Understanding Supply Chain Warehouse Storage Systems: Static, Dynamic, and Automated Solutions
When it comes to warehouse design and order fulfillment, selecting the right storage system is essential to ensuring efficiency, cost-effectiveness, and scalability. As supply chains grow in complexity and demand for faster deliveries intensifies, warehouses must adapt their storage solutions to meet these challenges. Understanding the different types of storage systems—static, dynamic, and automated—can help warehouse managers make informed decisions about how best to optimize their operations.
In this article, we’ll explore each storage system's key features, examples, pros, and cons, offering insights on which solution might be best suited for your specific needs.
Static Storage Systems
Static storage, also known as fixed storage, involves assigning specific storage locations to products. These systems are most effective in environments with a limited number of SKUs, stable inventory, and low turnover. Static storage is the most traditional form of warehouse storage and is typically easy to implement and manage.
Examples of Static Storage:
- Static Shelf or Rack Storage: Static shelves and racks store products in designated, unchanging locations. Common in small warehouses, retail environments, or environments with lower SKU variety, shelf storage is straightforward to set up and easy for workers to navigate.
- Pallet Racking Systems: Ideal for bulk storage, pallet racking systems are widely used in larger warehouses, especially those storing heavy or large items. Pallets are placed in fixed locations, and each item has a designated spot. These systems are simple and reliable for operations that require minimal inventory movement.
- Bin Storage: Bins are used for small or varied products. In warehouses handling small parts or hardware, bin storage allows for quick access and organization. Each bin is assigned a specific location to keep items easily identifiable and accessible.
Pros of Static Storage:
- Simple and easy to manage: Static systems require little technology and are straightforward for warehouse workers.
- Low setup cost: They are relatively inexpensive to implement and maintain.
Cons of Static Storage:
- Inefficient space utilization: Static systems may not maximize available space, especially in high-demand environments.
- Lack of flexibility: This system can struggle to handle fluctuations in demand or a large number of SKUs, leading to wasted space or inefficient picking.
Dynamic Storage Systems
Dynamic storage systems offer more flexibility than static systems. In a dynamic storage setup, products are stored in available spaces, and the system adapts to fluctuating inventory levels. This approach is beneficial in environments with high SKU counts, fast-moving inventory, and changing demand—like most warehousing and fulfillment operations in the current supply chain landscape. Dynamic storage often relies on real-time tracking systems (such as warehouse management systems, or WMS) to ensure accurate inventory control.
Examples of Dynamic Storage:
- Flow Racks (FIFO storage): Flow racks use gravity to push products toward the picking area. This system is most beneficial for perishable goods or items that need to be picked on a first-in, first-out (FIFO) basis. For example, food distribution centers may use flow racks to ensure that older products are picked first, minimizing waste.
- Carton Flow: Carton flow systems use inclined shelves with rollers or wheel beds, allowing cartons to roll forward as items are picked. This setup facilitates efficient picking in FIFO order and is commonly used in distribution centers dealing with fast-moving consumer goods. It’s an excellent solution when quick access and medium to high throughput are required.
- High-Density Storage Systems: Dynamic high-density storage systems maximize space and create compact storage, increasing capacity without expanding the warehouse footprint. Systems like Drive-In/Drive-Through Racking, Push-Back Racking, and dynamic industrial shelving systems like UNEX SpeedCell are designed to store goods more densely, making them ideal for a wide variety of SKUs and products with lower picking frequency. These systems store products compactly, increasing the number of items stored per square foot, improving overall space efficiency, and reducing the need for costly expansions.
Pros of Dynamic Storage:
- Maximizes space utilization: Dynamic systems are more efficient at using available space than static systems, especially when handling fluctuating inventory.
- Adaptability: These systems are ideal for handling high SKU counts and changes in demand.
- Faster picking: With systems like flow racks or carton flow, items are easy to retrieve in an organized manner, improving picking speed.
- High-density storage: High-density systems like UNEX SpeedCell, drive-in racking, or push-back allow for more goods to be stored in a smaller area, increasing storage capacity without additional space costs.
Cons of Dynamic Storage:
- Requires sophisticated tracking: Dynamic systems rely heavily on warehouse management software (WMS) to track inventory, making them more complex to set up and manage.
- Longer picking times (if you’re not doing it right!): Poorly optimized systems may require additional time for workers to locate items.
Automated Storage Systems
Automated storage systems integrate advanced technology to optimize space, improve speed, and reduce labor costs. These systems use robotics, powered conveyors, and computer-controlled machines to store, retrieve, and move products without human intervention. While they typically require significant upfront investment, automated systems offer long-term benefits, especially for high-volume, fast-paced environments.
Examples of Automated Storage:
- Automated Storage and Retrieval Systems (ASRS): ASRS solutions use cranes, shuttles, or robots to store and retrieve items automatically. These systems are common in large-scale operations, such as automotive parts warehouses, where high-density storage and fast retrieval are essential. ASRS can significantly enhance efficiency by reducing the need for manual labor and optimizing space.
- Robotic Mobile Storage: Robotic mobile systems use autonomous robots to transport shelves or bins to workers for order picking. This eliminates the need for workers to travel to pick items, reducing picking time and improving warehouse productivity. For example, Amazon’s fulfillment centers rely on this system to speed up operations.
- Vertical Lift Modules (VLM): Vertical lift modules store goods vertically, using automated elevators to retrieve items from different levels. VLM systems are space-efficient and often store small parts or high-value items. They are widely used to optimize storage and retrieval times for high-ticket or sensitive items in industries such as pharmaceuticals or electronics.
Pros of Automated Storage:
- Highly efficient: Automated systems significantly reduce labor costs while improving speed and accuracy, especially in high-throughput environments.
- Space optimization: Systems like ASRS and VLM maximize vertical storage, making better use of available space.
- Scalable and adaptable: Automated systems can scale to meet growing demands without major changes to the infrastructure.
Cons of Automated Storage:
- High initial cost: The setup for automated systems can be expensive, especially when incorporating robotics.
- Technical complexity: Automated systems require maintenance, and failures can disrupt warehouse operations.
- Limited flexibility: Automated systems are often less adaptable to changing inventory or layout needs than dynamic storage systems.
Choosing the Right Storage System for Your Warehouse
Each storage system has its own strengths and is suited to specific operational needs. When deciding on a storage solution, consider the following factors:
- Inventory Complexity: If your warehouse handles a large variety of SKUs or fluctuating inventory, dynamic or automated systems (or a combination of both) may offer the flexibility needed for quick adaptations. On the other hand, static storage may suffice if you have a more stable inventory or a smaller operation.
- Order Volume and Throughput: High-volume operations with fast-moving inventory often benefit from automated or dynamic systems that can speed up picking and reduce labor costs. Systems like ASRS or robotic mobile storage can help boost efficiency in these environments.
- Space Utilization: Automated systems and dynamic storage are more effective at utilizing available space than static systems. If space optimization is a key concern, consider solutions like ASRS, which maximizes vertical storage, and carton flow, which improves throughput and accessibility.
- Budget: While automated systems provide significant efficiency gains, they come with higher initial setup costs. Static and dynamic storage systems are typically more cost-effective, but static storage systems do not offer the same long-term scalability.
Learn how to save space in your facility. Download The Guide To Optimizing Warehouse Space Utilization!
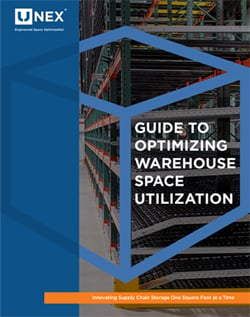
UNEX Dynamic Storage Solutions
UNEX dynamic storage solutions are designed to help warehouses unlock their full potential by maximizing space, improving picking efficiency, and reducing operational costs. Unlike basic static storage systems or costly automated storage systems, UNEX solutions offer flexibility, scalability, and cost-effectiveness. They make it easier to adapt to changing inventory needs and increase order volumes while maintaining healthier profit margins. Let’s explore four key UNEX solutions that can help you increase efficiency in your warehousing and order fulfillment operations.
UNEX SpanTrack Carton Flow
Compared to static storage systems, which allocate fixed storage locations, SpanTrack offers greater flexibility and faster picking, especially for smaller items or orders with high turnover. Unlike automated systems, it doesn’t require significant upfront investment or complex maintenance, offering a cost-effective solution with low upkeep.
SpanTrack Carton Flow offers:
- Optimized FIFO (First-In, First-Out) picking: SpanTrack uses inclined rollers and wheel beds that allow cartons to flow naturally to the pick face, ensuring the oldest items are picked first. This reduces waste and expiration risk.
- Flexibility and scalability: SpanTrack’s modular design allows easy adjustments to accommodate different carton sizes and changing inventory needs, making it adaptable to fluctuating demand.
- Increased storage density: SpanTrack maximizes vertical space and helps store more goods in less floor space, increasing storage capacity and improving space utilization.
UNEX FlowCell Flow Racks
Unlike static storage systems that are fixed in place, FlowCell flow racks offer modular, dynamic storage that can be reconfigured as your needs change. These durable, portable flow racks maximize pick efficiency and streamline workflows. Compared to automated systems, FlowCell racks provide fast access to items without the complexity or high costs of robotics or powered conveyors, making them ideal for mid-sized operations seeking efficiency without massive investments.
FlowCell Flow Racks Offer:
- Customizable configuration: FlowCell flow racks are designed to store a wide range of items, with adjustable dividers, shelves, and angles that can be configured to specific needs.
- Increased picking speed: Items flow to the picking area with gravity assistance, reducing the time workers spend traveling through aisles and improving order fulfillment speeds.
- Improved ergonomics: Flow racks minimize the need for bending or reaching, reducing strain on workers and enhancing overall productivity.
UNEX SpeedCell Dynamic High-Density Storage
SpeedCell provides far more efficient use of space than static storage systems, which often create dead zones in shelving and leave unused gaps in aisles. Unlike automated systems, SpeedCell is low-maintenance and affordable while still offering high-density storage and easy scalability, making it an ideal solution for businesses looking to optimize warehouse space without the high upfront cost of full automation.
SpeedCell High-Density Storage offers:
- Maximized vertical space: SpeedCell increases storage density by utilizing vertical storage space and can handle a wide variety of product sizes, from small parts to bulkier items.
- Increased storage density: SpeedCell can compress 200’ of rack or shelving into 40’ of highly organized space.
- Increased picking efficiency: The system allows easy access to stored items by organizing products into compact storage cells, significantly improving picking times.
UNEX Pallet Track Pallet Flow Systems
Pallet Track provides greater space utilization compared to static pallet storage, which flows pallets along wheel rails or rollers. Unlike automated systems, Pallet Track requires no complex robotics or controls, offering a simple yet effective solution to increase efficiency and space utilization without significant capital investment or ongoing maintenance costs.
Pallet Track Pallet Flow offers:
- FIFO pallet storage: Pallet Track uses gravity-fed roller systems to ensure that pallets are always picked in the proper order (first-in, first-out), reducing inventory errors and waste.
- Increased throughput: This pallet flow system improves throughput by reducing time spent searching for items and ensuring products are quickly accessible.
- Space-efficiency: By storing pallets in a compact, high-density configuration, Pallet Track utilizes available floor space more efficiently, allowing businesses to store more items in less space.
These UNEX dynamic storage systems are designed to offer significant benefits over traditional static storage, providing greater flexibility, space efficiency, and speed. In comparison to automated systems, they strike the perfect balance between cost, ease of implementation, and long-term scalability, making them an excellent choice for businesses looking to optimize their supply chain operations.
Maximize Space, Boost Efficiency, and Save Money When You Choose UNEX
As the demand for faster, more efficient order fulfillment continues to grow, choosing the right storage system is essential for maintaining a competitive advantage. Whether opting for the simplicity of static storage, the flexibility of dynamic systems, or the cutting-edge efficiency of automated solutions, understanding your warehouse's specific needs will help guide the right decision. By leveraging the right storage systems, businesses can optimize their supply chain operations, reduce costs, and improve overall efficiency.
At UNEX Manufacturing, our dynamic storage solutions are designed to help warehouses and order fulfillment operations maximize space, increase efficiency, and reduce labor costs. By offering flexible and high-density systems like carton flow, dynamic high-density storage, flow racks, and pallet flow systems, we enable businesses to optimize storage capacity and streamline their picking processes. Our solutions not only improve overall warehouse productivity but also help reduce operational costs, making them a smart investment for businesses looking to enhance their supply chain performance. With innovative storage solutions from UNEX, companies can save money, improve throughput, and stay competitive in today’s fast-paced environment. Contact us today to get started on your path to improved operational efficiency!