Optimizing Omnichannel Fulfillment for the Holidays Using Dynamic Storage Solutions
The holiday season has always been the main event for retailers. Some sellers generate close to 35% of their annual revenue in the fourth quarter alone. While that sales surge is critical for business, it also brings a range of complications and challenges.
That’s especially true in the era of omnichannel fulfillment, where many fulfillment centers are pulled in multiple directions, handling an influx of orders for direct-to-consumer shipping and in-store pickup. And, with Amazon setting consumer expectations for fulfillment times higher than ever, the pressure is on all retailers to streamline their operations to meet peak demand head-on.
Many approaches to fulfillment are often hampered by inefficiencies and errors. Without a clear focus on optimizing their omnichannel fulfillment operations, many retailers will fall behind this holiday season. Here are a few tips to ensure your company keeps up the pace.
The Role of Efficient SKU Management in Omnichannel Fulfillment
The days of straightforward, single-channel fulfillment in a brick-and-mortar location are long gone for most retailers. Now, multichannel flexibility is the name of the game. And that brings a dizzying level of complexity, as workers must handle inventory for an array of different fulfillment channels. Orders come from eCommerce, in-store customers, and wholesale distributors — and all require quick access to the same products.
The potential for chaos and disorder only ramps up during the holiday season, making effective SKU management foundational for creating efficient fulfillment practices. Time is of the essence in the final months of the year, and employees charged with order picking must know exactly where each product is while companies need to know how much stock they have on hand and how each product is poised to move through their warehouses.
During the holiday rush, it’s especially important to organize SKUs by seasonality, prioritizing the top sellers for high-fulfillment zones and the most accessible picking locations. Adding dynamic storage solutions to your warehouse can help ensure these high-priority items are most accessible for fast-paced fulfillment.
Speeding Up Order Picking in High-Volume Environments With Carton Flow Systems
Any warehouse operation that expects high sales volume during the holidays would be wise to invest in carton flow systems if they have not already. Unlike standard flat shelving, these dynamic storage solutions use angled shelves that naturally move inventory from the back of the shelf to the pick face. This gravity-based setup allows retailers to implement better first-in, first-out (FIFO) inventory management, loading shelves at the back and letting products move as they’re picked.
SpanTrack Lane and SpanTrack Wheel Bed, for instance, both drop right into existing pallet racks to convert flat, static shelving into a streamlined, gravity-flow system. With inventory angled toward the front of the shelf, pickers gain a better view of each product. They no longer have to peer and reach behind other inventory on flat shelves — everything is within reach for faster, more accurate order fulfillment and more timely inventory movement.
Fulfillment speed goes beyond ease of reach. Carton flow shelving also drastically condenses inventory thanks to more efficient use of shelf space. Placing more inventory within a smaller area results in smaller pick paths for even faster picking and fulfillment. SpanTrack Wheel Bed in particular allows for the most flexibility since multiple-sized products can be positioned within the same shelf level, making re-slotting simple. Carton flow bed "shark fin" infeed guides snap onto the flow bed axles to help guide product replenishment as well.
No matter your SKU size or shape, SpanTrack carton flow solutions enhance order picking processes, reduce labor costs and increase throughput in order fulfillment centers handling multi-SKU orders for online retail.
Learn to optimize warehouse space for increased speed and accuracy. Download the Guide to Understanding Throughput for Fulfillment!
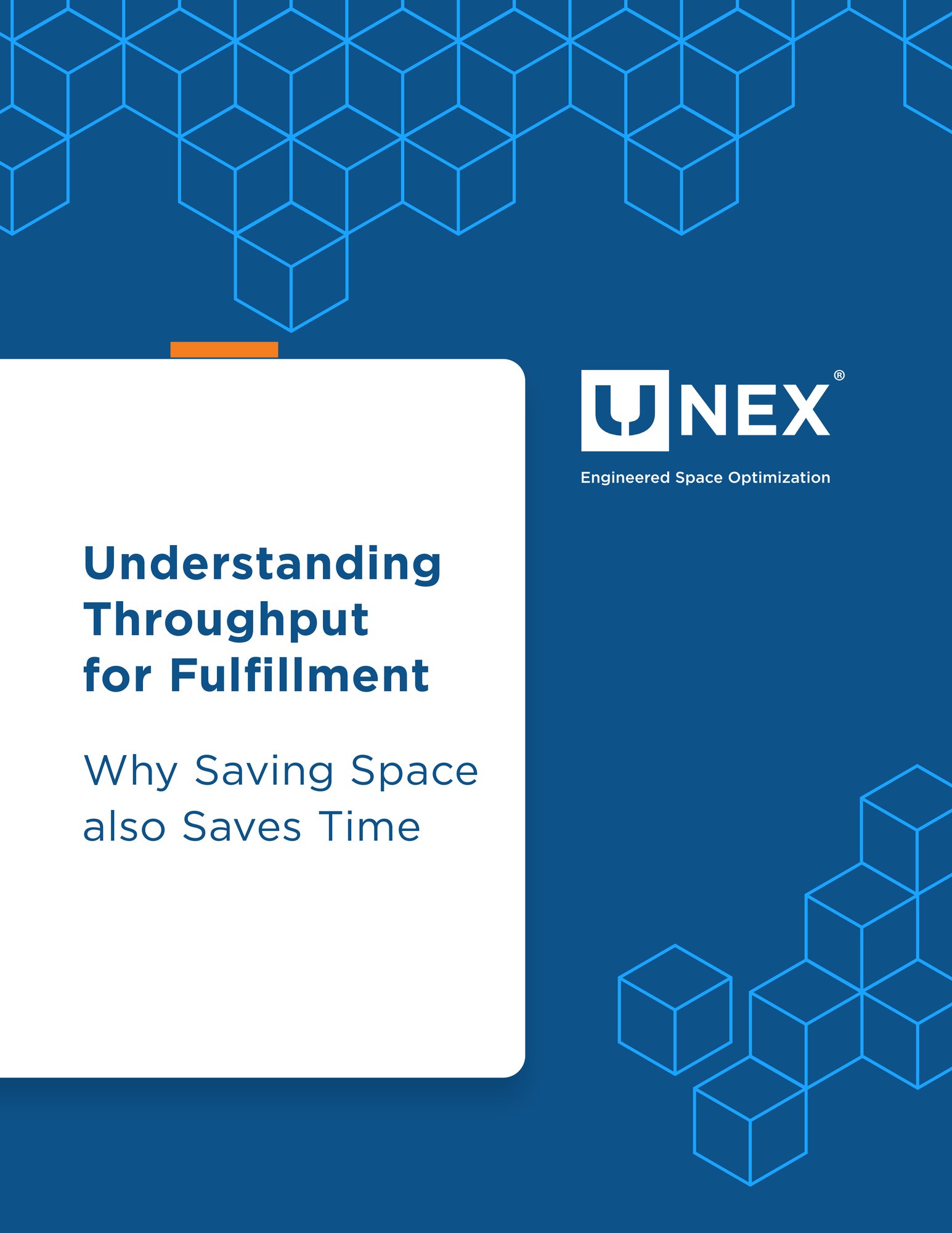
Maximizing Storage Space With High-Density Storage
The reason for many warehouse inefficiencies is simple: Inventory is too spread out. Workers have to travel far on foot or reach deep into shelves to collect items for orders, causing delays in fulfillment and increased labor costs.
Fortunately, the answer to this problem is equally as straightforward. High-density storage solutions allow retailers to condense inventory into a much smaller footprint, putting more products in reach to reduce worker movement and simplify fulfillment.
SpeedCell, for instance, increases storage density by 40% to 60%, compressing 200 feet of static shelving into 40 feet of tightly organized, accessible space. Columns of cells are designed to fit a variety of SKUs. They come in several sizes and are movable for easy access. Pickers can quickly locate products within a small footprint and move on to the next item — an ideal setup for fulfilling online orders or smaller in-store deliveries.
Like our other dynamic storage solutions, SpeedCell makes it easy to swap out inventory and rearrange based on seasonal fast-movers. This is especially critical for retail environments, where seasonal garments and other small holiday gifts take priority during the year-end rush. Individual cells are perfect for sorting sweaters or shoes by size, for instance, helping pickers quickly find and grab items for a surge of holiday orders.
Implementing high-density storage systems like SpeedCell not only reduces picking time but also delivers substantial cost savings. By condensing inventory into a compact footprint, SpeedCell minimizes the time and labor costs associated with locating and picking products. For example, reducing a picker’s average travel distance by even a few feet per order can save valuable seconds that add up across hundreds or thousands of holiday orders, making operations more cost-effective and productive.
Reducing Labor Strain and Improving Worker Productivity
Workers in retail and warehouse environments are always at risk of injury from overexertion or straining to reach items. During peak seasons, when order volumes surge, worker safety becomes an even greater priority.
Both SpanTrack and SpeedCell are designed with ergonomics in mind to help reduce strain caused by bending, reaching, and lifting. By positioning products closer to the pick face and reducing the physical demands of order picking, these dynamic storage solutions create a safer, more efficient work environment. This approach is especially beneficial for temporary seasonal workers, who may be less accustomed to the physical demands of fulfillment tasks.
Having fewer injuries also means happier and more productive workers. And in the holiday rush — when every second counts — more engaged, focused team members can shave seconds off of every order. They’re also less likely to make errors when picking, which ultimately saves money by curbing the deluge of holiday returns.
Prepare for Your Busiest Seasons With UNEX Dynamic Storage Solutions
As a retailer, omnichannel fulfillment puts your products in the hands of more customers than ever. However, as your omnichannel operations expand, if you don’t have organized systems for inventory storage and order fulfillment, the results can be disastrous.
In many retail fulfillment centers, the holidays are the ultimate test of their omnichannel systems. In reality, however, they expose whether you’re ready for fast-paced fulfillment, regardless of the season. Dynamic storage solutions like SpanTrack and SpeedCell can take your omnichannel organization to the next level, ensuring you’re ready to manage peak demand and keep orders moving year-round.
Reach out to UNEX today to learn how these and other solutions will help you optimize your omnichannel fulfillment and keep your operation organized and profitable through every season!