Lean Manufacturing 101
At UNEX, we believe in the benefits of Lean Manufacturing, and we use several lean principles in our manufacturing process.
The core idea of lean manufacturing is to maximize customer value while minimizing waste. Being lean means creating more value for customers with fewer resources. The term "lean" was coined to describe the Toyota Production System (TPS) during the late 1980s by a research team headed by Jim Womack, Ph.D., at MIT's International Motor Vehicle Program. There are many terms associated with lean manufacturing – so many in fact that it can be confusing.
5S System
5 Pillars with the goal of getting products closer to operations and workers, organized and labeled to eliminate wasted time and materials. The 5S lean manufacturing philosophy is "a place for everything and everything in its place".
5 Pillars of the 5S System
- Seiri or Sort = Tidiness
- Seiton or Set in Order = Orderliness
- Selso or Shine = Cleanliness
- Seiketsu or Standardize = Keep organized
- Shitsuke or Sustain = Discipline
Kaizen means continuous improvement and relies on employees to make suggestions for improvements. It is a concept that we share here at UNEX. Our sales team understands customers' issues and challenges then shares this with our engineers to build a solution to solve those problems and provide sustained value to customers' operations.
Kanban means visual cards used to control the flow of goods, adjust inventory or production levels, or communicate tasks. Kanban is used to reduce waste by improving supply chains efficiency in manufacturing.
Total Productive Maintenance (TPM) offers 8 pillars for proactively managing preventative maintenance, helping to keep machinery in top shape to avoid delays in the manufacturing process.
Andon is a system for notifying management about a problem. Workers are empowered to stop production for defects and immediately call for assistance. Typically Andon involves a combination of lights or sounds to communicate the status.
Heijunka means lean production system leveling and is used to reduce Mura (unevenness), which reduces Muda (waste). The goal is to produce intermediate goods at a constant rate so that further processing may also be carried out at a constant and predictable rate. It also keeps levels of inventory down.
Gemba means "The Real Place," and encourages management to do the "Gemba Walk" - to walk around the facility and encounter employees at their workplace. It helps managers learn about any ongoing issues first-hand.
Hoshin Kanri means "compass management," but is a way for strategic corporate goals to be communicated throughout a company and then put into action. It is a big picture, top-down approach that ensures workers' tasks contribute directly to the company's broader goals.
Ishikawa Diagrams are cause-and-effect diagrams that help identify the root cause of inefficiency or problem in the plant using "5 whys" to find the answer.
Muda means unevenness or wastefulness. The goal of Lean is to reduce waste. The seven wastes of lean manufacturing are overproduction, inventory, waiting, motion, transportation, rework, and overprocessing. With less waste, businesses are more productive, efficient, and profitable.
Overall Equipment Effectiveness (OEE) means to evaluate the effectiveness of a manufacturing operation or machine. OEE measurement is typical with key performance indicators (KPIs) that analyze downtime, performance, and output quality.
Plan, Do Check, Act (PDCA) is a standardized framework for problem-solving and improving efficiency. It is an iterative four-step management method used in business for the control and continual improvement of processes and products. It is also known as the Deming Circle.
Standardized Work means creating and implementing best practices for an organization or process to make the business more efficient.
Visual Factory means visually displaying information to workers, so they increase productivity and efficiency. This technique is part of the Pick-to-Light solution where lights tell order pickers what products to select to fill an order.
Cellular Manufacturing or "one-piece flow" or U-Shaped Cells is a lean methodology encompassing the movement of a single product through the manufacturing process. One-piece flow redirects the workforce away from non-value-added activities, such as having to search for parts and focusing on the manufacturing process.
Bottleneck Analysis is a way to uncover bottlenecks or barriers in the production process and develop methods that remove the particular issue causing the problem.
ABC Analysis is an inventory categorization technique that ranks products in one of 3 categories: "A" items are the most important to the organization; "B" items are less important, and "C" items are the least important. The ABC analysis provides a mechanism for identifying items that have a significant impact on overall inventory cost.
Continuous Flow Manufacturing entails running manufacturing processes with minimal disruption and little downtime. The goal is an optimally balanced lean production line with little waste, the lowest possible cost, on-time, and defect-free production.
Learn lean manufacturing storage principles. Download the Lean Manufacturing Storage Guidebook!
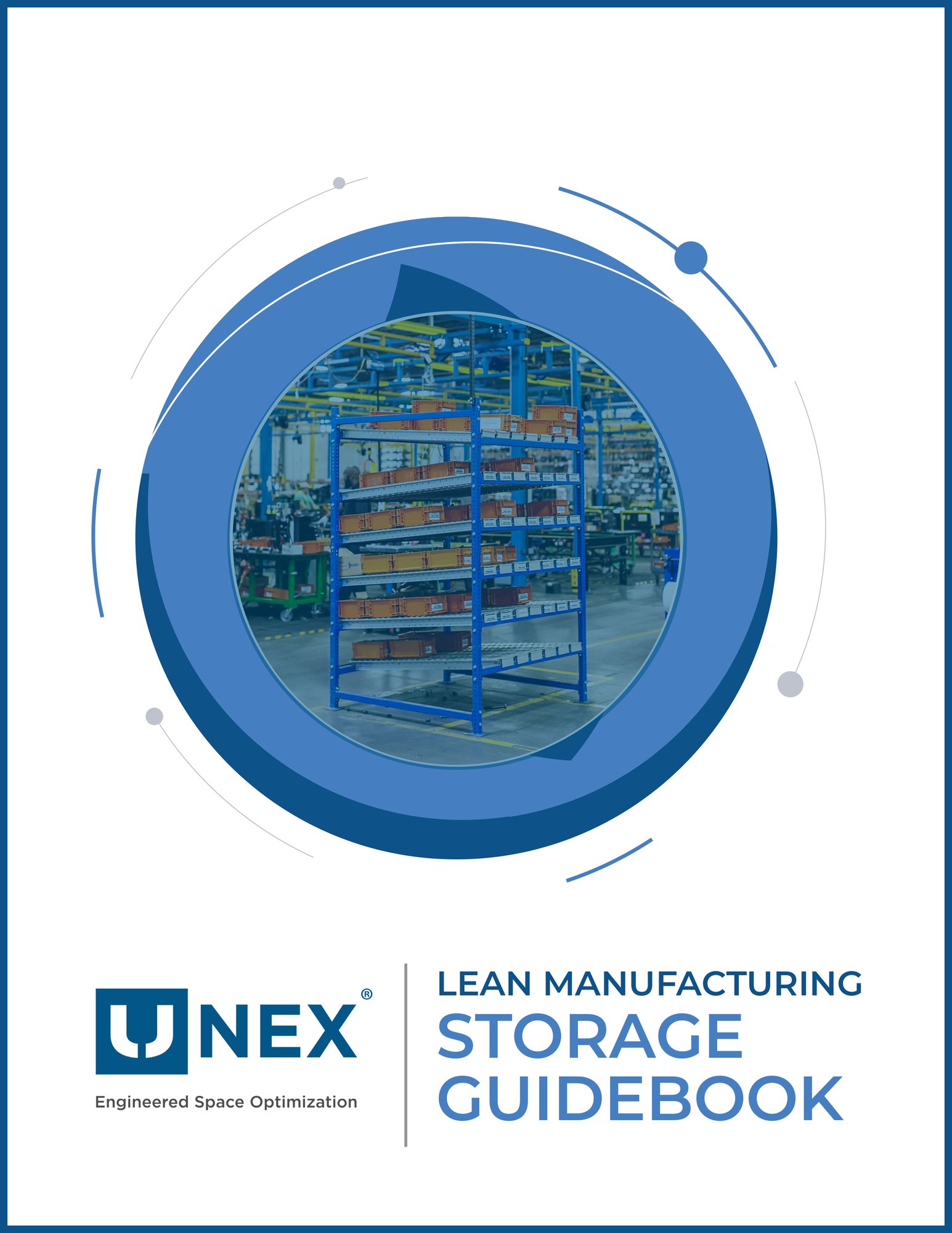
Jidoka means intelligent automation and empowers workers to shut down a machine or stop production if there is a problem without waiting on a manager's permission. It involves 4 processes: detect a problem, stop systems, fix the problem, investigate the root cause.
Just-In-Time is a manufacturing methodology where raw materials, parts, or components arrive at a manufacturing step "just-in-time" for the process to occur. With just-in-time manufacturing, items are made in response to actual demand to minimize storage and excess inventory.
Key Performance Indicators (KPI) are a measurement technique for tracking progress in continuous improvement. KPIs must be clearly-defined, continually measured, and analyzed for progress.
Level Loading is a technique where goods are produced at a steady, constant rate so that the manufacturing process is balanced. With level loading, inventory levels are kept low, and efficiencies are improved.
Mind Maps are diagrams used to visually organize information, showing relationships among various ideas that are all connected to a central concept. For problem-solving or to uncover new opportunities, use mind maps.
Poka-Yoke means mistake-proofing and is a mechanism for avoiding mistakes in the manufacturing process and preventing defects. Poke-Yoke prevents defects in the production process and cuts down on rework.
6 Big Losses identify and plan for the six most common productivity losses, which include unplanned stops, planned stops, small stops, slow cycles, production rejects, and startup rejects.
Single Minute Exchange of Die (SMED) is a lean production method for reducing waste in the manufacturing process. It provides a fast and efficient way of converting a manufacturing process from running the current product to running the next product. The changeover needs to take place in less than 10 minutes.
Takt Time is the average time between the start of production of one unit and the start of production of the next unit.
SMART Goals mean Specific, Measurable, Attainable, Relevant, or Results-Focused, and Time-Specific goals that help improve worker productivity, time management, and efficiency.
Value Stream Mapping is a lean-management method for analyzing the current state and designing a future state for the series of events that take a product or service from its beginning through to the customer. Analysts look at the visual map and find areas of waste or bottlenecks.
No Defects is a methodology for eliminating all defects in the manufacturing process. It is a proactive approach for uncovering defects and finding solutions to eliminate them.
UNEX specializes in designing engineered space-saving solutions for Lean Manufacturing Operations, serving several industries, including distribution, logistics, retail, and manufacturing. Learn more about how UNEX can help you boost productivity and maximize storage space within your operation, click here to contact us.