
In a warehouse, inventory may be stored in hard-to-reach areas, and you must use equipment, such as a forklift or a man-aboard order picker, to reach SKUs. As a result, workers are often in danger of being hit by objects falling from heights or by reaching and bending into rack and shelving to get to a product. In addition, improper handling of boxes, pallets, cartons, and items can cause strain and injury.
Common Warehouse Injuries and How to Avoid Them
Warehouse hazards, though, create more accidents because of the massive quantities of products of all different sizes, shapes, and weights stored on shelves, floors, and anyplace else someone can find a place to put a box, pallet, or carton. Often order pickers have to take on the overextend if they want to pick an item from a tall shelf.
Slips, trips, and falls
More than 8 million Americans will be treated in emergency rooms yearly due to an accidental fall. Suppose items are stored haphazardly within the distribution center, such as sticking out too far from a shelf or placed in the middle of an aisle. In that case, workers can easily injure themselves by tripping over or running into these items. Making sure floors are dry and slip resistant can prevent slips, trips, and falls.
There is an additional risk when stepping into a rack to pick an item while picking on a man-aboard order picker. Warehouses that use manual picking have to put a person up to those towering heights to retrieve picks that aren’t full pallets (which they would use a forklift for). Not only does that expose a picker to the over-exertions of bending and reaching into racks, but they also have to do it 20 feet off the ground—a recipe for disaster.
Lifting, reaching, and overexerting
Lifting and Handling Materials
Improper handling of boxes, pallets, cartons, and items can cause strain and injury to different parts of the body, especially the back. Heavy, big objects should be placed in the “golden zone,” where workers do not have to bend, reach or lift above their shoulders or below their waists.
Overexertion Injuries
Overexertion injuries occur when workers lift big and heavy items for a long time, resulting in excessive physical effort. Injuries can occur to joints and ligaments. Also, in the warehouse, workers walk to pick orders. The travel time between picks can be long, especially in poorly organized warehouses. Properly planned pick paths, SKU rationalization, and appropriate slotting of SKUs can help to cut down the length the worker must travel to fill orders.

Falling objects and forklift accidents
Falling Objects
Items not appropriately stored can fall and injure someone. If the storage racks do not have end caps, items can slide right out onto the floor, causing injury. Training employees on how to stack inventory properly and decreasing the amount of heaving objects on high shelves can significantly reduce the number of injuries in the facility.
Forklifts
Most accidents occur in a warehouse at/on the docks, forklifts, conveyors, storage units, and manual lifting/handling. Forklifts can overturn, or they can be overloaded, subjecting materials to falling off. Accidents between forklifts or between a forklift and another surface can cause serious injury. Statistics show that 1 in 10 forklifts are involved in an accident yearly. To ensure all are working correctly, operators must check hydraulic levels, tire pressure, engines, controls, steering, and brakes daily. Forklift work platforms can minimize risks for those doing overhead tasks.
Reduce Injuries by Implementing Ergonomic Storage Equipment
A good ergonomics program can decrease the risk of injury, reduce travel time for workers, and optimize space – driving significant improvements to the bottom line and a more efficient operation overall. As part of any ergonomics program, heavy, big objects should be placed in the “golden zone,” where workers do not have to bend, reach or lift above their shoulders or below their waists.
Also, workers can injure themselves by reaching deep into the pallet rack to pick inventory. If the cartons are stored on a pallet on the floor, they have to bend and reach, limiting their ability to lift the carton properly and increasing their odds of injury. In addition, if the carton is stored deep within the pallet rack, visibility and reach are compromised, further jeopardizing the worker’s safety when picking a case.
Pallet flow systems can ensure that the cartons are at the point of pick and that workers do not have to climb into a pallet rack to reach them. Tilted pick trays allow workers to better look at cartons stored higher in the pallet rack and pick that case without blindly reaching into the rack or scaling the beams. In addition, implementing a carton flow system will allow inventory to flow to the point of the pick, so workers avoid overextension and injury.
UNEX Solutions for Enhancing Efficiency and Safety
To address these challenges and improve both safety and efficiency in warehouse operations, UNEX offers several innovative solutions designed to reduce excessive motion, enhance ergonomics, and streamline picking processes.
Pallet Track
Pallet Track is an efficient pallet flow system that enhances storage density and picking efficiency. This system allows for a gravity-fed flow of pallets within your storage racks, ensuring that products are always at the pick face, reducing the time and effort required for retrieval. By optimizing the movement and storage of heavy items, Pallet Track minimizes unnecessary lifting and bending, thereby improving worker safety and productivity.
Carton Flow Solutions
SpanTrack Lane
SpanTrack Lane is a high-density carton flow solution designed to maximize storage efficiency and accessibility. This system is ideal for operations that require precise, organized storage with easy access to cartons and totes. SpanTrack Lane can be easily added to new or existing pallet racks without the need for shelves or intermediate support, making it highly versatile. Its superior flexibility accommodates a wide range of product sizes and weights, ensuring smooth, gravity-fed flow and reducing product hang-ups. Engineered to withstand the rigorous demands of active warehouses, SpanTrack Lane provides long-term durability and reliable performance.
SpanTrack Wheel Bed
SpanTrack Wheel Bed offers a flexible and adaptable carton flow solution that transforms static storage into dynamic, high-density storage. SpanTrack Wheel Bed uses a bed of staggered wheels that can accommodate cartons and totes of various sizes, making it ideal for operations with a diverse range of products. This solution ensures a smooth flow of items and can be integrated into any existing pallet rack structure, enhancing storage density and picking efficiency. The robust construction of SpanTrack Wheel Bed can handle high-volume picking environments, minimizing product damage and increasing throughput.
Ergonomic Solutions for Safer, More Efficient Warehouses
UNEX manufactures a variety of ergonomic order picking solutions designed to enhance efficiency and safety in warehouse operations. Whether you need to optimize space, reduce travel time for workers, or minimize the risk of injury, UNEX has the solutions to meet your needs. Contact us today to learn more about how UNEX can help transform your warehouse into a safer and more productive environment.
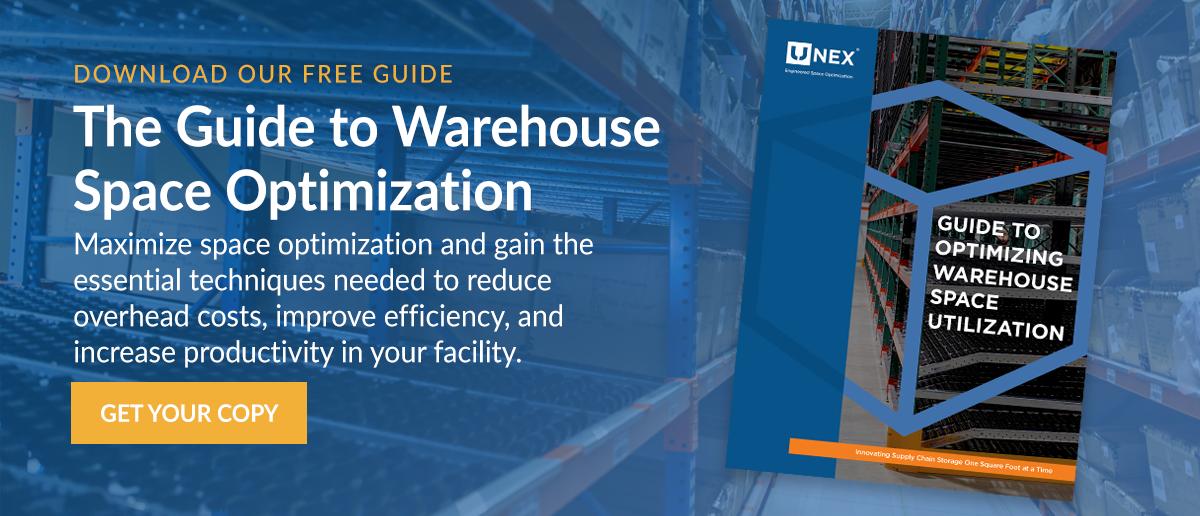