The Benefits of Manual Storage and Picking Solutions in an Automated World
E-commerce has grown and evolved rapidly over the past decade, and warehouse storage and fulfillment operations have had to adapt quickly. For many companies, automated warehouse fulfillment strategies have proven essential to keeping pace with the changes.
In just the past few years, warehouse optimization strategies have shifted toward new technological solutions, such as automated guided vehicles and robots, alongside other software-driven fulfillment methods. Private equity investments in such supply chain technologies surged from $8 billion in 2020 to $20 billion in 2021, and the global warehouse automation market value is expected to grow from $13.6 billion in 2021 to $57.6 billion in 2031, a compound annual growth rate of 15.3%.
As technology pushes warehouse operations forward, some people might assume that manual order-picking systems will soon become a relic of the past. Yet, as vital as warehouse automation is, it can’t solve all of today’s warehouse management challenges alone. In fact, manual warehouse storage and fulfillment solutions are still as crucial as ever for building high-performing, balanced warehouse operations.
Manual vs. Automated Warehousing and Order Picking
Manual warehouse operations come in many forms, depending on the needs of each specific warehouse. In a fully manual setup, workers hand-stock and hand-pick products from static or dynamic storage positions as inventory comes and goes in the warehouse.
This setup depends on strategic warehouse layout and organization to streamline the picking, packing, and shipping process for workers. It may involve methods such as block stacking for slow-moving items or more advanced dynamic storage solutions such as carton flow and pallet flow. Whatever form it takes, the goal is to make it as easy as possible to find products and fulfill orders by hand.
In an automated warehouse, some or all of these stocking and picking tasks are accomplished by some combination of robots and software. Broadly speaking, these are known as automated storage and retrieval systems (AS/RS), but like manual operations, they can take many forms. An operation may blend manual picking with powered conveyors, as in a pick-to-belt system, or it may incorporate fully automated A-frames for fast-paced fulfillment.
Learn how to save space in your facility. Download The Guide To Optimizing Warehouse Space Utilization!
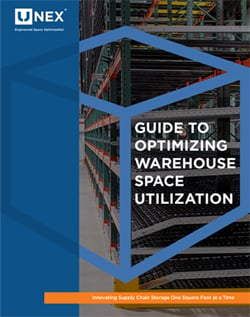
Why Manual Order Picking Remains Critical in Modern Warehousing
For most warehouses — even the fastest-paced operations — the decision about manual vs. automated warehouses isn’t an either-or choice. Automation may prove essential for many aspects of inventory management, but manual order picking still plays a crucial role in fulfillment.
Used properly, manual order-picking systems can deliver a range of benefits:
- Accuracy: Although automation provides more consistent order accuracy at scale, human operators are often still vital for ensuring product quality, verifying order accuracy, and preventing damage.
- Flexibility: Once established, an automated system is difficult to tweak and revise. In contrast, warehouses can easily adapt manual processes and storage systems to changing needs, whether it’s a new client in a 3PL warehouse or a high-volume order season for an omnichannel fulfillment operation.
- Simplicity: Manual processes are often simpler than automated systems, requiring less training and technical expertise. Workers are acutely aware of this — a survey by Harvard Business Review found that 35% of those who expressed hesitation about warehouse automation did so out of fear they would not receive adequate training.
- Versatility: Manual fulfillment systems are better equipped to serve warehouses with diverse product lines. These may include fragile items or ones that customers order infrequently, which are harder to account for within automated workflows.
- Cost Savings: Automation in warehouse logistics requires a substantial upfront investment in equipment and integration. An automated picking system alone may cost between $500,000 and $1 million, requiring several years to see a return on investment. Manual warehouse storage and fulfillment equipment is much less expensive, ROI can be almost instant, and labor costs can be spread out over time.
- Scalability: Because of these costs, scaling a heavily automated operation up and down based on the ebbs and flows of business can be difficult. Manual warehouses, on the other hand, are nimble enough to go with the flow by hiring temporary workers to meet surges in demand.
In most cases, achieving high-performing, efficient warehouse order processing requires an investment in both types of solutions. While automation can help to accelerate growth and enhance warehouse efficiency, manual warehouse operations can complement these technologies by keeping the company flexible, scalable, and in touch with its order fulfillment processes.
Manual Storage and Picking Solutions With UNEX
Complementing automated processes with manual warehouse productivity doesn’t mean relying on outdated or inefficient systems. Finding the right balance and achieving maximum effectiveness requires dynamic storage solutions and reliance on warehouse best practices for order picking.
For instance, UNEX offers a variety of dynamic solutions that will help you ensure efficient, streamlined manual order picking:
- Carton Flow: Carton flow rollers and wheel beds use gravity to bring cartons to the front of the pick face. This enables you to increase storage density without hampering carton access and visibility, simplifying the picking process while maximizing storage space. UNEX SpanTrack rollers and wheel beds drop into existing pallet racks to accommodate a wide range of inventory sizes and weights, whether you need access to full cartons or each picking. SpanTrack can be customized to fit your precise picking needs.
- Dynamic Industrial Shelving: Dynamic shelving creates maximum pick facings to transform an entire pallet rack bay into usable storage space. With columns and cells designed for efficient order picking, workers can access a wider range of products more quickly for more effective manual order fulfillment. UNEX SpeedCell converts existing shelving areas into organized, dynamic picking zones, increasing storage density by 40–60%. With 6 standard column sizes, this high-density shelving can enhance SKU storage for any type of fulfillment operation.
- Pallet Flow: Static pallet shelving requires constant reliance on fork trucks and introduces safety hazards and greater potential for product damage. In contrast, pallet track rollers move full pallets to the front of a pallet rack bay, allowing for increased storage density and safer, more ergonomic picking access. With UNEX Pallet Track, your team can access full-pallet inventory more safely and without a forklift. Tracks and mounts can be tailored to fit your operation and create the ultimate solution for first-in, first-out (FIFO) inventory management.
Optimize Your Warehouse With a Balanced Approach
According to a survey by Modern Materials Handling, 47% of warehouses already use a mix of automated and manual warehouse storage and fulfillment solutions. The two approaches can work together to support a high-performing modern warehouse operation.
Each of the UNEX solutions noted above can be designed to fit the unique needs of your warehouse with minimal upfront investment. Each can be integrated into a robust warehouse automation plan, and all are adaptable to fit your business as it grows and changes. Automation technology will continue to evolve, but manual order-picking systems will always play an indispensable role in order fulfillment.
Does your investment in manual storage solutions match the resources you’ve put into automation? Contact UNEX today to ensure your manual fulfillment operations are set to deliver maximum speed, accuracy, and efficiency.