How FlowCell Supports Lean Manufacturing Principles
Key Takeaways
- Lean manufacturing focuses on eliminating waste, and flow racks help reduce excess inventory, movement, and waiting times.
- UNEX FlowCell supports lean principles by enabling continuous flow, just-in-time production, and built-in quality through ergonomic, modular design.
- FlowCell optimizes space, improves productivity, and reduces worker fatigue in dynamic manufacturing environments.
Waste is the enemy in manufacturing — an ever-present obstacle in your mission to minimize costs and maximize value for your customers.
Lean manufacturing is singularly focused on snuffing out that enemy. At every turn in the manufacturing process, a lean mindset asks how you can eliminate waste to deliver more value while expending fewer resources. Every process must be perfected and optimized to continually bend toward perfection.
Within lean manufacturing processes, flow and layout play key roles in minimizing waste. Flow racks — dynamic, gravity-fed shelving racks designed to optimize pick and production efficiency — are an ideal component of this system. And UNEX FlowCell flow racks, in particular, are uniquely designed to support core lean manufacturing principles. Read on to understand how they fit together.
Understanding Flow Racks in Lean Manufacturing
Flow racks are designed to streamline manufacturing processes. These simple, wheel and roller-based conveyor shelves rely on gravity to move manufacturing components to the front of the pick face, improving product accessibility. Because items move forward on rollers or wheel beds as they’re picked, manufacturers can store more inventory within less shelf space, thus reducing “storage sprawl” and worker travel time.
These objectives are right in line with lean manufacturing’s central ideas. At its heart, lean is all about stripping the manufacturing process of any activities that do not add value. The ultimate goal is to deliver the highest possible quality at the lowest possible cost.
By enabling a more optimized, accessible storage and picking area for the manufacturing line, flow racks help warehouse and manufacturing operators more readily implement lean systems. From the get-go, adding flow racks to the manufacturing floor establishes a more organized, efficient picking area that fits seamlessly with the streamlined approach central to the lean mindset.
Lean Manufacturing Principles Supported by Flow Racks
Using flow racks in manufacturing does more than reinforce lean concepts at a high level. These dynamic storage systems specifically support four critical lean manufacturing principles.
1. Elimination of Waste
As we touched on, waste is the central antagonist in lean manufacturing. Its processes are all built around eliminating eight different types of waste — three of which flow racks address directly:
- Excess inventory: Flow racks streamline first-in-first-out (FIFO) inventory processes and increase inventory visibility, making it much easier to track and manage stock levels.
- Unnecessary movement: With parts and components easily accessible at the pick face and condensed within a smaller footprint, manufacturers can limit the movement of workers, machinery, and equipment involved in stocking and picking.
- Waiting: Flow racks reduce the time employees spend pulling inventory from the back of shelves or waiting while another worker retrieves parts from somewhere else on the floor. This accelerates the entire manufacturing process and maximizes labor efficiency.
2. Continuous Flow
Creating a continuous flow to the assembly line is critical to reducing waste in manufacturing. Workers must be able to focus on their part of the process without stopping to wait or traveling to retrieve parts.
Because continuous flow is built into their design, flow racks provide the ultimate lean storage solution. Whether they’re set up for lineside storage, on modular mobile carts, or integrated into assembly workstations, flow racks keep inventory moving freely from one process to the next.
3. Just-In-Time (JIT) Production
Toyota made the lean manufacturing promise famous in the 1980s with its focus on “just-in-time” (JIT) production and inventory management. Under this approach, production should be fine-tuned so that inventory supply and demand are in perfect sync. In other words, there’s never too much on hand, but there’s always just enough.
As a dynamic storage system, flow racks are ideal for this level of precision in inventory management. Their flexible, modular design allows manufacturers to lay out the shop floor and inventory flow to fit their exact specifications so that the right inventory is always within reach. A more efficient layout can reduce the number of workers on hand, eliminating crowding and enabling faster picking for JIT production.
4. Built-in Quality
The lean manufacturing process is as focused on improving quality as reducing waste. Its “5S” system — sort, set, shine, standardize, and sustain — is geared toward continuous improvement, both in terms of efficiency and product quality.
Flow racks facilitate consistent quality control by making it easier to access parts and keep them well organized. When components are aligned in smooth-flowing, accessible lanes, it’s much easier to keep them in good condition and reduce the risk of damage.
Learn lean manufacturing storage principles. Download the Lean Manufacturing Storage Guidebook!
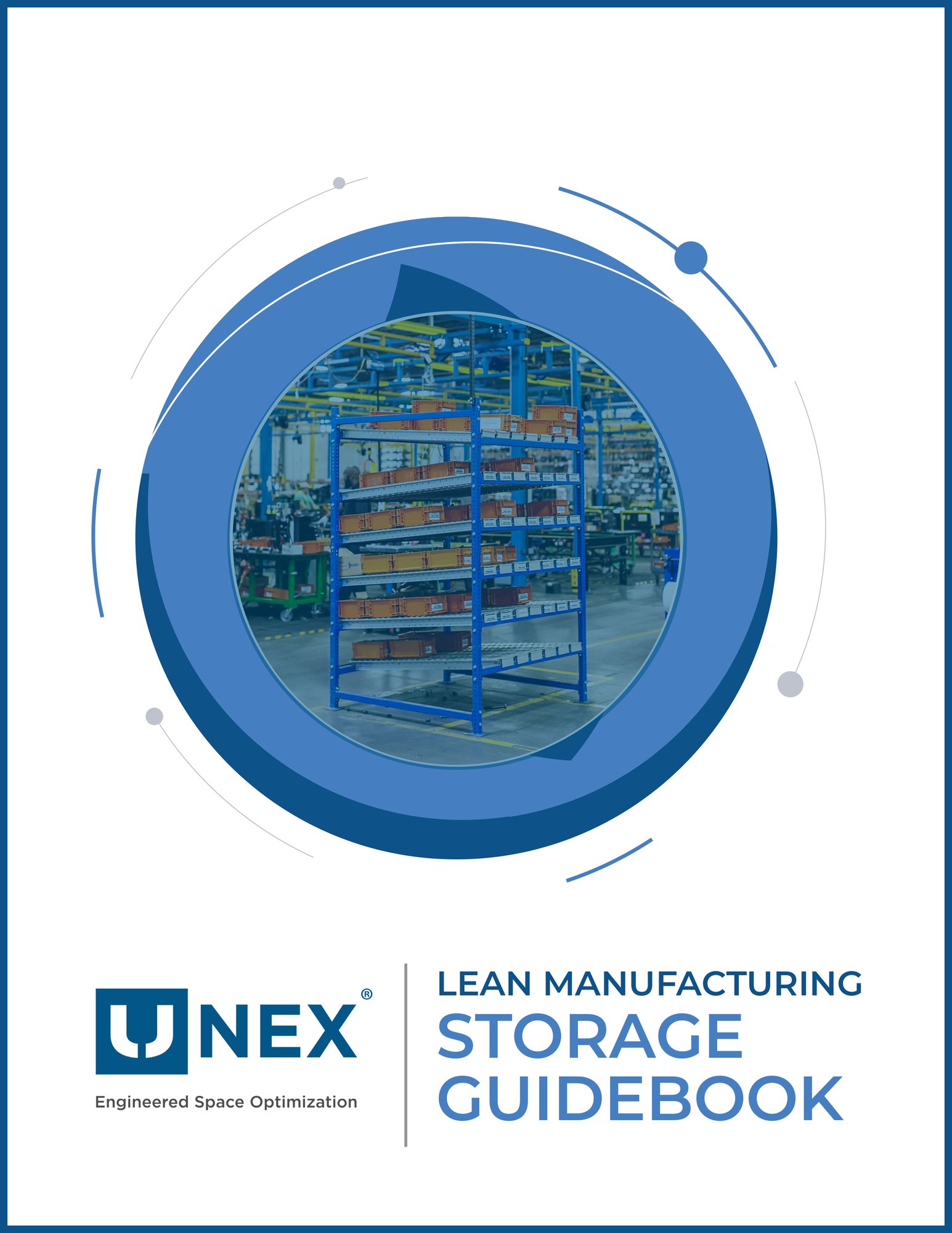
Advantages of Flow Racks in Supporting Lean Manufacturing
Aside from directly supporting lean manufacturing principles, flow racks bring additional distinct advantages that make them an ideal lean storage solution.
- Space optimization: Traditional static shelving relies on a lot of space, spreading inventory horizontally across the warehouse floor. While this is necessary in some cases, it’s often antithetical to lean processes. Flow racks maximize space utilization, freeing floor space for more value-added manufacturing and assembly activities.
- Increased efficiency and productivity: Relying on good flow rack design rather than worker movement to keep parts accessible is inherently more efficient. When workers can quickly access the materials and tools they need, they can focus on the job at hand — making the whole assembly line faster.
- Ergonomic benefits: Flow racks also support greater productivity by reducing worker fatigue and limiting the risk of injury. Gravity-fed shelves reduce the need for reaching, bending, lifting, and carrying, making every movement more effective and less tiring.
- Scalability and flexibility: Like flow racks, the lean manufacturing process is inherently dynamic. A lean approach is adaptable and flexible, shifting and scaling with your business as it grows or demand shifts. Using flexible flow racks in manufacturing supports this method, allowing users to reconfigure workstations, lineside storage, and mobile carts as needed.
UNEX's FlowCell: Enhancing Lean Manufacturing
While any flow rack system will support lean manufacturing principles in your warehouse, not all solutions on the market are designed to fit as neatly within the lean system as FlowCell modular flow racks.
With FlowCell flow racks from UNEX, manufacturers can create a number of solutions to meet their unique needs, whether they run an automotive assembly line or a computer manufacturing facility. This sets the stage for continuous improvement and growth within the manufacturing environment.
Specifically, FlowCell supports a lean approach in three ways:
- Modularity: FlowCell is as flexible as the lean mindset. It is easy to build and highly reconfigurable so the solution can be adapted as your needs change.
- Durability: With heavy steel construction, FlowCell flow racks can bear the brunt of a high-powered assembly line. Heavy automotive parts are no problem for these dynamic flow racks.
- Ergonomic design: FlowCell makes it much easier for workers to access components and minimize movements on the assembly line and in the manufacturing warehouse. This ergonomic design boosts production and reduces the risk of injury and fatigue.
Manufacturers have used FlowCell to improve even the most complex operations. At the Daimler Trucks Components & Logistics facility in North Carolina, the company installed 40 FlowCell stations lineside to maximize product density and minimize worker movement. This enabled Daimler to quadruple the number of parts moving through its facility.
Implementing Flow Racks for Lean Manufacturing
Lean manufacturing relies on shifts in mentality and processes, but it also requires companies to deploy tools designed to optimize production and minimize waste. Few solutions are better built for this task than FlowCell flow racks.
FlowCell’s durable, modular, ergonomic design helps manufacturers optimize space, boost productivity, and improve processes and flow throughout a facility. Ultimately, this supports lean initiatives by eliminating waste while maximizing product quality.
Are you ready to take your lean manufacturing processes to the next level? Contact UNEX to learn how FlowCell flow racks can improve your operations.