5 Ways to Reduce Work in Progress (WIP) in Manufacturing
Key Takeaways
- Just-in-Time (JIT) manufacturing reduces excess inventory and speeds up production.
- Identifying and eliminating bottlenecks increases efficiency and minimizes WIP delays.
- UNEX solutions such as FlowCell, SpanTrack, and Roller Rack support lean goals by enhancing flow, access, and organization.
Work in Progress (WIP) is any inventory that has entered the manufacturing process but is not yet a finished product. Reducing WIP is one of the most important steps in achieving lean manufacturing, leading to smoother workflow, greater liquidity, and overall improved performance of a team’s production.
5 Ways To Reduce WIP in Manufacturing
1. Just in Time Manufacturing (JIT)
Just in time manufacturing is a method of production where materials are only brought in and used as they are required in the manufacturing process. JIT is a fantastic way to reduce many types of waste, especially surplus. The purpose of this method is to get rid of overproduction, waiting, and excess inventory - three of the eight types of waste.
By minimizing these types of waste, manufacturers will have a quicker turnover which reduces the amount of money tied up in materials.
2. Locate Bottlenecks
A bottleneck is a stage in the manufacturing process that is scheduled to complete more objectives than it can produce at maximum capacity. A bottleneck can be as simple as a slow Wi-Fi connection or waiting for approval to proceed with a project.
When a bottleneck occurs, it slows down the work process and requires employees to work overtime or sacrifice other tasks. Removing these bottlenecks will reduce the WIP time, maximizing output. These bottlenecks can be removed by allocating more resources to that stage, usually employees or materials.
When the Work in Progress enters stage C, the manufacturing process will get backed up – this is the bottleneck.
3. Coordinate
Make sure that employees are all focused on a common goal. All employees should understand each part of the manufacturing process, allowing them to perform their respective tasks more efficiently. Workers can better set up the processes that follow and precede them, resulting in faster task completion. With small amounts of time saved in each step, manufacturing WIP is reduced greatly.
4. Upgrade
Upgrading employees and machinery are some of the best ways to reduce WIP in manufacturing environments. The first and most cost-effective step is to offer training. By creating in-depth training sessions and instructions on how to perform tasks, employees will master their trade, reducing WIP. While it is important to have skillful employees, they are only as fast as the tools allow them to be.
Training employees will go to waste unless their materials allow them to perform tasks at a good pace, so upgrading the tools that they work with is key. Keeping equipment up to par is often the most vital part of reducing WIP. Other methods of improvement include hiring more employees, fixing network issues, and offering incentives to employees.
5. Organize
One of the most common bottlenecks is disorganization. Out of 18,000 business leaders, 57% said they lose six working hours per week as a result of disorganization.1 Disorganization can come in many ways, whether it be tools, parts, or information. Any disarray will negatively affect the WIP in manufacturing and cause delays in the process.
One of the most common solutions to this problem in manufacturing is to provide guidelines on which places items should go, along with how many. Labeling storage bins and organizing them will help solve organization issues. By knowing exactly where materials are, transitional time can be reduced so more time is spent on work.
Learn lean manufacturing storage principles. Download the Lean Manufacturing Storage Guidebook!
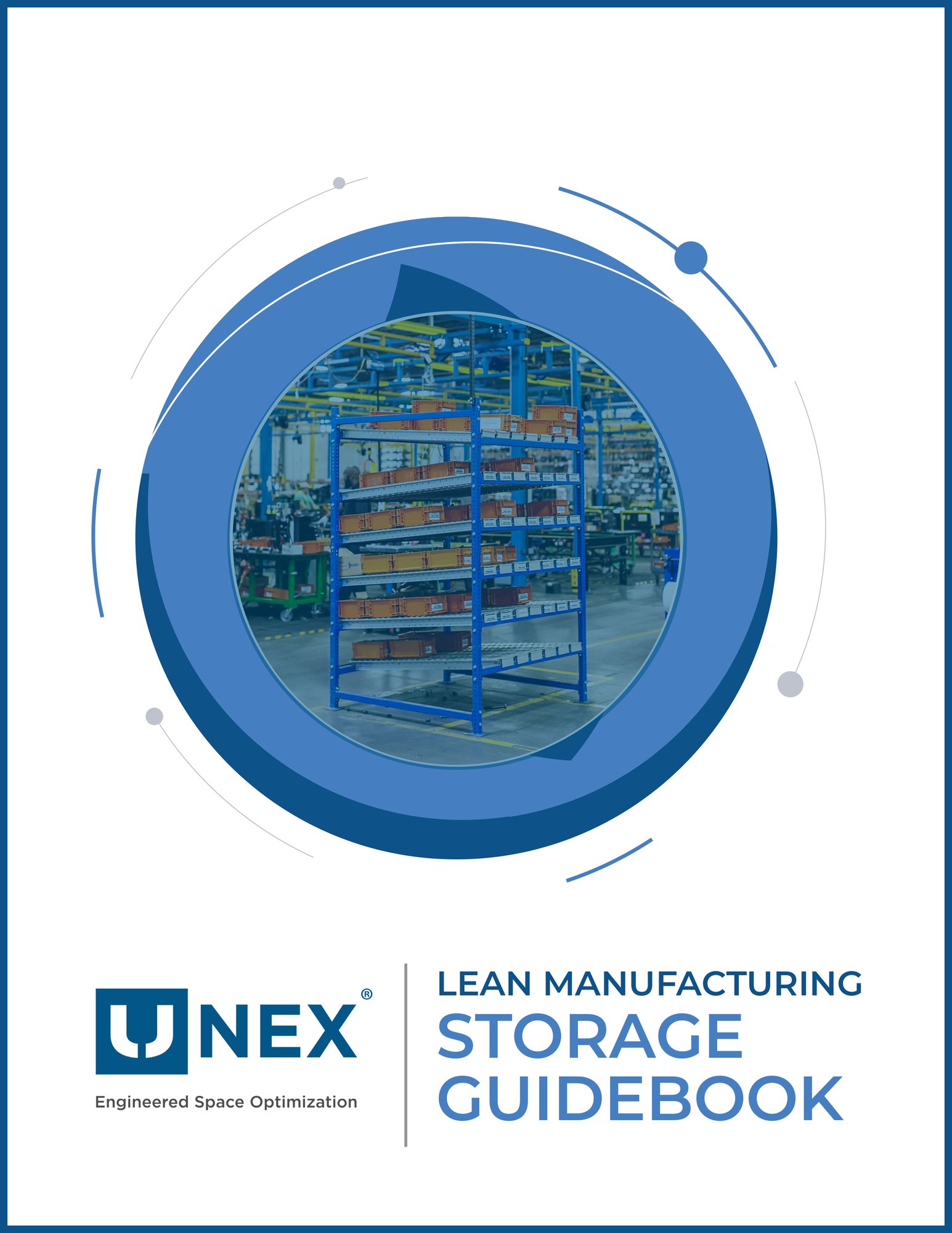
UNEX Solutions to Reduce WIP in Manufacturing
Reducing WIP in manufacturing requires more than process adjustments—it demands equipment that supports lean principles and eliminates production inefficiencies. UNEX offers solutions that directly address common causes of WIP buildup, such as disorganization, bottlenecks, and inefficient part presentation. Here are high-impact UNEX solutions to help you move materials smarter and faster:
FlowCell Modular Workstations
FlowCell is a flexible, modular flow rack system designed to bring materials right to the point of use. Whether you're optimizing lineside storage or building sub-assembly stations, FlowCell ensures consistent FIFO inventory rotation and ergonomic access to components.
Key Benefits:
- Boosts production efficiency by up to 30%.
- Reconfigurable to support line and model changes.
- Keeps workspaces organized and clear of clutter.
- Reduces travel time and material handling waste.
SpanTrack Carton Flow
SpanTrack drops into existing pallet racks to create durable, high-performance flow lanes. Designed to optimize picking and replenishment, it supports both full-case and each pick applications with customizable roller lane and wheel bed configurations.
Key Benefits:
- Enables FIFO for reduced inventory aging and faster returns.
- Minimizes product hang-ups and improves flow reliability.
- Increases SKU density and pick speed.
- Ideal for assembly areas, supermarkets, and workstations.
Roller Rack Gravity Flow Racks
Roller Rack combines welded uprights and roll-formed beams with SpanTrack to create standalone, easy-to-deploy carton flow systems. It’s the perfect solution for facilities that need organized access to parts without overhead pallet storage.
Key Benefits:
- Speeds up pick rates and reduces travel time.
- Provides ergonomic access with knuckled flow lans.
- Modular and scalable to match growing SKU volume.
- Supports lean layouts with dedicated storage bays.
Accelerate Production with UNEX
Reducing WIP is a vital process in lean manufacturing, and achieving this is an ever-evolving practice. By utilizing JIT, locating bottlenecks, and by upgrading, manufacturers can truly begin to achieve maximum production levels.
Obtaining the correct equipment is a crucial aspect of reducing WIP. It can organize the workplace and speed up production significantly, increasing profitability. See how UNEX products can help reduce Work in Progress and achieve peak production efficiency.