4 Best Practices for Warehouse Order Picking
With eCommerce giants such as Amazon promising millions of products with unbelievably quick delivery speeds, warehouse and distribution centers are struggling to keep up. To stay competitive in the market, companies must effectively use warehouse space to expand their digital operations, cut delivery time and costs, and keep up with order fulfillment.
To meet demanding turnaround times, optimizing existing storage space to streamline order picking operations is critical. Optimized storage spaces enhance workflow productivity, increase picking speeds, and improve accuracy.
By taking a deep dive into their order picking operations and ensuring they align with these best practices, companies can increase warehouse and order fulfillment efficiency to maintain a competitive stance in the industry.
4 Warehouse Order Picking Best Practices
1. Condense Inventory to Reduce Picker Travel Time
The more time a picker has to travel to find the items that they need, the less time they spend packing and sending off orders for deliveries. Finding ways to reduce picker travel times increases order picking speeds and allows you to get more productivity out of existing internal resources.
Condensing inventory into a single, well-organized location helps increase pick facings, which results in less time spent on search and travel for order pickers. Warehouse storage solutions help companies save on pick times and reduce picker travel times. High-density storage solutions consolidate storage capacity and provide greater SKU density to lessen travel and search time for order pickers.
What impact can these simple storage changes make on your operations?
Imagine this: Your 25-person warehouse staff makes $15 per hour with an average picking speed of around 60-70 lines per hour. This puts labor cost per pick at about $0.25.
By increasing pick rates by 20%, the company benefits from an extra 2,400 picks per day, 12,000 per week, and over 600,000 picks per year! If you need the capacity, these additional picks could mean substantially more revenue for your company.
If you don’t need additional capacity, you can divert more employees to other value-added tasks and reduce your order selection labor by over $150,000 per year!
Warehouses and distribution centers can leverage storage solutions to reduce picker travel times, decrease labor costs, and improve worker comfort and productivity.
Learn how to save space in your facility. Download The Guide To Optimizing Warehouse Space Utilization!
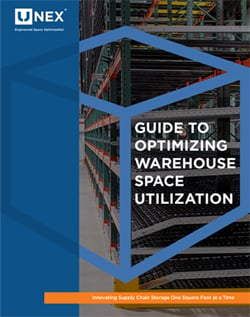
2. Label Inventory to Improve Warehouse Order Picking Accuracy
While a high-density storage system has value on its own, it’s only truly helpful if stored inventory is easily identifiable. For larger operations that have significant quantities of inventory, the time saved in picker travel time could quickly be negated by an inadequately labeled storage system.
Unfortunately, in a fast-paced environment like order fulfillment, maintaining the integrity of a labeling system can be a challenge. Because of this, the investment in durable storage solutions with equally durable built-in label holders helps maintain order.
A well-labeled storage solution not only keeps inventory organized and easy to identify but also results in an optimized picking process and increased speed and accuracy.
3. Reinforce FIFO with Inventory Storage Solutions
Using the First In First Out rule, or FIFO, not only ensures goods are sold as they come in, but also helps warehouses avoid potential waste and calculate inventory costs.
While maintaining FIFO in a warehouse primarily falls on the workers, inventory organization within the warehouse can play a major role in ensuring their success.
When integrated into existing carton flow rack systems, wheel beds are a practical solution that helps to maximize space and create an ideal FIFO storage flow. Rear-fed storage solutions ensure replenishment from the back does not interfere with operations from the front. Even something as simple as angled pick shelving helps the product to slide forward when removed from the front.
Following FIFO is critical to success in distribution and warehouse applications. Leveraging storage systems to support warehouse staff not only increases worker comfort but also has positive impacts on overall efficiency.
4. Continuously Improve Processes and Procedures
The warehousing industry is continually changing and market forces such as seasonality can directly impact the number of SKUs required to fulfill orders and the warehouse order picking speed required to keep up with demand. In an ever-evolving industry, continuously re-evaluating distribution processes and procedures to ensure alignment with current industry requirements is key to maintaining a competitive position in the market.
Implementing scalable storage solutions ensures that warehouses and distribution centers can accommodate seasonal market forces and improve efficiency.
Experience the Engineered-to-Order Difference
High-density and FIFO-reinforcing storage, a reliable labeling system, and continuously-optimized warehouse processes and procedures are an excellent start for optimizing your warehouse order picking operations. But, optimizing warehouse order picking processes doesn’t involve a one-size-fits-all solution. Every warehouse and distribution center has unique needs and requires a built-to-order approach to maximize efficiency and streamline order picking operations.
At UNEX, we understand that every warehouse has a unique and diverse set of products. That’s why we design and manufacture storage products and solutions tailored to your storage space. Contact us today to help enhance workflow productivity, increases picking speeds, and improves accuracy.