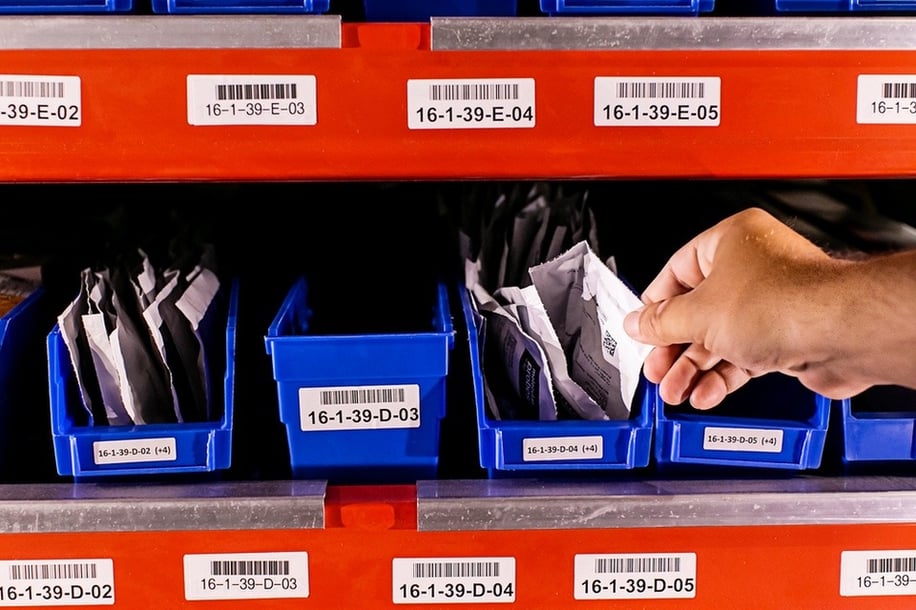
Order picking is one of the most important processes in a fulfillment center. As the first step in fulfillment, order picking sets the stage for the rest of the process. Delays or errors in order picking can quickly trickle down to packing, shipping, and delivery, ultimately affecting customer satisfaction.
While order picking is vital, many order fulfillment centers struggle with inefficiencies and disorganization. Common order picking challenges include:
- Space Constraints: Both small and large warehouses struggle with organization and space constraints, as many fulfillment centers are storing more inventory than ever.
- Errors and Delays: Outdated storage systems and inefficient picking methods can cause delayed or incorrect orders, leading to costly returns and customer complaints.
- Worker Fatigue: Poorly designed warehouse layouts often increase picker time and worker fatigue, limiting the number of orders that an employee can fulfill.
- High Labor Costs: Manual picking processes decrease picking speeds and delay employee training. Warehouses must hire more employees to meet demand, contributing to high labor costs.
It’s essential to optimize your order picking operation to avoid these challenges. An optimized picking operation can help your fulfillment center expand storage density, reduce labor costs, boost overall productivity, and increase customer satisfaction.
Strategies to Optimize Order Picking
If high pick error rates, worker fatigue, and lack of warehouse space sound all too familiar, there are effective strategies you can leverage to optimize your order picking operation. From creating designated SKU locations and choosing the right picking method to condensing storage space and improving your warehouse layout, let’s dive into each of these six strategies:
1. Designating Locations for Each SKU
Order pickers shouldn’t sort through multiple SKUs to find what they’re looking for. Every SKU in your fulfillment center should have its own designated location with a specific, clear label. Designated locations reduce travel and search time, increase picking accuracy, improve space utilization, and minimize confusion.
To assign your SKUs to their most productive locations, you’ll need to assess your entire inventory and utilize these slotting optimization strategies:
- Analyze SKU velocity: Review the orders you receive on a daily and weekly basis. Which products move quickly or slowly? Categorize inventory as slow-, medium-, or fast-moving SKUs. SKU velocity determines what type of storage is best for your products and where they should be located in your fulfillment center. For example, fast-moving SKUs are best left on a pallet and loaded into a pallet flow system, while medium-moving SKUs are typically each or case picks and should be stored in a carton flow system. Slow-moving SKUs don’t need a high-profile position in your warehouse. They should be stored in a dynamic storage system, static shelving, or tilted-pick shelving.
- Group items by popularity and affinity: To further reduce travel time, store SKUs that are regularly ordered together, so they can be picked simultaneously. This slotting strategy often works well for eCommerce businesses.
- Regularly review and adjust slotting plans: After creating your slotting plan, you’ll need to regularly evaluate and adjust it to keep up with changes in your product mix and seasonal demand.
Once you’ve analyzed SKUs and chosen designated locations, follow these helpful implementation tips to bring this order picking strategy to life:
- Label shelves and bins clearly: To keep your inventory organized and in its designated location, shelves and bins need to be clearly labeled. However, maintaining a labeling system can be challenging. We recommend choosing labels made of durable materials that will withstand the conditions in your warehouse. Pick a consistent label type: barcodes, QR codes, RFID tags, painted labels, etc., and place product labels in consistent, visible positions. Some warehouses include key product information on labels and also use colors and numbers to distinguish rack categories.
- Train staff to return items to their designated spots: A designated location system is only beneficial if your staff is up to speed on how it works. Train order pickers on where inventory is located, how it’s categorized, and how to read the labeling system.
2. Choosing the Right Method for Your Operation
There are many types of order picking methods. While there’s no “right” or “wrong” method, the best option for your order fulfillment center depends on these factors: warehouse size and layout, order volume and frequency, product diversity and SKU characteristics, and labor availability and skill levels.
Let’s take a look at the most common types of order picking methods:
- Single order picking, also called discrete order picking, is a basic order picking style where pickers focus on picking one SKU at a time. This method is usually most efficient for smaller operations with limited SKUs.
- Batch picking, also called multi-order picking, involves picking groups of orders simultaneously. This method is helpful for small items or simple orders with minimal SKUs and reduces the time needed to process SKUs.
- Wave picking occurs when a worker picks one order, one SKU at a time. But unlike single order picking, this method schedules orders to be picked at certain times in a specific wave, maximizing picking and packing operations. Wave picking is very efficient when large numbers of SKUs are picked.
- Zone picking assigns pickers to one specific warehouse zone to pick within. These workers only fill orders with SKUs in that specific area, and they pass the order on to the next zone. This process can be beneficial for operations that sell high volumes of many products.
There are a few tips you can follow to determine which method will be most efficient for your operation. First, assess your current picking operations and identify any pain points. Are order pickers gathered around popular SKUs and blocking aisles? Are employees spending too much time traveling to reach inventory? Next, conduct trials of different picking methods to determine the best fit for your fulfillment center. Even after you’ve selected a method, you may need to continually review and adjust it based on performance data or operational changes.
3. Condensing Storage Space
Many fulfillment centers struggle with wasted space and cluttered storage. Condensing your storage is one effective way to reduce picker travel times and increase storage density without compromising organization. Try swapping your static shelving systems for dynamic storage solutions to condense storage and optimize your overall picking operation.
Dynamic storage solutions increase space efficiency, storage capacity, and product accessibility. For example, UNEX offers two impactful dynamic storage systems: SpanTrack and SpeedCell.
- SpanTrack is a carton flow system — a crucial aspect of efficient order picking — that eliminates the need for manual handling. SpanTrack Lane or Wheel Bed tracks drop into existing structures and enable full case or split case picking. Its gravity-driven design ensures products move smoothly along the tracks, reducing the risk of product damage and facilitating precise inventory control.
- SpeedCell is a high-density storage solution that optimizes unused space in existing pallet rack bays. This solution dramatically increases storage capacity by 40-60%. It’s designed to store and organize a wide range of SKUs and allows workers to fully access the entire depth of the rack.
Both of these dynamic storage solutions increase storage density, while keeping SKUs organized, labeled, and accessible for order pickers.
4. Optimizing Layout to Minimize Travel Time
Your warehouse layout greatly impacts picker travel time, which affects productivity levels and overall output. A well-organized warehouse layout allows for faster picking, reduced travel time, and improved efficiency. Here are a few practical ways to adjust your warehouse layout for optimal order picking:
- Create efficient pick routes: Develop clear guidelines for pick routes and order prioritization. Establish different pick routes for types of SKUs and ensure order pickers are trained on these routes.
- Ensure sufficient aisle space and implement one-way aisles: While you don’t want to waste space with extra-wide aisles, ensure there’s enough room for order pickers to comfortably navigate and for large equipment that may need to pass by. One-way aisles can also help prevent congestion and delays in picker travel time, increasing efficiency.
- Position frequently picked items in easily accessible locations: Fast- and medium-moving SKUs should be located in clear, accessible locations closest to fulfillment.
5. Prioritizing Ergonomics and Safety
Your employees are essential to your operations. However, repetitive activities such as bending and reaching can increase the risk of back injuries and even slow pick rates. An optimized picking operation prioritizes ergonomics and safety to reduce worker injuries, improve productivity, and increase job satisfaction.
How can you improve ergonomics in your picking operation? Here are a few solutions:
- Try adjustable workstations, ergonomic picking tools, and proper shelving heights. Adjustable workstations are one easy way to improve ergonomics — they can be raised or lowered to a comfortable height. Ergonomic picking tools and proper shelving heights improve product accessibility and help prevent unnecessary reaching and straining.
- Utilize conveyors and mobile picking carts to reduce fatigue and protect products from damage. While order pickers can manually move products, equipment such as gravity conveyors can help ease the strain on workers. Mobile picking carts, like UNEX SpeedCartt, can help order pickers fulfill orders multiple orders at once without carrying heavy items.
6. Utilizing FIFO Fulfillment Solutions
First-in, first-out (FIFO) is an inventory management system that can increase pick and stock speeds and improve overall order fulfillment. While order pickers fulfill orders from the front, employees can load inventory from the back, ensuring the oldest inventory is always used first. This helps reduce waste, which is essential for businesses selling perishable inventory.
To implement FIFO, we recommend leveraging a dynamic storage solution like carton flow. Unlike static pallet locations or static shelving, where loading and picking happen from the front, dynamic carton flow allows for front order picking and rear loading. These systems ensure stock is regularly rotated to help maintain order and organization.
UNEX Solutions to Optimize Order Picking
We offer a variety of dynamic storage solutions designed to improve organization, condense storage space, increase ergonomics, and utilize FIFO fulfillment. Discover how each of these solutions optimizes order picking:
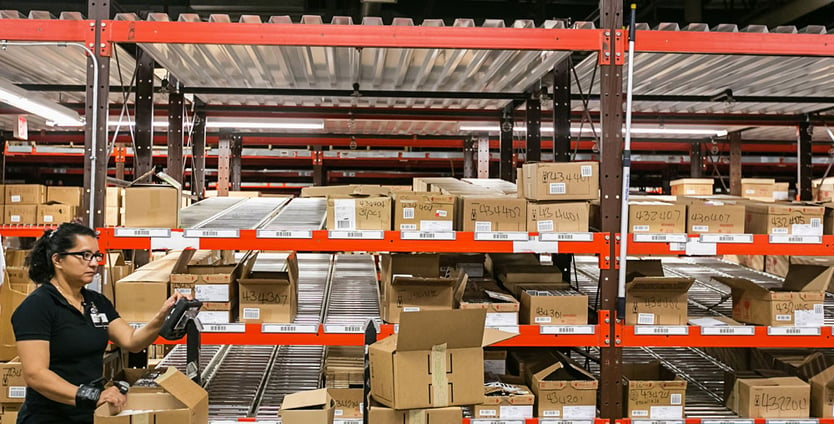
SpanTrack: Carton Flow Solutions
SpanTrack is a durable, reliable, and innovative carton flow solution that drops into existing structures, creating efficient carton flow. Here’s how it benefits order picking:
- Maximizes SKU storage: SpanTrack can be added to any new or existing pallet rack and provides the flexibility to store products with a wide variation in weight and size.
- Improves productivity and accuracy: SpanTrack ensures products are always at the pick face, reducing the time it takes to find products and increasing overall throughput.
- Reduces strain on pickers: SpanTrack can be configured with adjustable pick trays, presenting open cases to order pickers, so they can easily pick orders without bending or reaching.

SpeedCell: High-Density Storage Solution
SpeedCell is a dynamic, high-density storage solution that increases pick faces while improving pick speed and accuracy. SpeedCell helps optimize order picking operations by:
- Maximizing space utilization: SpeedCell transforms wasted, disorganized space into usable, SKU-dense storage. This solution can compress 200’ of rack or shelving into 40’ of highly organized space that’s easy for order pickers to navigate.
- Reducing travel time: More pick facings and great SKU density mean less travel time while pulling orders and restocking locations.
- Enhancing organization: Each “cell” has a unique location label holder, making it easy for order pickers to locate products, no matter the picking method.

FlowCell: Modular Flow Rack Solution
FlowCell workstations are modular, dynamic storage units designed specifically for a facility’s unique operation. These durable and flexible storage units support Lean principles by keeping inventory organized and maximizing pick efficiency. Not only is FlowCell beneficial to order fulfillment, but it is widely used in manufacturing environments. These are a few benefits of implementing FlowCell in any operation:
- Maximizes space: FlowCell increases space utilization by up to 50% by keeping inventory organized and properly stored. It boosts production efficiency by up to 30% by angling parts toward the worker, creating an efficient and accessible pick point.
- Improve ergonomics: It also minimizes reaching and improves ergonomics, reducing order picker injury and fatigue.
- Ensures FIFO inventory rotation: FlowCell replenishes from the back so it doesn’t interfere with the picking process in the front.

Gravity Conveyor: Roller & Wheel Conveyor Solutions
UNEX Gravity Conveyor efficiently moves loads through a facility. They’re easy to install, low maintenance, and essential to any order picking operation. Here are a few benefits of installing gravity conveyors:
- Increases efficiency and throughput: They reduce the time it takes to move products throughout a facility, resulting in faster processes and output.
- Reduces labor costs: By speeding up inefficient processes, gravity conveyors can help decrease labor costs and allow employees to focus on order picking and restocking.
- Improves space utilization: Gravity conveyors can be combined with FlowCell or SpanTrack to create efficient and flexible packing stations.
Putting Strategies into Action for Optimal Order Picking
By making strategic changes to your warehouse layout, storage systems, and inventory management, you can create a more efficient and streamlined order picking operation. These strategies will help you reduce labor costs, boost productivity, and create a safer work environment. While you may find strategies that work for your operation now, continuous improvements may be needed, which is why it’s important to invest in versatile, dynamic storage systems. To learn more about order picking and storage solutions from UNEX, contact us today!
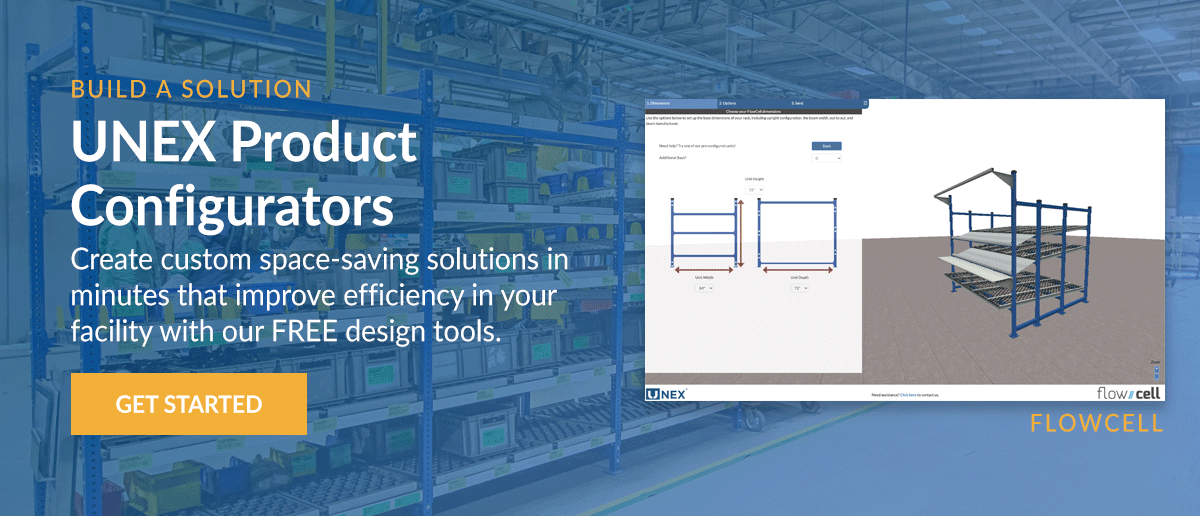