Implementing Dynamic Storage in an Automated Facility
As automated solutions continue to increase in popularity and availability, supply chain leaders face a tough decision; which solution or combination thereof are a good fit for the needs of my facility? No doubt, automation is reshaping how order fulfillment operations in particular approach warehouse storage. But just like any warehouse storage system, automation is not a one-size-fits-all solution. From the most basic static shelving to more robust dynamic and automated solutions, how can you decide what to use where, and when?
Let’s explore the 3 basic categories of warehouse storage - static, dynamic, and automated. Then we’ll take a deeper dive into how all 3 of these solutions can work together like a dream to create a highly efficient warehouse environment.
Learn how to save space in your facility. Download The Guide To Optimizing Warehouse Space Utilization!
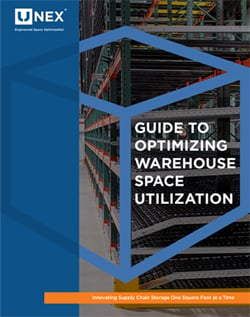
Warehouse Storage Solution Basics
When it comes to warehouse storage, your options are pretty straightforward, but knowing each solution’s strengths (and weaknesses) and viewing them through the lens of your operation’s unique needs is where things get a bit tricky. Every facility is different, so it can be hard to know which combination of storage mediums and what warehouse layout will give you the most efficient facility with the best ROI. In order to understand where and when you might utilize each type of warehouse storage system, it’s important to first understand the key differences among them. Let’s review:
Static Shelving
Static shelves are just that; static. They are fixed in place and do not move. They are typically flat metal or wire shelves that are installed into pallet racking, or they are standalone structures like steel or rivet shelving. To learn more about the most common types of industrial shelving, check out our in-depth article, Top 4 Types of Industrial Shelving.
Static shelving will provide the quickest, easiest, and cheapest setup of the 3 main warehouse storage systems, but it certainly has its limitations. Static shelving is a great starting point for most operations, but as your business grows, you’ll come to realize it's not nearly as efficient as its dynamic and automated counterparts because of its subpar space utilization. However, static shelving is a perfectly good storage solution for some of your slower-moving inventory and/or small quantities of particular SKUs. Static storage is also commonly used for reserve storage on pallets above your main pick locations in a fulfillment operation.
Dynamic Storage
Dynamic storage solutions are designed to be mobile and modular. Dynamic systems often consist of moveable shelving or gravity-fed tracks like carton flow that are designed to save space and time by storing products more efficiently. Unlike static storage systems, dynamic storage allows you to more effectively utilize the space within your racks which, in turn, optimizes the time-saving and efficiency-boosting nature of the equipment.
Dynamic storage is a perfect choice for warehouses and fulfillment centers that need the ability to be extremely flexible. Companies storing a variety of SKUs and that typically face seasonal rushes, fluctuating order rates, and/or quick order churn can benefit from implementing dynamic storage solutions throughout key areas of their warehouse space that are dedicated to order fulfillment. With dynamic storage, you can easily reconfigure product locations and modify storage areas to support the quick and efficient fulfillment of your most popular SKUs.
Automation
Automated storage systems are mostly self-sufficient, powered machines that utilize the latest technology to store and retrieve SKUs, effectively replacing some or all of the human components of an order fulfillment operation. Some automated storage solutions are considered goods-to-person systems where a variety of technologies are working together to bring SKUs from their location directly to an order picker. Others are considered person-to-goods systems where workers have to physically go to the SKU location to retrieve products. This is where dynamic and automated storage systems are quite similar in function.
Some operations that leverage automation for 100% of their order fulfillment processes are considered “dark warehouses.” These fully automated buildings use automated material handling equipment like self-guided forklifts, robotic pickers, and automated sortation systems to pick and move products throughout a facility completely. Since no human interaction is required, these facilities don’t even need to turn the lights on and can completely operate 24/7/365 in the dark, hence their name. This is certainly one way to be efficient, but the average operation is using a combination of static, dynamic, and maybe some automated solutions, all working together in harmony.
Related Reading: Two Ways Manual Solutions Enhance the Benefits of Automation
Knowing When and Where to Use Warehouse Storage Systems
Now that we’ve recapped the 3 main warehouse storage categories, we can address the burning question: when and where do you use static storage vs. dynamic vs. automated?!
At the risk of oversimplifying, it all comes down to throughput. Throughput is the rate of production or the speed at which something is processed. In the warehousing industry, warehouse throughput refers to the number of units processed per time interval. Throughput typically quantifies the outbound operations within a warehouse.
When it comes to selecting the right storage medium, you should first familiarize yourself with your product mix to determine the throughput of your SKUs. Most SKUs fall into 3 zones:
- Low Throughput or Slow-Movers: SKUs that are ordered infrequently that do not need a high-profile position in the warehouse, but still need to be stored in an easily accessible location.
- Medium Throughput or Medium-Movers: SKUs that are picked often and represent the bulk of most operations’ picks.
- High Throughput or Fast-Movers: High-volume SKUs that move so quickly, they may not even need to be removed from their original pallet. These SKUs typically represent the bulk of the revenue stream in a facility.
It’s best to store low-throughput SKUs in static shelving, tilted pick shelving, or high-density shelving. High-density shelving can be dynamic or automated, but most people find dynamic high-density storage like UNEX SpeedCell to be the true sweet spot for these SKUs as it provides significant space-saving over static storage but is dramatically more cost-effective compared to automated storage systems. In this case, dynamic storage is also easier to manage and requires far less maintenance than an automated system.
For medium-throughput SKUs, carton flow solutions, like SpanTrack Lane and SpanTrack Wheel Bed, are the ideal solution. Once again, dynamic storage will be far more efficient than static shelving because it can use more space within your pallet racking. And since these SKUs are typically the ones your team will handle the most, it's important to consider a storage solution that is space efficient. When you store more SKUs in less space, you reduce the time employees need to travel to each SKU location. You’ll save time and money when you actively work to reduce the overall footprint of your order picking operation.
In most cases, high-throughput SKUs shouldn‘t be removed from the pallet they arrived on. Your highest throughput SKUs should be placed on a pitched conveying surface, like UNEX dynamic Pallet Track, for the most efficiency. If you are storing and moving full pallet loads and have the budget, you may consider an automated storage and retrieval system (AS/RS) for this part of your operation. A unit-load AS/RS is a large system that is designed to store and pick full pallet loads. But again, investing in this type of system will require much consideration due to its high cost and higher maintenance requirements.
To gain an in-depth perspective on slotting your SKUs according to throughput, download our expert-backed guide, Understanding Throughput for Fulfillment!
UNEX Warehouse Storage Experts Can Help
As you can see, there is a lot to consider when it comes to warehouse storage! While static shelves are a basic, quick, and cost-effective option, dynamic and automated storage systems reign supreme when it comes to saving space (ie: most efficient, biggest ROI). Most dynamic and automated systems can solve the same challenges all operations face:
- Inefficiency, low accuracy, mispicks
- Running out of storage space
- Increasing labor costs
So how do you decide between dynamic and automated systems? Maybe you don’t have to!
We asked our Northeast Regional Sales Manager, Dan Teese to help us better understand when and where it makes sense to implement dynamic storage systems in automated facilities or in conjunction with automation. Over his nearly 10 years in the business, Dan has seen it all! His experience has shown him that most facilities store products that may not warrant the investment for automation, or it is physically impossible for them to achieve a healthy ROI with automation. But that doesn’t mean they don’t use it at all!
There’s a place for everything and everything in its place. “Slower moving SKUs or oddball items are typically not a great fit for storing in automated systems,” Dan explained. “Likewise, items that are being picked out of master cartons or totes that may not be easily handled by an automated solution will be better off stored in a dynamic system like carton flow or dynamic industrial shelving,” he added.
We then asked Dan to really break it down for us. Here’s what he had to say:
“Automation is an expensive investment. For your slower-moving each picks, where every pick of a particular SKU may be of a different quantity, the investment into automation is probably not warranted. Not all picks are the same, and not all products have the same throughput. Because of this, you want to make sure your storage system does not slow down the picking process, and assigning the wrong solution could very well do this. Your products and the throughput of your SKUs can change throughout the year. Having the flexibility to adjust to those changes quickly is very important. Some automation requires a lot of changes (read: costs) in order to have this flexibility. Warehouses can quickly adjust dynamic storage solutions like SpeedCell dynamic industrial shelving and SpanTrack carton flow to fit the needs of changing product lines or throughputs.”
WOW. Thanks, Dan!
As we're learning, and many supply chain leaders are finding out, automation may be flashy, but it has limitations. So how does dynamic storage fill in the gaps where automation can't?
- Cost
- Flexibility
- Scalability
- Less maintenance
- Ease of use/less training required
Dan was able to share some more insight into specific projects he has worked on by adding, “Some of the larger projects I have done were ones where SpeedCell was the preferred solution over automation. The reason these facilities went with SpeedCell was its lower cost, flexibility to scale and change locations easily, and quick ROI. A lot of the smaller projects I have done are where they put a few bays of SpeedCell at the end of a carton flow or static storage area, and they used more automated solutions when it came to powered conveyors and pallet storage.” This is a great example of you might leverage dynamic solutions to fill in the gaps where automation can’t, while still utilizing all 3 of the core warehouse storage systems to play to their unique strengths. Finding the right mix of storage mediums that will work together strategically throughout your facility is the key to success!
Connect with Dan on LinkedIn to stay up-to-date on the latest warehouse storage trends and solutions!
Work with the Warehouse Storage Experts at UNEX
We shared a lot of great foundational information in this article, but if you’re still feeling overwhelmed or simply want to know the exact right combination of solutions that will work best for your operation’s unique needs, UNEX can help. Our team of experts like Dan can work with our distributor partners local to your area to develop a complete solution for the unique needs of your business. Whether that total solution includes static shelving and dynamic storage, or automated systems working in conjunction with dynamic UNEX solutions, our combined years of experience with partners across the country will lead you to develop the perfect warehouse storage plan for your operation. Plus, we offer free engineering support on all our projects to ensure your UNEX solutions are tailored specifically to your unique situation. Contact us today to get started on your next project!