5 Principles of Lean Manufacturing
Key Takeaways
- Lean Manufacturing focuses on maximizing customer value by eliminating the seven types of waste and streamlining every step of the production process.
- The five core Lean principles guide continuous improvement and operational efficiency.
- UNEX products such as SpanTrack, FlowCell, and Roller Rack aredesigned to support Lean initiatives by reducing waste, improving flow, and optimizing workspace organization.
The founders of the Lean Enterprise Institute and the Lean Enterprise Academy, James Womack and Dan Jones, wrote, “Lean Thinking: Banish Waste and Create Wealth in Your Corporation.” The book is considered to be the bible of Lean Manufacturing, written from their in-depth study of the Toyota Production System. Lean principles focus on eliminating waste in the enterprise.
Today, these principles are widely adopted by manufacturers around the world to streamline operations, improve quality, and enhance customer satisfaction. Lean thinking encourages continuous improvement by identifying and removing non-value-adding activities across the entire production cycle. From the shop floor to supply chain logistics, applying Lean methods helps companies remain agile, competitive, and responsive to customer demand while optimizing space, time, and resources.
Seven Wastes of Lean Manufacturing
The essence of lean manufacturing is to maximize customer value while minimizing waste. By creating more value for customers with fewer resources, manufacturers can improve profits and even increase worker safety with the right processes in place.
As we’ve mentioned before the 7 Wastes of Lean Manufacturing include:
- Overproduction – Manufacturing an item before it is required instead of manufacturing Just in Time.
- Waiting - Much of a product’s lead time is tied up in waiting for the next operation; this is usually because material flow is poor, production runs are too long, and distances between work centers are too great.
- Transport – Excessive movement and handling add costs and time to material handling processes. Reducing transport time to move an item from one place to another leads to Lean thinking.
- Over-processing – Spending time on a product feature that does not impact functionality leads to excessive processing. Over-processing can also be attributed to using more expensive equipment when simpler machinery can be used to do the same thing.
- Excess inventory - Takes up space and eats into working capital. A seamless flow between work centers helps to slash inventory and work in progress.
- Excess Motion – Reducing bending, reaching, lifting, and walking can reduce wasted motion.
- Defects – Quality defects result in rework or scrap, adding costs to the manufacturing process.
Learn lean manufacturing storage principles. Download the Lean Manufacturing Storage Guidebook!
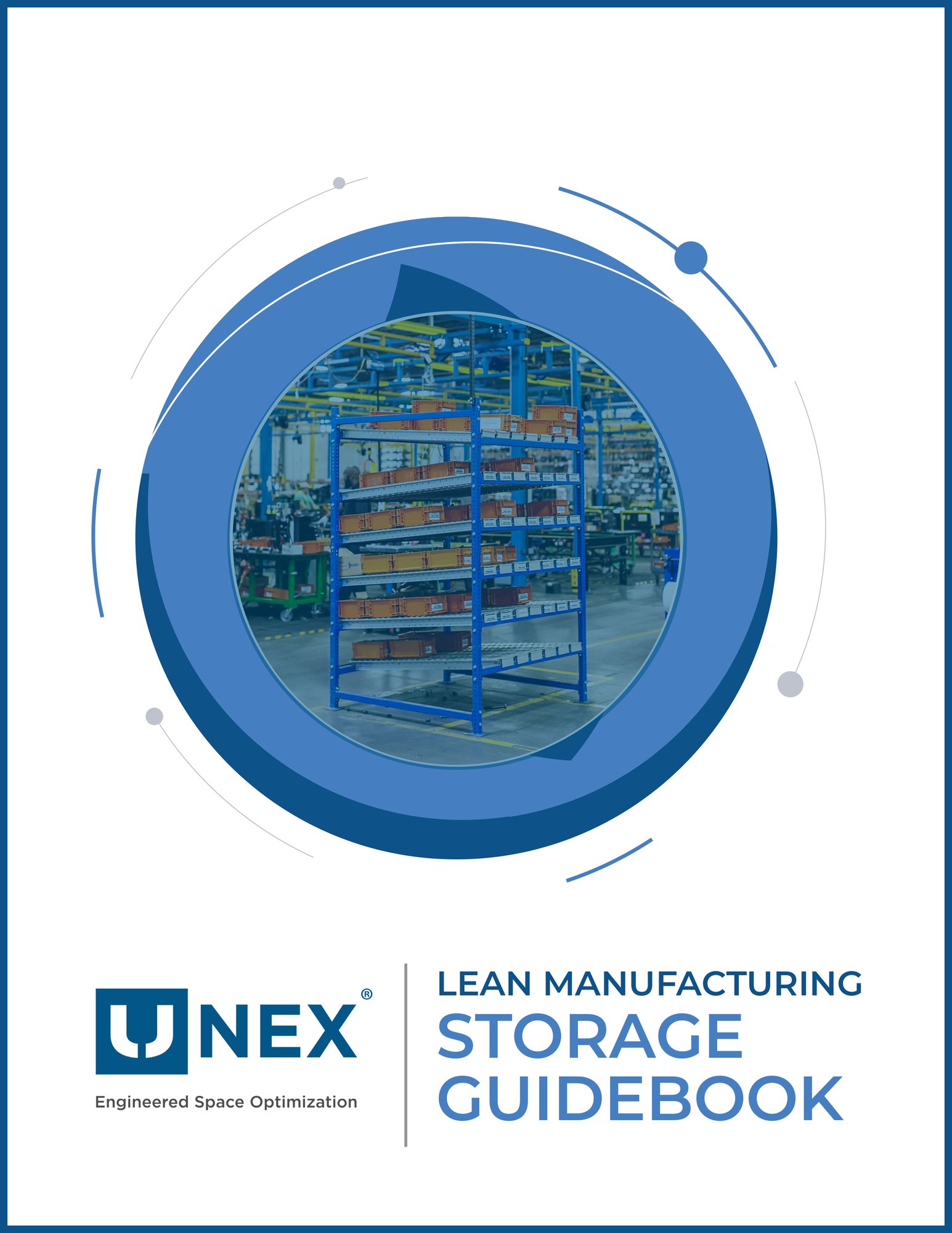
Five Principles of Lean Manufacturing
The book Lean Thinking details five Lean manufacturing principles: value, value streams, flow, pull, and perfection. Each of these principles is described more in-depth below:
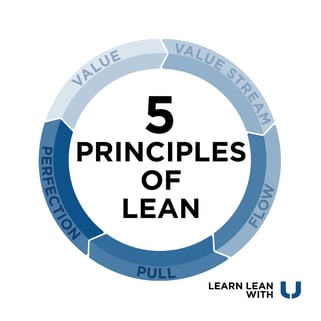
1. Value
Eliminating waste allows manufacturers to deliver value to customers.
2. Value Stream
If the value stream stops moving forward at any point, waste is the inevitable by-product. The lean manufacturing principle of flow is about creating a value chain with no interruption in the production process and a state where each activity is fully in step with every other.
3. Flow
Per Lean Thinking, "Understanding workflow is essential to the elimination of waste when following lean manufacturing methodologies.
If the value stream stops moving forward at any point, waste is the inevitable by-product. The lean manufacturing principle of flow is about creating a value chain with no interruption in the production process and a state where each activity is fully in step with every other.”
4. Pull
In Lean Manufacturing, workflow is precise, making sure things are made just in time at the right time in the right amount. Lean Manufacturing eliminates the traditional manufacturing approach of producing products based on forecast and replaces it with a pull approach that dictates nothing is made until the customer orders it. Flexibility is required along with short delivery cycle times for success.
5. Perfection
The Lean Manufacturing Approach strives for perfection, minimizing defects and waste. As products are made, the pursuit of perfection continues, making for continuous improvements along each step of the process.
UNEX Solutions That Eliminate Waste and Enable Lean Manufacturing
Successfully implementing Lean Manufacturing principles requires not only process discipline but also smart, efficient equipment that reinforces lean behaviors across your operation. UNEX offers a range of space optimization and order picking solutions that directly address the seven wastes—overproduction, waiting, transport, over-processing, excess inventory, excess motion, and defects—while supporting flow, pull systems, and continuous improvement.
SpanTrack: SpanTrack carton flow is ideal for reducing transport and motion waste by bringing products directly to the point of pick. Instead of workers walking aisles and handling items multiple times, SpanTrack condenses storage space and uses gravity-fed flow lanes to deliver products efficiently in FIFO order. This supports the Lean principle of pull by ensuring inventory is replenished only as needed.
FlowCell: FlowCell modular workstations help eliminate over-processing, excess inventory, and waiting by organizing tools and materials at the workstation level. These highly configurable units support just-in-time delivery and provide a visual and ergonomic workspace. By keeping everything within reach and in order, FlowCell makes it easier to identify abnormalities, reduce motion, and maintain clean, efficient work zones.
Roller Rack: Roller Rack systems combine structural frames with SpanTrack to create standalone picking or staging zones that reduce space usage and optimize product flow. They are especially effective in managing value streams by minimizing interruptions and bottlenecks between processes. Roller Racks promote standardization, simplify replenishment, and improve inventory visibility—critical elements in maintaining consistent flow.
Implement Lean Manufacturing with UNEX
Manufacturers and distributors need to remove all elements of waste within their processes in order to fuel growth. UNEX offers space optimization and ordering picking solutions that can help operations minimize waste and maxmize space utilization.
UNEX products help manufacturers implement and maintain Lean Manufacturing practices for safer, cleaner, more productive workplaces. Contact us today to learn how UNEX products can help you reduce waste, improve productivity, enhance safety, and maximize cost savings.
References:
https://books.google.com/books/about/Lean_Thinking.html