The Importance of 5S Lean Manufacturing

Key Takeaways
- 5S is a foundational lean methodology that improves productivity and reduces waste through better organization, cleanliness, and standardized workflows.
- Each pillar of 5S plays a crucial role in creating safer and more efficient manufacturing environments.
- UNEX products such as FlowCell, Roller Rack, SpanTrack, and Pick Shelves support 5S by enhancing organization, improving access, and enabling long-term lean success.
Many manufacturing facilities have opted to follow the path towards a 5S lean manufacturing system as part of a continuous improvement program or lean manufacturing process. The 5S system is part of Toyota’s Lean Manufacturing methodology designed to reduce waste within your facility.
How Important Is 5S?
The 5S methodology is typically the first step towards in eliminating waste from manufacturing processes and eventually leads to improving bottom-line results. There are five pillars in 5S, which stand for: Sort, Set in Order, Shine, Standardize, and Sustain. The goal of a 5S program is to get products closer to operations and workers, organized and labeled to eliminate wasted time and materials.
The 5S philosophy is "a place for everything and everything in its place," is a mantra of UNEX. We help you find the right space optimization solution that eliminates wasted time, underutilized space, and lost inventory.
The result of a 5S lean manufacturing implementation is a significant reduction in space needed for existing operations. Workers improve their workspaces by cleaning and organizing them.
Tools and materials are labeled and stored in organized storage locations. Shelving and racks optimize the storage of items in a smaller footprint, helping to improve the order picking process by eliminating the need to search for things.
The 5 Pillars of 5S Lean Manufacturing
Implementing 5S creates a foundation for continuous improvement in manufacturing environments. Each pillar contributes to a more efficient, organized, and productive workspace, helping teams reduce waste and maximize value. Here’s how each step applies in practice:
1. Sort
Remove all items not needed, leaving only the bare essentials. Sorting saves time, space, and labor costs while enhancing productivity.
2. Set in Order
Arrange items, so they are easy to use; label items so anyone can find them or put them back in the right location. Arranging eliminates wasted time from excess motion and searching.
3. Shine
Keep everything clean every day. Daily cleaning keeps things ready to be used when needed.
4. Standardize
Ensure conditions of work area do not return to the original, disorganized state.
5. Sustain
Make a habit of properly maintaining correct procedures to avoid backsliding.
Learn lean manufacturing storage principles. Download the Lean Manufacturing Storage Guidebook!
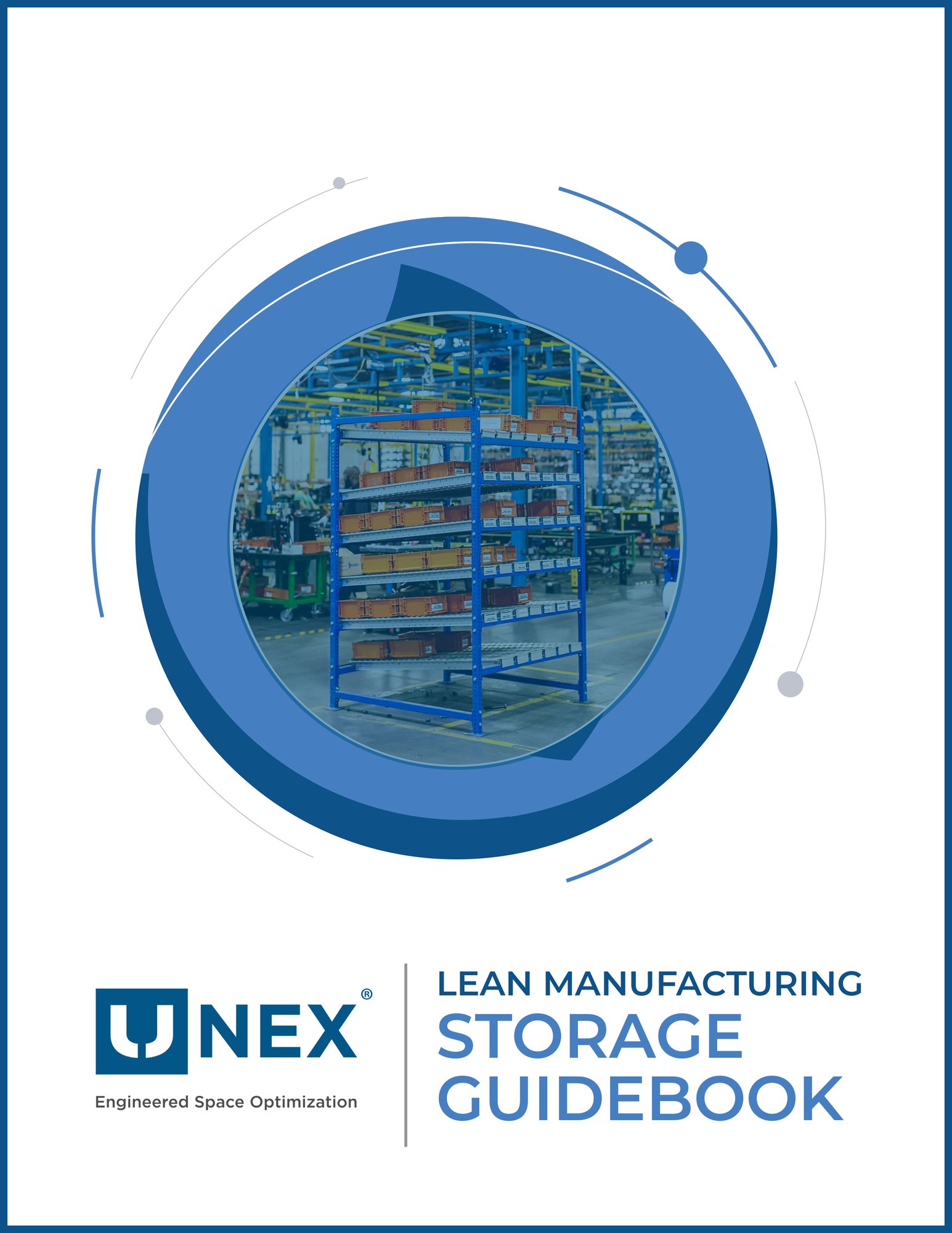
UNEX Solutions That Support 5S Lean Manufacturing
A well-executed 5S program requires more than commitment—it demands tools and systems that make organization, efficiency, and consistency part of everyday operations. UNEX provides a range of products specifically designed to solve the challenges identified in 5S initiatives, helping manufacturers eliminate waste, reclaim space, and improve workflow visibility.
FlowCell
FlowCell is a standout solution for organizing materials and tools directly at the point of use. These modular workstations support the "Sort" and "Set in Order" pillars by creating designated storage areas that separate essential items from unnecessary clutter. The ergonomic design and reconfigurability of FlowCell make them ideal for maintaining clean, organized workspaces that adapt to continuous improvement efforts.
Roller Rack
Roller Rack addresses the need for visual organization and flow. Built as standalone units with integrated SpanTrack lanes, they make it easy to assign specific locations for parts and components, supporting efforts to reduce search time and reinforce a place-for-everything mindset. Roller Racks are especially effective in high-activity areas where clear labeling and consistent layout are critical to sustaining progress.
SpanTrack
SpanTrack carton flow transforms standard pallet racking into dynamic, high-performance storage systems. These drop-in tracks ensure consistent FIFO inventory rotation and streamline picking processes, aligning with the "Standardize" and "Sustain" pillars of 5S. Their easy integration and adjustability allow facilities to maintain orderly workflows while reducing product damage and excessive motion.
Pick Shelves
For smaller parts and precision picking applications, UNEX Pick Shelves offer a clean, accessible solution. Their angled design improves visibility and reach, helping teams implement daily cleaning and maintenance practices outlined in the "Shine" phase. By making every item easy to see and access, pick shelves reduce errors and support a safer, more efficient workplace.
Implementing 5S Lean Manufacturing With UNEX
Implementing 5S raises product quality and improves worker productivity, resulting in lower costs and higher efficiencies. UNEX is laser-focused on helping clients improve their manufacturing processes with lean principles. Our 5S storage solutions, like Flow Cell, minimize waste while increasing efficiencies.
UNEX specializes in designing engineered space-saving solutions serving several industries, including distribution, logistics, retail, and manufacturing. To learn more about how UNEX can help implement 5S lean manufacturing, boost productivity, and eliminate waste within your operation, contact us today.