Using FlowCell Flow Racks to Solve Common Manufacturing Challenges
Today’s manufacturers are constantly pressed to deliver more and do it faster, all while navigating tighter spaces, rising costs, and increasingly complex product mixes. Every inch of floor space, every second of motion, and every touchpoint matters for meeting demand.
Fortunately, there is a versatile solution for addressing some of the most urgent needs of today’s manufacturers. FlowCell flow racks are engineered to support lean manufacturing practices by streamlining storage, improving material flow, and reducing waste across the production floor. FlowCell can be configured for a variety of applications, including but not limited to:
- Lineside Storage Racks
- Picking Carts
- WIP Carts
- Industrial Workstations
- Manufacturing Supermarkets
Implementing smart, flexible storage can transform nearly any manufacturing workflow. From inflexible layouts to poor parts presentation, we’ll explore some of the most common pain points facing manufacturing teams today and demonstrate how FlowCell flow racks help solve them.
Challenge #1: Disorganized Workstations and Excessive Downtime
Without a clear, organized workflow, many industrial workstations tend toward chaos. Tools, components, and totes are often scattered or stored in a disorganized manner, leaving workers to spend too much time searching for required items. Downtime expands while production slows to a crawl.
FlowCell modular workstations can help bring order to the chaos by streamlining workflows and reducing clutter. FlowCell industrial workstations are versatile enough to fit a wide range of settings, whether you need packing stations, kitting stations, assembly, or sub-assembly stations. Combining a clean workstation with accessible gravity flow shelves allows you to keep parts, tools, and components within reach and organized.
Return lanes can also be added above or below FlowCell workstation. These give you a dedicated space for empty totes while keeping the primary workspace clutter-free. Optional pick trays and tool bars further enhance functionality without increasing disorganization.
Challenge #2: Inefficient Lineside Storage and Material Flow
Lineside storage should promote an orderly, efficient workflow, but it often does just the opposite. Empty bays lead to unnecessary bottlenecks, as workers pause and wait for items to be replenished or leave the line looking for parts.
With their gravity-fed design, FlowCell manufacturing flow racks directly address these inefficiencies in material flow. You can easily organize parts and components on a first-in, first-out (FIFO) basis, allowing for easy restocking at the rear so parts never run out in the middle of production.
FlowCell is also built to suit a range of different lineside applications, from straightforward lineside storage to more efficient work-in-progress (WIP) carts. Choose from several size options to fit even the tightest lineside spaces and keep components moving without disrupting flow. Plus, FlowCell units are reconfigurable and adjustable. As demand fluctuates and processes shift over time, FlowCell can easily adapt to your changing needs.
Learn lean manufacturing storage principles. Download the Lean Manufacturing Storage Guidebook!
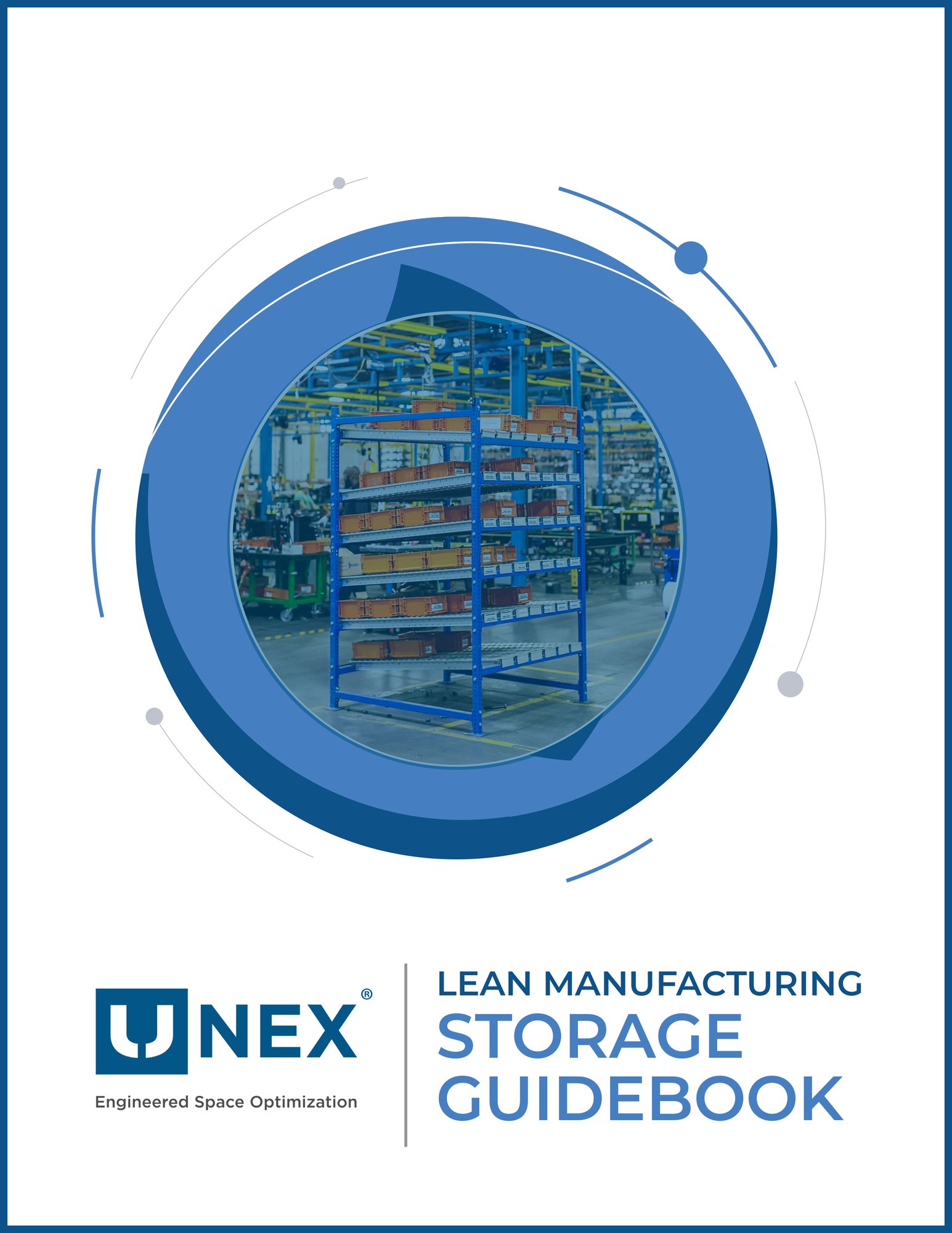
Challenge #3: Lack of Flexibility for Changing Production Needs
Static shelving is not easily adapted to the fast-evolving needs of most manufacturing operations. If production lines switch to different components, batch sizes, or custom assemblies, reconfiguring static systems can be time-consuming, costly, or outright impossible without major retrofitting.
Deploying modular manufacturing workstations makes your operation far more flexible and adaptable. FlowCell stations can be reconfigured in a matter of minutes, with modular components that can be added or removed based on workflow demands. Pick trays, workbenches, and tool bars can all be mixed and matched to build the ideal workstation for your current needs.
Ultimately, designing an efficient manufacturing layout starts with storage solutions that align with your specific workflows. Whether you need stationary or mobile units, roller racks or wheel beds, or a mix of pick trays to suit varying part sizes and kit configurations, UNEX flow racks are flexible enough to tailor to the demands of your operation.
Challenge #4: Limited Space for Parts and Components
As production demands increase, manufacturers often face space constraints on the floor, particularly when accommodating more components, part types, or product variants. Bulky shelving, floor-stacked inventory, and static storage systems can quickly eat up valuable real estate, limit visibility, and slow down access to critical components. These limitations reduce operational efficiency and create cluttered, more difficult-to-navigate work areas that hinder safety and productivity.
FlowCell is designed to clear clutter from the floor and utilize previously wasted space, transforming underutilized areas into efficient flow-through storage. FlowCell flow racks allow you to store parts in well-organized, gravity-fed lanes that keep components visible and accessible. The result? Cleaner sightlines and more ergonomic part presentation that helps workers find and retrieve what they need faster and without strain.
FlowCell is also ideal for creating manufacturing supermarkets, or centralized areas where components are staged and replenished to support lineside operations. These hubs benefit from the same space-efficient, accessible storage, making it easier to manage inventory and streamline picking within a limited workspace.
Whether you’re shifting product mixes or planning frequent changeovers, adding flow racks to your production line supports adaptability without compromising throughput. Ultimately, FlowCell allows you to store 50% more inventory in the same space while boosting production efficiency by 30%.
Challenge #5: Inconsistent Part Presentation and Quality Issues
In manufacturing environments, parts presentation at the point of use has a direct impact on productivity and product quality. Misplaced bins, haphazard component stacks, and improper inventory rotation all increase the chances of picking errors, slowdowns, and even defects in final assemblies. These issues can trigger costly rework, which disrupts downstream processes and risks compromising quality standards.
With features like angled flow lanes and optional pick trays, FlowCell is designed to support consistent, clear, and ergonomic part presentation. These elements guide components to the optimal position at the pick face, keeping them clearly visible and easy to grasp, regardless of part size or shape.
The built-in FIFO functionality of manufacturing flow racks comes in handy again here , ensuring older stock is always used first. This reduces the risk of obsolete parts making their way into production, which is vital for quality assurance in many manufacturing facilities.
Why Manufacturers Choose UNEX FlowCell
There are a variety of manufacturing workstations and storage solutions on the market, but not every one of them equally addresses the biggest challenges facing today’s production facilities. FlowCell has long been a go-to choice among manufacturers seeking durable, efficient, and flexible systems to support lean operations. These industrial flow rack solutions are engineered specifically for the demands of modern production environments, where space is tight, processes are in constant flux, and uptime is critical.
Constructed from heavy-gauge steel with high load capacities, FlowCell workstations and racks are built to withstand harsh, high-traffic conditions. Each system can be designed to fit the unique layout and workflow of your facility, helping you solve specific material handling challenges instead of forcing you to adapt to a less-than-ideal solution.
With a modular design and a wide range of configurations, from workstation storage to mobile units and lineside applications, FlowCell supports continuous, dynamic material flow across every phase of production. It’s this combination of rugged durability, lean-focused design, and tailored flexibility that makes UNEX flow racks a reliable choice for manufacturers looking to streamline operations and stay competitive.
Start Solving Manufacturing Challenges Today
In a manufacturing environment where speed and efficiency are at a premium, flow racks for production lines are a non-negotiable. But to truly overcome the complex challenges of today’s manufacturing demands, you need more than a flow rack. FlowCell goes a step further, bringing together ergonomic part presentation, high-density storage, modular flexibility, and rugged durability in one tailored solution.
From reducing downtime at disorganized workstations to enabling just-in-time delivery of parts on the line, FloweCell supports lean practices at every level. It helps manufacturers make better use of limited space, adapt quickly, and maintain consistent quality, even in the most demanding environments.
Want to learn more? Contact our team of product specialists today to learn how FlowCell can solve manufacturing challenges in your facility!