5 Common Flow Rack Implementation Mistakes that Impede Performance
Today’s warehouse managers are constantly looking for ways to run a more efficient operation. After all, ineffective operations negatively impact the business’s bottom line, customer satisfaction, workplace safety, and more. Fortunately, there are numerous storage systems warehouses can leverage to streamline their operations, such as industrial flow racks.
Flow racks are a high-density storage system that can be implemented into warehousing operations to increase space utilization and create FIFO product rotation. While they are a warehouse staple, flow racks can be deceptively complex to order and install. With a variety of styles and sizes on the market, determining the correct fit for your operation can be a challenge.
Mistakes in Flow Rack Implementation
The successful implementation of flow racks requires careful planning and consideration. Mistakes in the selection, installation, and configuration of these systems can severely impede performance and operational efficiency. Here are the five most common mistakes in flow rack implementation and how to avoid them to ensure your warehouse operates at peak efficiency.
1. Choosing the Wrong Style Track
Selecting the appropriate style of track for your flow rack system is crucial for optimizing efficiency. The two primary styles of tracks used in flow rack systems are dedicated lane tracks and universal bed tracks, each with different features ideal for specific applications.
- Dedicated Lane Tracks: These tracks utilize carton flow rollers and are ideal for operations with predictable box sizes. They are particularly effective for storing items like shoes, liquor, or apparel, where the dimensions of the boxes remain consistent. The dedicated lanes ensure that each box type flows smoothly and is easily accessible.
- Universal Bed Tracks: In contrast, universal bed carton flow tracks are designed for flexibility, making them suitable for handling a variety of box sizes. This style is perfect for scenarios where box sizes are unpredictable, such as closeout merchandising or operations dealing with imported goods where packaging varies. Universal bed tracks are also advantageous for highly seasonal businesses that frequently re-slot SKUs based on throughput, as they can adapt to different product types effortlessly.
In addition to these track styles, some older styles, such as plastic wheel rails, are still in use. While plastic wheel rails can manage lightweight products with specific dimensions, utilizing this style of track comes with several limitations. Plastic wheel rails aren't as durable or efficient as dedicated lane or universal bed tracks. These older systems often lead to hang-ups and reduced flow efficiency.
Choosing the wrong style of track for your operation can lead to inefficient workflows and wasted space. For instance, using dedicated lane tracks in an environment with unpredictable box sizes can result in reduced storage effectiveness. This misalignment not only hampers productivity but also affects the bottom line by preventing optimal use of available space.
2. Choosing the Wrong Track Width
Choosing the correct track width is essential to maintaining operational efficiency and maximizing space utilization. Choosing the wrong width can lead to several issues that hinder productivity and waste valuable space.
- Operational Inefficiencies: Incorrect track width can prevent workers from placing SKUs in the optimal location, leading to inefficiencies in the picking process. If the track width is too wide for the SKU, it creates gaps and makes it difficult for workers to pick items quickly and safely. Conversely, if the track width is too narrow, it can cause products to jam or not fit properly.
- Wasted Space: When SKUs are undersized compared to the track they are in, it results in wasted horizontal space. This not only reduces the overall storage capacity but also makes the storage system less efficient.
Typically, lanes work better when they are slightly undersized compared to box width. Tracks sized in this manner are easier to pick from because workers can easily and safely slide their hands underneath and it doesn’t waste horizontal space.
To avoid the mistake of choosing the wrong track width, consider the following:
- For Uniform Width Items: If the items you are storing are the same width, SpanTrack Lane carton flow rollers will be your most efficient and cost-effective option. This setup ensures that each box type flows smoothly and is easily accessible.
- For Varied Width Items: If the items you are storing vary in width or you have a need for frequent reslotting, SpanTrack Wheel Bed, commonly known as carton flow beds, will provide maximum efficiency and flexibility. This system allows for easy re-slotting and adaptation to different product sizes without the need to move tracks.
Learn to optimize warehouse space for increased speed and accuracy. Download the Guide to Understanding Throughput for Fulfillment!
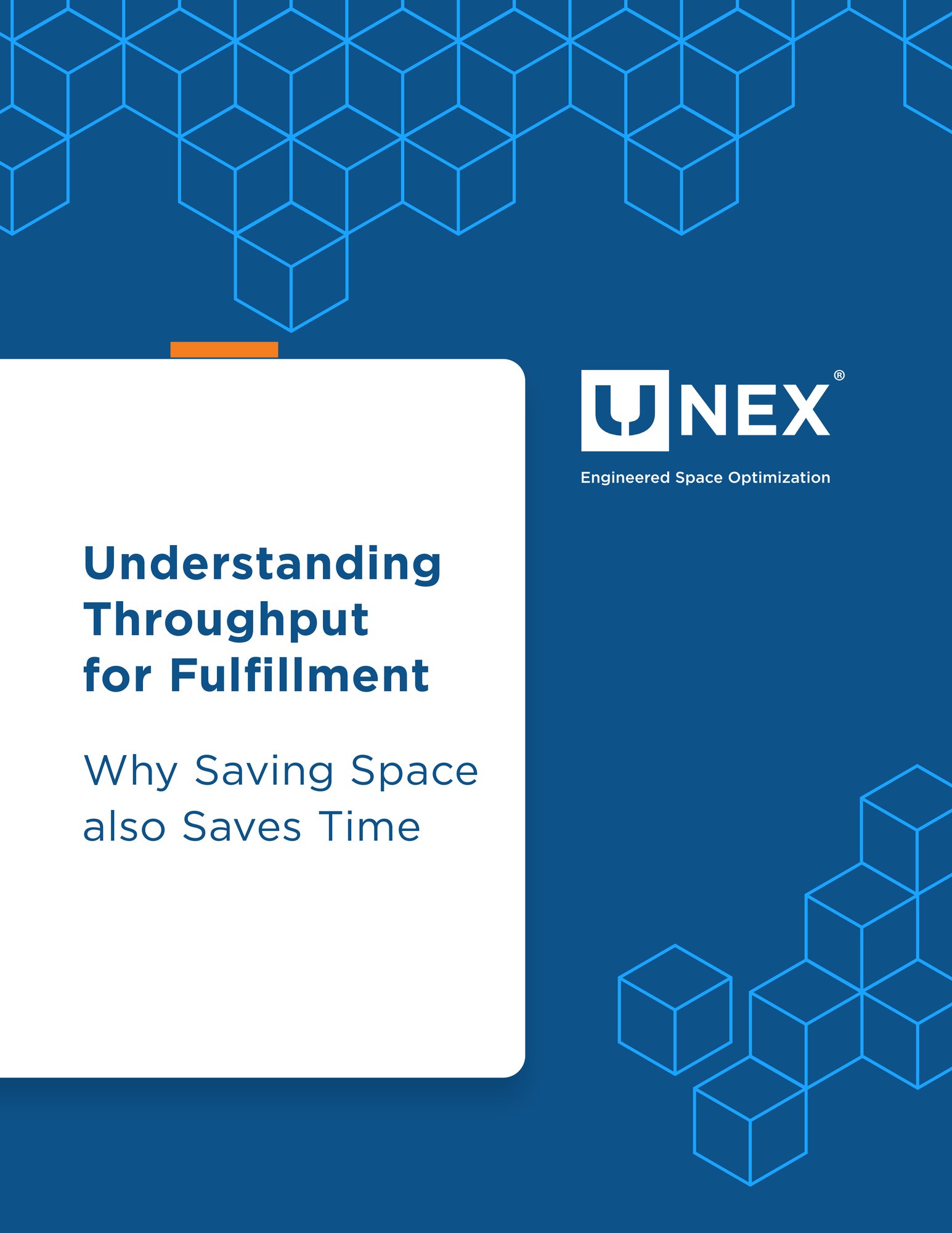
3. Choosing the Wrong Lane Depth
Ensuring that the depth of the track aligns with what you’re storing is a critical factor that is often overlooked. Selecting the wrong lane depth can lead to several inefficiencies and increased operational costs.
If the flow rack is too shallow, it may require more frequent replenishment, consuming valuable time and resources, reducing overall productivity, and increasing labor costs. Conversely, a flow rack that is too deep wastes vital floor space by storing more inventory than necessary for the required throughput. Overloaded racks can lead to higher carrying costs due to excess inventory and increased handling and operational costs. Additionally, if the lane depth is too great for the average inventory levels, the racks will remain partially empty most of the time, resulting in wasted capacity and inefficiency.
To avoid these pitfalls, assess your inventory turnover rate and align the lane depth with your throughput requirements. High-turnover items may benefit from shallower lanes for quick replenishment, while lower-turnover items might need deeper lanes to reduce restocking frequency. Also, consider the size and weight of the products being stored. Larger or heavier items may need deeper lanes to accommodate their dimensions, while smaller items can be stored in shallower lanes for maximum picking efficiency.
4. Not Optimizing Space between SKUs
Many warehouses overlook how much space is between their SKUs — but does this even matter? Yes! Spacing SKUs is another key consideration to make when implementing a flow rack.
The optimal spacing between boxes is approximately 2”. This spacing helps maximize horizontal storage, ensuring there is enough space for workers to pick boxes up from their sides. This is important because if boxes are too close, they’re hard to pick. On the other hand, if boxes are too far apart, this wastes valuable horizontal space.
To avoid wasted space and facilitate easy inventory access, always maintain appropriate spacing between SKUs in your flow rack system.
5. Incorrectly Sizing Beams
Incorrectly sizing beams is another implementation mistake that’s easy to make. Occasionally, facilities need to repurpose existing pallet rack structures where the beams may be sized for heavier loads. However, these taller beams may take up valuable vertical space. For example, if your inventory only takes up half the vertical space on each storage level, that creates lots of wasted space that could be reconfigured.
In order to ensure warehouse space optimization, confirm the beams are properly sized for the anticipated load. This tip alone could be the difference between three, four, or even five storage levels, which could yield a 20-30% increase in storage density.
Operational Efficiency with UNEX Flow Racks
When properly planned and installed, industrial flow racks can help increase space utilization by up to 50% without expanding the existing footprint of your storage area. At UNEX, we help warehouses realize this space utilization potential with our customizable flow rack systems. Designed to maximize space, tidy messy pick areas, and improve inventory organization, let’s take a look at how these dynamic storage solutions improve warehouse operations and overall efficiency:
FlowCell
UNEX FlowCell is a modular, dynamic storage system designed specifically for a facility’s unique operation. These durable and flexible storage units support Lean principles by keeping inventory organized and maximizing pick efficiency. Here are just a few of the many FlowCell benefits:
- Accelerates Productivity: Boosts production efficiency up to 30% by angling parts toward the worker, creating an efficient and accessible pick point.
- Improves Ergonomics: Minimizes reaching and improves ergonomics, reducing worker injury and fatigue.
- Enables Versatility: FlowCell’s portable design accommodates line and process changes with flexible, easy-to-reconfigure storage.
Warehouses can rely on FlowCell for years because it’s backed by a 7-year warranty. Plus, FlowCell is 13 times stronger than the average tube and joint modular structure, supporting up to 1,000 pounds per level because of its heavy-gauge steel construction.
Roller Rack
UNEX Roller Rack provides seamless carton flow to help warehouses maximize efficiency. These pre-engineered gravity flow racks are designed to optimize efficiency, safety, and FIFO rotation. They’re ideal for operations where carton flow is required, and there is no need to store pallets above the rack. Discover the benefits of Roller Rack:
- Easy to Install: These durable flow rack structures are pre-configured, making them quick and easy to build. Roller Rack’s modular design allows for maximum flexibility to create standalone carton flow units or add units to create bays of carton flow.
- Reduces Worker Strain: Adjustable pick trays and knuckle track positions improve access and visibility, reducing worker strain.
- Creates Dense Storage: SKU storage is up to 7 times more dense per bay than pallet position storage, which means up to 80% less travel time for pickers.
Roller Rack’s modular design allows you to easily scale storage capacity up or down by adding or removing rack sections as needed. Racks can also be reconfigured with various carton flow lane styles to accommodate your changing inventory needs.
Optimize Your Flow Rack System with UNEX
Avoiding these common implementation mistakes is important when determining the flow rack solution that’s best suited for your space. After all, every warehouse footprint and operational objective is different. That’s why creating a comprehensive plan is one of the most important steps to take before purchasing a flow rack system.
Instead of an off-the-shelf storage solution that may, or may not, fit your unique operational needs, consider a customized flow rack solution that is designed for your warehouse’s unique footprint and product offering. Not sure what type of flow rack you need to be successful and make the most out of your space?
Contact us to get in touch with a UNEX product expert. They will help you choose the right storage solutions to take your business to the next level.