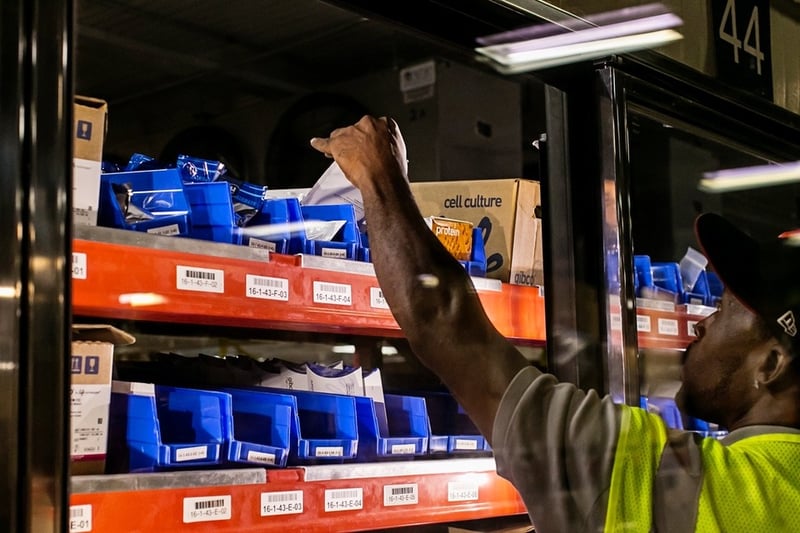
In the fast-paced world of order fulfillment, efficient order picking isn’t just a critical component — it’s the backbone of your operation. As customer expectations for quick and accurate deliveries continue to rise, mastering the small details of order picking can set your operation apart from the competition.
The growth of eCommerce and faster delivery times has made optimization of order picking procedures a top priority for businesses. Whether you’re handling a high volume of diverse SKUs or managing seasonal peaks, the right order picking strategy can significantly impact your productivity, accuracy, and overall customer satisfaction.
In the fast-paced world of order fulfillment, efficient order picking is crucial, and enhancing picking procedures is a top priority for businesses. This article examines the key benefits of optimized order picking, explores best practices, and showcases solutions for streamlining order picking processes effectively.
Benefits of Efficient Order Picking
Order picking is the process of locating and pulling products to fulfill orders in a warehouse or fulfillment center, and it is the first step in fulfilling customers' orders. Getting order picking right has far-reaching benefits for warehouse operations. When order picking goes smoothly, businesses build positive customer relationships by reliably delivering the correct goods on time. It’s also an essential piece of logistics and supply chain management. As the bridge between inventory storage and product delivery, order picking is a crucial checkpoint for inventory control.
Here are the key benefits of an optimized order fulfillment operation:
- Positive Customer Relationships: Timely and accurate deliveries help ensure orders are processed and shipped quickly with minimal errors, leading to higher customer satisfaction and repeat business.
- Enhanced Inventory Control: Facilitates improved tracking and reduces the risk of mispicks or lost items, maintaining optimal stock levels.
- Efficient Use of Employee Time: Optimized picking routes minimize travel time and allow employees to pick more orders in less time, boosting productivity.
- Reduced Physical Strain and Risk of Injury: Ergonomic solutions and safety measures help implement ergonomic tools and safety protocols to minimize physical strain, reduce fatigue, and prevent workplace injuries.
- Competitive Advantage: Efficient order picking provides a competitive edge by enabling faster order processing and adaptability to increased order volumes, resulting in cost savings by reducing labor costs and operational expenses.
By optimizing order picking processes, businesses can enhance the efficiency of their warehouse operations, strengthen supply chain management, and gain a competitive edge in the marketplace. In the following sections, we’ll explore the different types of order picking systems and best practices to help you accurately deliver orders and streamline the rest of your order fulfillment process.

Choosing Order Picking Methods
There are several different ways order picking can be organized. When determining which method or methods to use in your warehouse, it’s important to consider your type and range of inventory, the size of your operation, the volume of products it moves, and customer demand patterns. Choosing the right order picking method for your company can play a critical role in improving your warehouse’s storage density, increasing order accuracy and productivity, and reducing labor costs. Below are some of the most common order picking methods:
Single-Order Picking
Single-order picking involves one worker picking all items for an entire order. While it is the most common way to fulfill orders and can be highly accurate, it is also the most time-consuming and least efficient picking method. Single-order picking can work perfectly well for very small companies with a limited number of products, but successful businesses can quickly outgrow this method and begin to experience slowed delivery times.
Batch Picking
Batch picking groups orders so that a single picker collects all items with the same SKU for a series of orders. This helps minimize travel time for pickers and allows them to work on multiple orders at once. This can be especially valuable for companies that often fulfill multiple orders for the same product.
Zone Picking
In zone picking, each picker is assigned a specific area of the warehouse, and they are responsible for gathering all items within their zone for all orders that come to them. Once a picker has completed their part of an order, they pass it on to the next zone, and the process continues until the order is complete. This limits travel time while also preventing the need for employees to crowd around any product that experiences a surge in demand. However, accuracy can decline as orders are passed through multiple pairs of hands throughout the fulfillment process. Nonetheless, this process can be beneficial for companies that sell high volumes of a large number of products.
Wave Picking
Wave picking is a more complex method that groups multiple orders according to specified criteria, such as priority, destination, or carrier. Pickers collect products in waves that are scheduled throughout the workday to efficiently allocate labor, manage foot traffic within the warehouse, and meet shipping deadlines. Wave picking is most useful for large operations that distribute many different kinds of products in high volumes.
Common Challenges in Order Picking
The order picking process in warehouses and fulfillment centers is often fraught with challenges that can hinder efficiency, accuracy, and overall productivity. These challenges can manifest in various forms and contribute to order delays, increased costs, and customer dissatisfaction.
As order picking plays a vital role in the fulfillment process, be aware of some of the key challenges associated with the order picking process:
- Incorrect Orders: Mistakes during picking can lead to incorrect orders, resulting in dissatisfied customers and costly returns or corrections.
- Inefficient Organization: Poorly organized warehouse layouts lead to wasted time, as workers spend excessive time searching for items.
- Worker Fatigue: Inefficient processes and layouts can cause excessive worker fatigue, reducing productivity and increasing turnover rates.
- Ergonomic Issues: Repetitive strain and poor ergonomics can result in employee injuries, leading to increased absenteeism and healthcare costs.
- Peak Demand and Labor Shortages: During peak times or labor shortages, these challenges are exacerbated, making it even harder to maintain efficiency and accuracy.
In today’s competitive order fulfillment landscape, it’s critical to implement solutions that minimize errors, allocate resources efficiently, and protect workers.

Best Practices for Order Picking
Inefficient order picking processes can lead to a multitude of issues that drain warehouse efficiency, productivity, and profitability. Poorly optimized picking operations are often unnecessarily labor-intensive, struggling with inventory inaccuracies, and wasting valuable warehouse space, leading to reduced throughput, higher error rates, and negative customer experiences. However, there are several steps businesses can take to streamline the order picking process while maintaining high accuracy.
Have a designated location for each SKU.
A place for everything and everything in its place is a notion that’s ideally suited to warehouse environments. Pickers should be able to find each distinct item in a designated and clearly labeled place without taking extra time to sort through multiple SKUs to find what they’re looking for.
Condense storage space.
To minimize picker travel times, it’s necessary to limit the amount of floor space they must cover to retrieve items. Dynamic storage solutions allow businesses to store more items in a smaller space while keeping them organized, clearly labeled, and easily accessible.
Optimize the layout to minimize travel time.
A well-organized warehouse is essential to optimizing pick times. A warehouse management system can help you optimize picking routes and generate efficient pick lists. When condensing storage, be sure to leave sufficient aisle space so pickers can move quickly and easily from one location to the next. Creating one-way aisles can help combat congestion and prevent collisions.
Prioritize ergonomics.
While condensing storage is important, it should not be done at the expense of worker health and safety. Store frequently needed items at ground level for easy picking, and utilize conveyors to reduce fatigue and the risk of worker injuries while protecting products from damage.
Use storage solutions that support FIFO fulfillment.
A first-in-first-out (FIFO) fulfillment model ensures that the oldest items are moved first and helps to prevent waste. Solutions like dynamic high-density storage and carton flow help keep inventory organized and ensure proper SKU rotation.
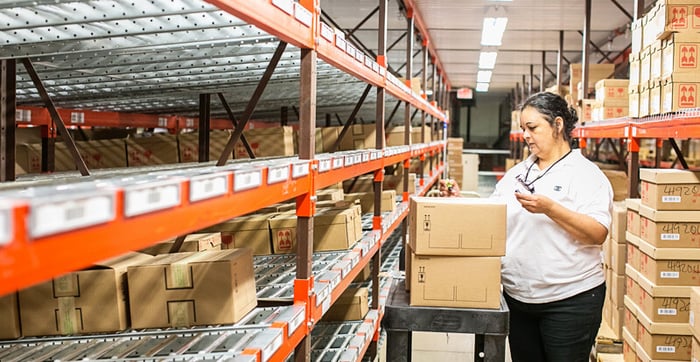
Solutions to Enhance Order Picking
UNEX provides a variety of warehouse storage solutions that help companies minimize inefficiencies, cut costs, improve productivity, and optimize their order picking processes.UNEX offers dynamic storage solutions, such as Pallet Track, SpanTrack, and SpeedCell, that are engineered to address challenges faced by order pickers. These solutions transform less efficient or outdated shelving and rack systems into highly optimized storage.
SpeedCell: High-Density Storage Solution
- Maximize Space Utilization: SpeedCell compresses up to 200 feet of rack or shelving into just 40 feet of highly organized space, making it ideal for small parts and slower-moving items.
- Enhanced Organization: By creating a highly organized storage environment, SpeedCell reduces the time pickers spend searching for items, thereby increasing picking speed and accuracy.
- Flexible and Adaptable: SpeedCell can be integrated into existing operations, providing a flexible solution that grows with your inventory needs.
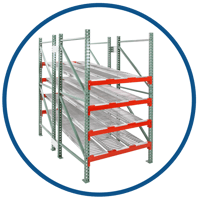
SpanTrack: Efficient Carton Flow Solutions
- Seamless Integration: SpanTrack drops into existing structures, eliminating the need for additional shelving or intermediate supports.
- Versatile Storage: Capable of handling a wide range of item sizes and weights, SpanTrack is ideal for medium to high volume pick rates, providing efficient and ergonomic pick paths.
- Increased Throughput: SpanTrack ensures that products are always at the pick face, reducing pick times and increasing overall throughput.

Pallet Track: Optimized Flow for Fast-Moving Items
- First-In, First-Out (FIFO) Rotation: Pallet Track ensures FIFO inventory rotation, which is crucial for managing high volume and perishable goods.
- Improved Efficiency: Designed for fast-moving items, Pallet Track reduces the manual handling of pallets, speeding up the order picking process.
- Durability and Reliability: Built to withstand the rigors of high-volume operations, Pallet Track offers reliable performance and minimizes downtime.
Optimize Your Operations with the Right Order Picking Solutions
Optimizing order picking is essential for businesses to stay competitive and meet customer expectations in today's fast-paced order fulfillment landscape. By implementing best practices and leveraging innovative storage solutions, companies can streamline their order picking processes, reduce inefficiencies, cut costs, and boost productivity. Solutions like UNEX SpeedCell, SpanTrack, and Pallet Track are designed to transform basic storage shelves into highly efficient and organized systems, minimizing travel time, enhancing inventory control, and promoting worker safety.
By investing in the right order picking methods and storage solutions tailored to your specific needs, your business can not only improve operational efficiency, but also deliver a superior customer experience through timely and accurate order fulfillment. As the backbone of warehouse operations, optimizing order picking can drive long-term success. To learn more about UNEX order picking solutions and how they can benefit your operation, contact us today!
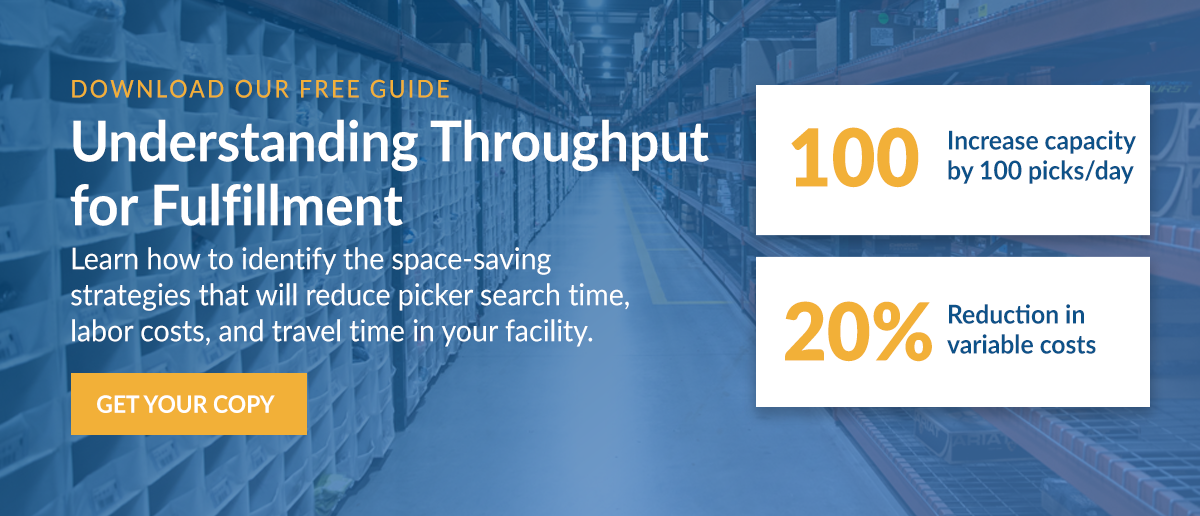