Overproduction - Volume or Value? [The 7 Wastes of Lean Manufacturing]
Emphasis on boosting productivity is prevalent in the manufacturing industry. It might seem counterintuitive to name overproduction as the primary source of waste, but across most organizations, it consistently is.
That’s because the volume of work produced does not necessarily correlate with the value of that work.
How Overproduction Leads to Waste
Think about it: manufacturing a product sooner than required – or in higher quantities, than needed – wastes time, labor, and materials. What’s more, having too much product on hand creates excess inventory, which increases the costs of inventory management and storage.
If the product is seasonal, it’s now more likely to end up as scrap. If the product is perishable, it’s now probably headed for a landfill. That doesn’t put you ahead of the game; it puts you behind the eight ball.
Any time you make more product than you can sell, you are producing volume without creating value. In other words, you are creating waste.
Even overfilling food packages – something producers often do to avoid throwing food away – actually creates waste. Food is packaged and labeled based on weight and volume: overfilling not only distributes the unsold product, but it also misinforms consumers at the same time.
In any discussion of organizational waste, overproduction means more than outputting ill-timed or excess manufactured goods.
7 wasteful examples of overproduction in manufacturing include:
- Scheduling more meetings more often than needed
- Generating and distributing too much paperwork
- Creating reports with more detail than its recipients want or can absorb
- Keeping labor and equipment on standby
- Duplicating systems or running redundant processes
- Over-packaging
- Increasing handling and transportation costs
Related Reading: Waiting: Always a Losing Game
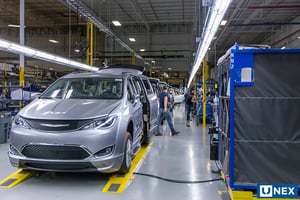
Minimize Waste with Lean Manufacturing
The solution is to balance volume and value by carefully calibrating plans and processes so that production syncs with inventory needs. It’s not a matter of how much you output, it’s whether that output is available, accessible, and acceptable when and where it’s needed. That’s where the value is measured. There’s nothing productive about producing too much.
Lean manufacturing means creating more value for customers with fewer resources. At UNEX, we are firm believers in lean manufacturing (we use many of its principles in our manufacturing processes) and we design all our space optimization and order picking solutions to maximize customer value while minimizing waste.
UNEX specializes in designing Lean, engineered space-saving solutions, serving several industries, including distribution, logistics, retail, and manufacturing. Learn more about how UNEX can help your business boost productivity and maximize storage space within your operation, click here to contact us.