Top 7 Warehouse Management Challenges and How to Overcome Them
Key Takeaways
- Inefficiencies in space utilization, picking, and ergonomics drive up labor costs, errors, and operational bottlenecks in warehouse management.
- Solving these challenges requires dynamic, scalable storage solutions that improve organization, throughput, and worker safety.
- UNEX solutions like SpanTrack, SpeedCell, FlowCell, and Gravity Conveyor address space constraints, picking inefficiencies, and product damage while supporting warehouse scalability.
Warehouse management plays an essential role in the success of businesses across the supply chains. Effective warehouse management helps increase operational efficiency, while reducing costs and boosting overall customer satisfaction. But managing a warehouse isn’t easy or simple, especially with an unpredictable supply chain. Challenges are certain to pop up, and it’s essential to identify and solve them to prevent negative consequences that may impact your customers, employees, and overall business.
In this article we will outline seven of the most common warehouse challenges and we’ll suggest the best UNEX solutions to help address them.
7 Warehouse Management Challenges
Challenge 1: Space Utilization
Warehouse space is more valuable than ever. But many of today’s warehouses store thousands of SKUs and don’t have effective storage systems in place to optimize their existing space. Static storage systems can create a congested warehouse with blocked aisles and disorganized SKUs, resulting in low pick rates and delayed shipments.
Challenge 2: Inventory Management
Whether your warehouse struggles with having too much or too little inventory — or even disorganized or spoiled inventory — you’re not alone. Inventory management problems are common and costly, but a disorganized warehouse can lead to lost items, delayed order fulfillment, stock shortages, safety hazards, and more.
Challenge 3: Order Picking Efficiency
Inefficient order picking processes can quickly snowball into multiple challenges affecting your employees, customers, and bottom line. Here’s how your warehouse picking processes and strategies impact:
- Worker productivity: Inefficient pick paths can increase travel time and slow worker productivity. Tired employees may accidentally pick the wrong items or hurt themselves on the job, leading to high turnover rates.
- Customer satisfaction: Inefficient order picking can cause delayed orders and incorrect shipments, negatively impacting customer satisfaction.
- Business profitability: Reduced throughput and high occurrences of order picking errors eventually impact business profitability. It is costly for warehouses to restock incorrect orders and even costlier to lose customers.
Challenge 4: Product Damage
Is your warehouse losing money on inventory before it’s even shipped to the customer? Poor organization and inadequate storage solutions may cause damage when the item is stored or handled. For example, inventory could be crushed when shelves are overloaded or items aren’t properly stored.
Challenge 5: Labor Costs
If labor costs are becoming a significant expense for your warehouse, they may be caused by inefficient processes and excessive manual handling. Order picking is one of the most labor-intensive processes in any warehouse, and it may be contributing to your high labor costs. If workers spend a lot of time traveling from SKU to SKU or searching for items, these inefficiencies can quickly add up over time.
Challenge 6: Ergonomics
Is your warehouse struggling with high levels of employee turnover or worker injuries? Poor ergonomics may be to blame. This problem impacts warehouse workers in many ways, from decreasing their productivity to causing injuries on the job. When items — especially heavy objects — are out of easy reach, workers may need to reach or bend in awkward positions to pick them. These strained movements may cause workers to accidentally strain a muscle or experience discomfort over time.
Challenge 7: Scalability and Flexibility
In today’s ever-changing supply chain landscape, many warehouses need the ability to quickly scale and change their operations. Whether you’re experiencing seasonal demand or a certain product line is quickly expanding, you need the ability to accommodate warehouse growth.
Learn how SpeedCell helped Goodwill of Central & Southern Indiana boost efficiency and storage capacity. Download the Case Study.
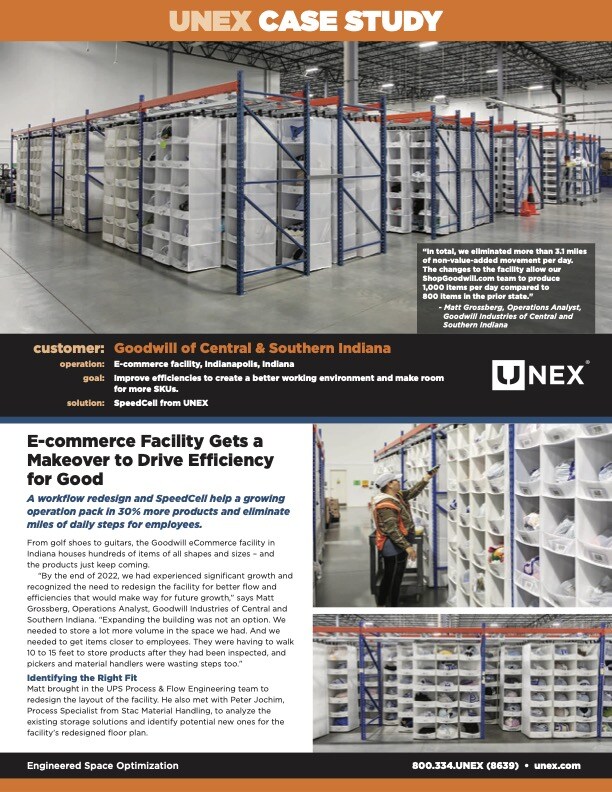
How UNEX Solutions Solve Warehouse Challenges
UNEX offers warehouse storage solutions designed to solve today's top warehouse challenges. Discover the benefits of each system and how they can improve space utilization, operational efficiency, inventory management, and more.
SpanTrack: For Space Utilization, Inventory Management & Picking Efficiency
SpanTrack is a carton flow storage solution that improves productivity and accuracy on the pick line, maximizes SKU storage, and minimizes strain on order pickers. SpanTrack provides significant benefits across warehouse operations:
- Maximized Storage Capacity: Optimize every square foot of space in your warehouse with SpanTrack. These carton flow racks drop into existing pallet racks to create efficient storage lanes, allowing you to use the full height and depth of your pallet rack shelves. Store significantly more inventory in the same amount of space with SpanTrack.
- Effortless FIFO Inventory Management: These carton flow racks use gravity to move inventory from the front to back, promoting an automatic First-In, First-Out (FIFO) inventory system. This inventory management method ensures older inventory is used first to reduce waste, prevent product expiration, and maintain product quality.
- Improved Ergonomics & Lower Labor Costs: With SpanTrack, items are always within the pickers’ ergonomic “golden zone,” reducing injury, risk, and strain. For example, SpanTrack can be customized with knuckled end treatments for improved each picks, tilting products toward the worker. Increased efficiency per picker also minimizes labor costs as employees save time searching for and picking SKUs to fulfill orders.
SpeedCell: For Space Utilization, Picking Efficiency & Inventory Management
SpeedCell is a dynamic, high-density storage solution that maximizes space within standard pallet racking, helping warehouse operations improve pick speed and accuracy, while saving time and money. Discover how SpeedCell optimizes warehouse operations:
- Maximized Space Utilization: SpeedCell can compress 200’ of rack or shelving in 40’ of highly organized space, increasing storage density by 40-60%. It transforms dead and unusable space into fully utilized and profitable areas.
- Enhanced Picking Efficiency: By dramatically improving pick facings and providing easy access to every SKU, SpeedCell can reduce labor costs by up to 40%. The system’s ergonomic design allows workers to slide columns side-to-side, minimizing the time they spend searching for items.
- Improved Inventory Organization: Each cell in the SpeedCell system has a unique location label holder, increasing inventory visibility and pick accuracy. This dynamic organization system is compatible with pick-to-light, RFID, and scanner technologies.
FlowCell: For Improved Ergonomics & Efficiency
FlowCell modular flow racks are storage units and workstations designed for a facility’s unique operation. FlowCell is a flexible, ergonomic solution that boosts production efficiency by up to 30% and increases space utilization by up to 50%. In addition, these modular flow racks angle parts toward the picker to minimize reaching, improving ergonomics by reducing worker injury and fatigue.
Create customized workstations for flow-through, picking, packing, and kitting. Because of the flexibility of FlowCell, many third-party logistics facilities (3PL) use FlowCell to quickly adapt to different client contracts and accommodate various product sizes.
FlowCell provides multiple benefits that make it an essential component in enhancing your warehouse operations:
- Maximized Production Throughput: With a modular design, FlowCell can increase production efficiency by up to 30%, allowing you to streamline operations and handle more tasks in less time.
- Flexible & Scalable Storage: Easily reconfigure FlowCell units to adapt to changing operational needs, ensuring that your storage solutions can scale with your business.
- Enhanced Space Utilization: By angling parts toward the picker and maintaining a clear, organized workspace, FlowCell optimizes every inch of available space, boosting overall warehouse productivity.
Gravity Conveyor: For Reduced Product Damage & Enhanced Productivity
Reduce product damage and enhance productivity with low-maintenance UNEX gravity conveyors. These durable, efficient conveyors use gravity to safely move loads on a pitched conveying surface. Install gravity conveyors on conveyor lines, merging or diverging applications, and temporary or permanent locations to reduce manual lifting, pushing, and pulling.
In addition to enhancing productivity, gravity conveyors can be accessorized to further reduce product damage. Conveyor stops help prevent product damage by ensuring items always come to a slow stop, while guard rails can be installed to prevent large items from falling off the conveyor. UNEX gravity conveyors offer a range of benefits that improve operational efficiency in your warehouse:
- Versatile Material Handling: UNEX gravity conveyors support various applications, including assembly lines, cross-docking, and loading docks, making them essential for diverse warehouse operations.
- Low-Maintenance Durability: Built with high-quality materials, these conveyors require minimal maintenance, reducing downtime and ensuring consistent workflow.
- Customizable for Specific Needs: With adjustable width, length, and support height options, gravity conveyors can be tailored to fit specific warehouse requirements, enhancing overall operational efficiency.
Maximize Your Warehouse Potential with UNEX
If you’re struggling with poor space utilization, inventory management problems, high labor costs, or scalability issues, discover your warehouse’s full potential with UNEX. Our dynamic warehouse storage solutions and gravity conveyor systems address warehouse managers’ top challenges with practical, efficient, and affordable solutions that enhance overall performance. Contact us today to discuss the solutions and strategies that are best for your unique operation!