Improving Productivity with Lineside Storage in Lean Manufacturing
Today's fast-paced landscape has transformed manufacturing efficiency from a luxury to a lifeline. In response, lean manufacturing principles that prioritize waste reduction and efficiency gains have seen a boom in popularity among forward-thinking operations. Lineside storage – or the strategic placement of materials, tools, and components near the production line – has become especially critical for enabling efficient material flow, reducing waste, and optimizing space utilization.
Let’s explore how lineside storage can significantly reduce waste and enhance productivity in manufacturing operations just like yours.
Understanding Lean Manufacturing
Before we dive into lineside storage, let’s brush up on the basics. Lean manufacturing revolves around eliminating waste, enhancing efficiency, and using customer sentiment to define, determine, and gauge value.
A few examples of lean manufacturing’s guiding principles include:
- Eliminating waste, delays, and bottlenecks
- Exposing unnoticed waste using Value Streams
- Continuous investment in refining and enhancing processes
- Aligning production with customer demand rather than arbitrary metrics
Download The Lean Manufacturing Storage Guidebook
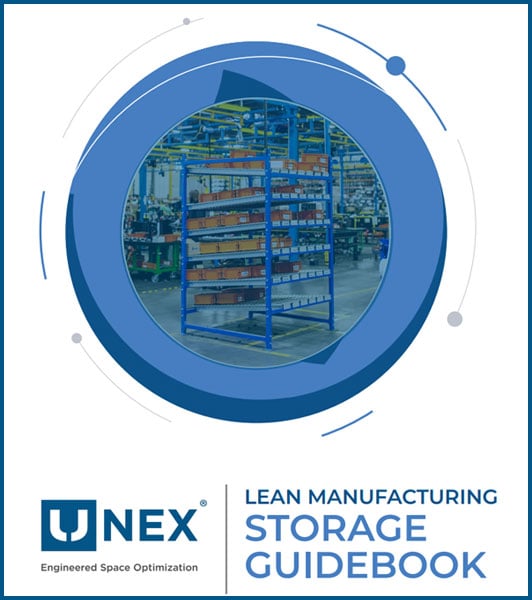
The Concept of Lineside Storage
Lineside storage is a tried-and-true concept that aims to enhance manufacturing outcomes by mitigating or eliminating the need for workers to slow or stop production to retrieve essential tools, supplies, or resources stored in far-off areas.
Lineside storage accomplishes this by strategically storing manufacturing components and materials right next to the production line. This simple approach comes with a host of benefits, like:
Reduced Handling Time: Positioning materials near where needed minimizes the time spent moving items around the factory. This cuts down on unnecessary delays in production.
Enhanced Just-In-Time (JIT) Practices: Lineside storage aligns perfectly with JIT manufacturing, ensuring that components are available exactly when needed, reducing inventory carrying costs.
Improved Quality Control: Having materials at hand allows for better oversight. Errors can be spotted and corrected quickly, maintaining the integrity of the manufacturing process.
Increased Flexibility: By keeping essential materials close to the assembly line, it's easier to adapt to changes in production, whether it's a sudden rush order or a shift in design requirements.
Reducing Waste with Lineside Storage
Waste reduction belongs at the heart of every efficient manufacturing process.
Every aspect of waste, whether it's excess inventory, overproduction, or even wasted time, negatively impacts the bottom line. Let's explore how lineside storage can help you tackle common types of manufacturing waste, like:
- Defects
- Waiting Time
- Overproduction
- Excess Inventory
- Unnecessary Movement
Defects: Lineside storage carefully stores production materials to prevent damage and promote quality control measures, minimizing defects.
Waiting Time: Lineside storage dramatically reduces idle time, downtime, and waiting time in the manufacturing process by ensuring quick and convenient material availability.
Overproduction: Lineside storage eliminates overproduction using strategies like pull-based, Kanban production systems to visualize your production processes, making it easy to manage flow, align production with customer demand, and reduce bottlenecks.
Excess Inventory: Lineside storage minimizes excess inventory, reduces carrying costs, and mitigates stockouts by supporting Just-in-Time inventory practices.
Unnecessary Movement: By positioning frequently used materials closer to the production line, lineside storage minimizes travel time and worker fatigue, cutting both wasted time and resources.
Improving Productivity through Lineside Storage
Lineside storage, when implemented correctly, creates a one-two punch of productivity-boosting benefits.
Manufacturers can mitigate or eliminate painful drains on productivity by removing unnecessary costs, travel, and waste. Then, by promoting enhanced workflows, optimized space utilization, accessibility, collaboration, and flexibility, lineside storage promotes habits, behaviors, and practices that boost productivity.
Let’s explore how these benefits impact manufacturing further!
- Cost Reductions
By storing materials closer to the production line, manufacturing operations can significantly reduce labor costs by eliminating inefficient and time-intensive travel. Lineside storage also saves manufacturers money by reducing workplace injuries related to retrieving and transporting goods. - Enhanced Workflows
Lineside storage is pivotal in ensuring a smooth flow of materials to the production line, minimizing delays and interruptions. This steady stream not only creates a more consistent production process but directly impacts productivity by reducing downtime. - Space Optimization
The strategic use of lineside storage often results in more organized space utilization. The production line can function efficiently by optimizing the factory layout to incorporate lineside storage, creating a productive environment where everything is in its right place. - Waste Reduction
Lineside storage's approach to using exactly what's needed when it's needed diminishes the chance of overstocking and waste. This not only leads to cost savings but also promotes a productive workflow where resources are used judiciously. - Collaboration and Accessibility
Having all materials readily accessible improves communication between different departments and teams. This enhanced collaboration fosters a more cohesive working environment, leading to higher productivity levels across the board. - Enhanced Flexibility
Lineside storage enables a more flexible production process, allowing manufacturers to adapt to custom orders and emergent client needs quickly and efficiently where applicable. This adaptability ensures that production lines can meet various demands without losing productivity, making it a versatile tool in the ever-changing manufacturing landscape.
Key Considerations for Implementing Lineside Storage
If you’ve been considering optimizing your lineside storage, make sure you consider these essential factors first:
Space Utilization and Layout Design: You’ll need to optimize your lineside layout to make the best use of your available space, considering your flow of materials, worker placement, and proximity to production lines.
Ergonomic Considerations for Workers: Be sure to design storage areas with workers' comfort and safety in mind to reduce fatigue, enhance efficiency, and avoid injuries.
Material Replenishment Strategies: Make sure you have systems in place to support faster material replenishment as your flow of materials changes.
Lineside Storage Solutions & Best Practices
Lineside storage isn’t just about placing materials near the production line – it's about intelligent, strategic manufacturing management. UNEX’s manufacturing solutions have been leveraged by operations to maximize their work space’s efficiency.
One solution for optimizing lineside storage and workflows is UNEX FlowCell flow racks. Flow racks are durable, modular racks that can be customized to a facility's unique operations and configured in various ways to support lineside processes. FlowCell offers lineside flexibility by delivering inventory and components directly to production lines, maintaining product organization, and maximizing space utilization.
The modular construction allows FlowCell to adapt to accommodate line and process changes. Units can be scaled up or down, rearranged, and expanded over time. FlowCell can serve as lean workstations right at lineside, providing direct inventory and components where needed while supporting just-in-time principles to minimize waste, movement, and excess inventory in production.
When considering modular flow racks for lineside storage, you should keep the following questions in mind:
- What are your space and layout requirements?
- How are your parts getting to the line?
- How much storage capacity do you need?
- What are the weights of the items you’ll be storing lineside?
- Do you need the flexibility to accommodate different-sized bins and totes?
- Is FIFO or inventory rotation important in your production process?
Three Tips for Maintaining Lineside Storage Systems
Conduct Regular Audits: Continuous inspection and assessment of the storage systems ensure they remain aligned with production needs.
Commit to Employee Training: Continuously empower your workforce with the knowledge and skills they need to effectively harness the benefits of lineside storage.
Implement 5S: Applying the 5S method (Sort, Set in Order, Shine, Standardize, and Sustain) to lineside storage areas will create a more organized and efficient work space.
Integrate Lineside Storage with More Lean Manufacturing Practices: Lineside storage doesn't function in isolation; its true potential is unlocked when integrated with other lean manufacturing practices.
Whether that means implementing Kanban production principles or embracing Just-In-Time manufacturing, manufacturers have plenty of options for using lineside storage as a launchpad for creating a comprehensive lean manufacturing strategy.
Harness the Power of Lineside Storage
Lineside storage is a practical solution to real-world manufacturing challenges that, when implemented correctly, provides a decisive advantage over the competition. To learn more about the benefits of implementing efficient lineside storage systems or to get started with FlowCell, contact UNEX today!
Flowcell Configurator
From flow-through workstations for assembly and order fulfillment to mobile carts and presentation racks, customize FlowCell modular flow racks to meet the specific needs of your operation.