black, midnight, or gunmetal black?). The line must be extended to accommodate this additional space to keep the palletized storage. This means additional physical space to extend the line, more equipment, and more pickers. Replacing those pallets with a lineside flow rack system is much more efficient.
The Advantages of Implementing Lineside Storage
As modern manufacturing has evolved to accommodate a wider variety of consumer choices, the complexity of assembly processes has increased significantly. This shift has made lineside storage an essential component of efficient production. By placing materials and components directly at the point of use, lineside storage systems streamline the assembly process, reduce wasted time, and enhance overall productivity.
Improved Efficiency and Reduced Downtime
Lineside storage systems bring parts and materials directly to the assembly line, ensuring that everything needed for production is within easy reach of the workers. This proximity eliminates the need for operators to leave their stations to retrieve parts, thereby reducing downtime and increasing the speed of assembly. With everything organized and accessible, workers can focus on assembling products rather than searching for components, leading to faster throughput and higher productivity.
Optimized Space Utilization
In contrast to traditional storage methods that require large amounts of space to accommodate various components, lineside storage solutions, such as flow racks, make better use of available space. These systems allow for vertical storage and easy access to a wide variety of components, even in a compact footprint. This not only helps in managing the increasing number of product variants but also frees up valuable floor space for other critical operations.
Customization for Specific Needs
Lineside storage systems can be customized to meet the specific needs of different assembly operations. Whether you require layback storage for easy access to larger items or knuckled storage for smaller components, lineside solutions can be tailored to optimize the picking and assembly process. This flexibility ensures that each manufacturing line operates at peak efficiency, regardless of the variety and volume of components involved.
Support for Lean Manufacturing Practices
Implementing lineside storage aligns with lean manufacturing principles, particularly the first two pillars of 5S—Sort and Straighten. By keeping only the necessary items at the line and organizing them in a logical sequence, lineside storage supports a clutter-free, efficient workspace. This organization not only speeds up the assembly process but also reduces the potential for errors and waste, contributing to a leaner, more cost-effective production environment.
Learn lean manufacturing storage principles. Download the Lean Manufacturing Storage Guidebook!
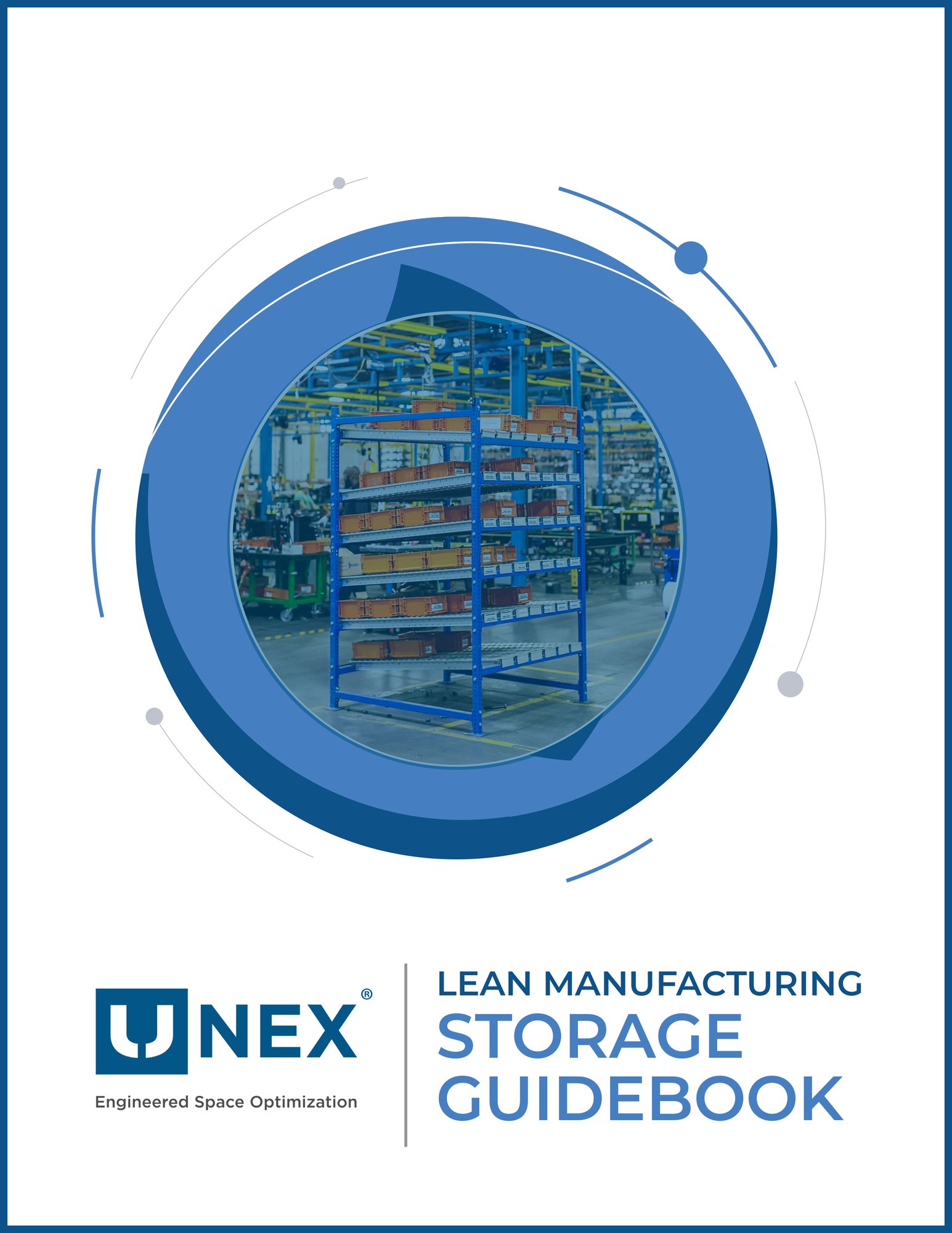
Maximize Efficiency with FIFO Lineside Storage Systems
Lineside storage is particularly beneficial when integrated with FIFO (First-In, First-Out) principles. By using FIFO in a lineside setting, manufacturers ensure that the oldest stock is used first, reducing the risk of obsolete inventory and ensuring that components are used in the correct order. This is especially important in industries where the shelf life of components can impact product quality. Additionally, FIFO lineside storage systems make inventory management more intuitive and reduce the likelihood of errors, contributing to a more streamlined and reliable production process.
Throughput analysis is required to implement a FIFO lineside flow rack system. If you have room for an 8 ft. deep aisle but go through 16 ft. worth of product daily, you will have to refill the shelf each day. Our Space Optimization Specialists can assist you with this throughput analysis. Essentially, this system would be a just-in-time storage system where assemblers are each picking the items. Another consideration is the type of product being stored. Do you want layback storage or knuckled storage? It depends on the product being picked.
When going to a FIFO lineside system, it is important to remember the first two philosophies of 5S:
- Sort
Go through the pick area and dispose of any unnecessary items. This will increase efficiency by removing any potential obstacles present during the pick. You want the picking area to be as simple as possible so that the task can be accomplished with minimal distraction or superfluous activity. - Straighten
Similar to sorting, straightening requires arranging the workspace in a way that makes sense to the assembler. FIFO is part of this straightening process, as the flow rack design puts products in a position to be picked where and when they need to be. The FIFO streamlines the picking process by removing the need to sort through products to find the next pick.
UNEX Solutions for Lineside Storage and FIFO Efficiency
When it comes to optimizing lineside storage and implementing FIFO in your assembly operations, UNEX offers a range of innovative solutions designed to enhance efficiency, improve space utilization, and streamline inventory management.
Flow Racks
UNEX Flow Racks are specifically designed to support lean manufacturing practices by providing easy access to parts and materials in a FIFO sequence. These racks can be positioned directly at the assembly line, allowing workers to pick components with minimal effort. By organizing inventory in this way, Flow Racks help reduce waste, improve ergonomics, and enhance overall productivity. The use of Flow Racks in lineside storage ensures that your production process remains smooth and efficient, even as the variety of SKUs continues to grow.
FlowCell Modular Workstations
For assembly lines requiring customized storage solutions, UNEX FlowCell modular workstations offer a highly adaptable option. FlowCell units are designed to bring parts and tools directly to the point of use, minimizing movement and reducing the time workers spend retrieving items. These workstations can be configured to support FIFO by placing newer inventory behind older stock, ensuring that the oldest parts are used first. The modularity FlowCell also allows for easy reconfiguration as your production needs evolve, making it a versatile solution for maintaining an organized, efficient assembly line.
Elevate Your Assembly Line with UNEX Solutions
The remaining philosophies of 5S, shine, standardize and sustain, are also incredibly important to remember when designing and maintaining a streamlined picking process. A just-in-time FIFO lineside storage system can make your picking process faster and more efficient. Contact a UNEX Space Optimization Specialist today to discuss the potential to add FIFO to your line-side storage.