Implement Lean Manufacturing with Carton Flow Systems
In today's interconnected and highly competitive global economy, businesses are facing unprecedented pressure to reduce production costs in order to remain viable and competitive. This has led to a greater emphasis on adopting strategies that not only cut expenses but also enhance the overall quality of products and deliver superior value to customers.
One such strategy that has gained widespread recognition and implementation is lean manufacturing. Lean manufacturing is a systematic approach aimed at minimizing costs by identifying and eliminating wasteful practices that do not add value to the end product, all while simultaneously ensuring improvements in product quality and customer satisfaction.
7 Key Areas to Reduce Waste in Lean Manufacturing
The roots of lean manufacturing can be traced back to Japan, specifically to the Toyota production line, where the company embarked on a revolutionary journey to create the most efficient production system in the world.
In lean manufacturing, eliminating waste is essential for optimizing efficiency, reducing costs, and maximizing productivity. By focusing on these seven key areas, manufacturers can streamline operations, minimize inefficiencies, and create a more sustainable production process.
1. Transportation. Moving a product or raw material from one place to another takes time, incurs the risk of loss or damage, and does not increase the product’s inherent value. Minimizing transportation saves time and money by making the assembly, parts picking, or production process faster and more efficient.
2. Unnecessary/Excess Inventory. This can be a raw material, work in progress, or finished product that is purchased or produced but is not needed. This represents a waste of not only money but also valuable space and time and can result from inefficient or disorganized storage systems.
3. Unnecessary/Excess Motion of a worker or equipment wastes time and energy, and can even lead to accidents and injuries in the workplace. This waste is high when static storage systems such as pallet racks and wire shelving are used.
4. Waiting is the waste that results when a product is not being produced or transported and represents a significant portion of a product’s shelf life.
5. Overprocessing results when more work is done on a product than is required, or when more complex or unnecessary production processes are employed.
6. Overproduction, or simply the production of more goods than required, increases all other wastes.
7. Defects that require a product to be reworked or even scrapped are a huge waste, and for many manufacturers represent a significant amount of cost.
Learn lean manufacturing storage principles. Download the Lean Manufacturing Storage Guidebook!
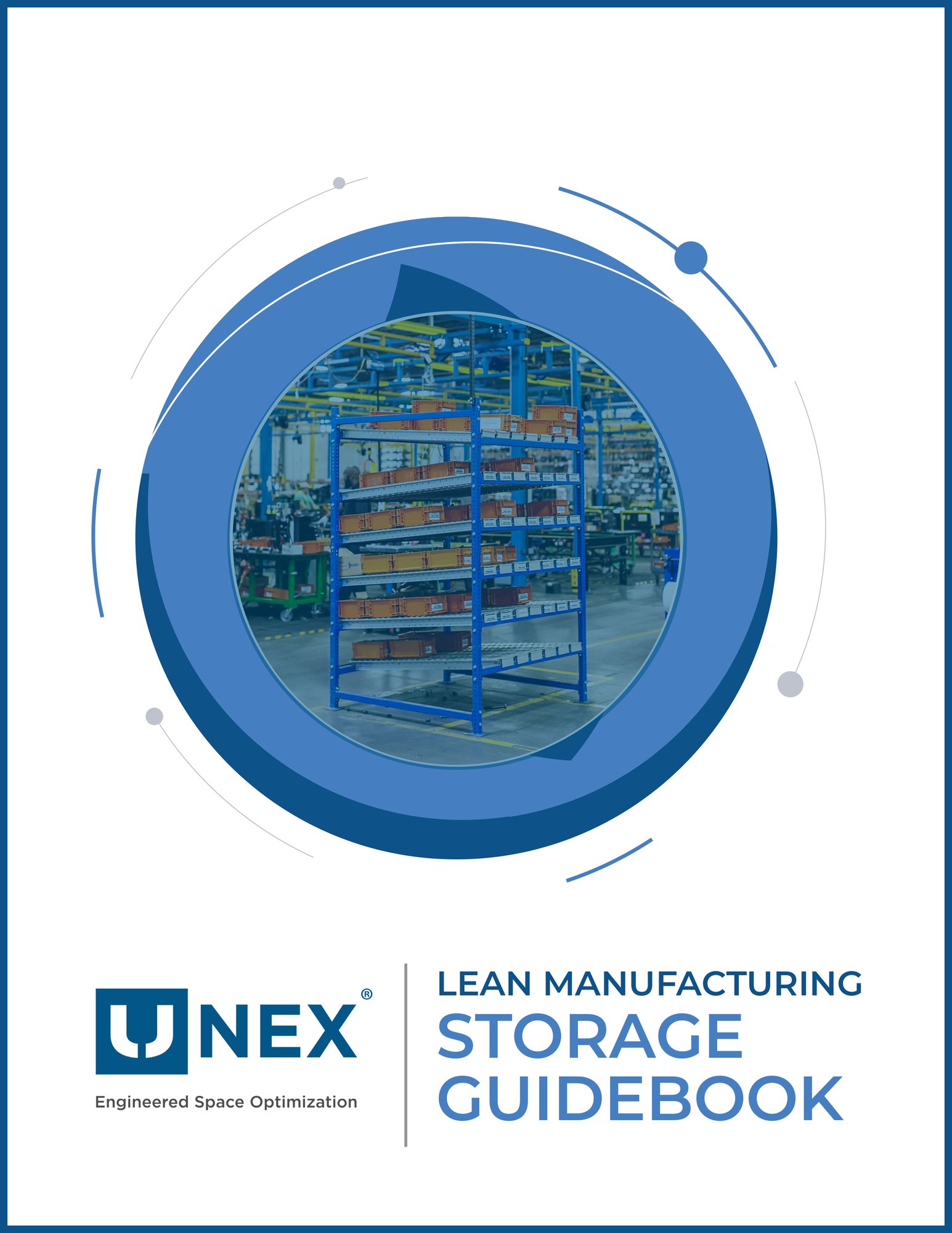
Boost Efficiency with Dynamic Storage Solutions
UNEX carton flow systems offer a low-cost and highly effective means to eliminate these wastes in the workplace while increasing order picking efficiencies and accuracy, improving space utilization, and decreasing labor costs. One key area in which to apply lean manufacturing is the storage mediums used for assembly and parts picking.
Static storage units such as shelving, containers, pallets, and wire decking result in wasted space and poor visibility. As a result pick rates are low, and workers risk injury by searching for products and then climbing, lifting, or overreaching to get them. Dynamic storage offers a safer, more ergonomic solution for assembly and parts picking, and can increase space utilization by up to 50%.
For example, a modular flow rack system minimizes reach distances by ensuring that the product is always upfront and accessible, and therefore always within easy reach. Pick access and accuracy are greatly improved because parts are angled toward the picker. These factors can increase pick rates by up to 30%.
FlowCell Supports Lean Manufacturing Principles
UNEX FlowCell is a modular and dynamic storage system designed to streamline your assembly line operations while promoting lean manufacturing principles. Whether for lineside storage, sub-assembly stations, or supermarket racks, FlowCell workstations optimize space utilization and improve ergonomics, making it easier and safer for your team to access materials.
FlowCell systems are highly adaptable, featuring flexible designs that adjust to your facility’s unique needs. Each unit can be reconfigured to accommodate changes in process flow, ensuring that your storage solutions evolve alongside your business.
Key Benefits of FlowCell:
- Increased Space Utilization: By organizing inventory efficiently, FlowCell boosts space utilization by up to 50%.
- Enhanced Ergonomics: Products are angled towards the picker, reducing reach distances and minimizing worker strain, which can improve productivity by up to 30%.
- Flexible and Durable: Built from heavy-gauge steel, FlowCell is engineered for durability while allowing easy reconfiguration on 1-inch centers, making it a cost-effective, long-term solution.
- First In, First Out (FIFO) Stock Rotation: Maintain a seamless inventory rotation with back-to-front replenishment that never interferes with the picking process.
Optimize Your Flow Rack System with UNEX
Whether you are facing space constraints or looking to improve your assembly line efficiency, FlowCell offers a tailored solution. By optimizing the organization and flow of your materials, you can reduce waste, improve safety, and enhance overall operational efficiency. Contact us today to discover how UNEX can help you achieve your business goals.